无心磨床自动化上下料系统设计
2022-6-14 来源: 眉山职业技术学院 作者:林建兵
摘要: 针对无心磨床的工作原理与加工特点,设计一种自动化上下料装置,运用 PLC 控制技术对系统中供料装置、出料装置、传输机构等各部分运动状态及工作程序进行精准控制来实现产品从供料到取件的自动化、连续性生产,通过验证,该系统设计方案稳定可靠,为此类机床加工过程的自动化改造升级提供了一种有效的途径与方法。
关键词: 无心磨床; 上下料系统; 自动化
0 引言
无心外圆磨床适于磨削细长圆柱形、短轴类和套类等工件,磨削精度和生产效率高,应用较为普遍。但一些老旧式磨床因未配备自动上下料装置,在生产中采取人工供料及取件,此模式在反复操作时易出现安全事故,存在安全隐患,基于机床结构及生产特点增设配套的自动化上下料系统可有效规避此类问题,同时还可一定程度提高生产效率与产品的稳定性,提升企业自动化水平,是一种切合实际且经济有效的改造方案。
笔者提出如何在不改变无心磨床生产条件与环境的前提下增设一种自动化上下料系统来实现产品的自动化、连续性生产的加工方案,对规避人工操作的安全隐患,提升中小微企业自动化、智能化升级具有现实意义与实际价值。
1、磨床工作原理与现存问题
无心磨床工作的核心部件由两个砂轮和底部托板构成,两个砂轮中的一个为引导轮,另一个为磨削轮,工件置于两轮之间,导轮带动工件单向转动,磨削轮实施磨削加工,底部托板对工件实现支撑,三者协作完成表面磨削,加工过程一般为连续进行,加工原理如图 1 所示。
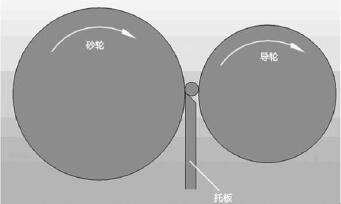
图 1 无心磨床工作原理简图
老旧磨床由于无配套自动化供取装置,工件更换时需由人工进行更换操作,长此以往易出现安全事故,虽然目前一些磨床的设备商不断投入研发自动化供料装置,并将其集成在设备中整体出售,但此类设备价格昂贵,中小企业负担困难,加之以整体更换老旧磨床成本较高,因此考虑在现有基础上改造并加装自动化上下料装置则更为现实,具有较好的可行性与操作性。
2、改造思路与基本结构
基于无心磨床的工作特点,拟设计一种自动化上下料系统配合现有机床实现全自动供料与取件,同时实现连续性生产,一定程度提高生产效率与产品稳定性。基本的设计思路为: 基于机床布局增设自动化供料与取件装置代替人工更换工件,充分融合自动传输、机械手及伺服、控制系统完成原料供给与产品传输,整体布局如图 2 所示,在原有机床的基础上,增设自动化上下料系统,建立序列化工作程序,确保加工过程连续并一定程度提高生产效率,整个系统由供料装置、传输机构、上下料装置、自动出料装置及辅助系统等部分组成,在各类支撑机构及辅助装置的配合下,各部件紧密配合、衔接有序,确保磨床连续高效工作,工作原理及工作过程简介如下。
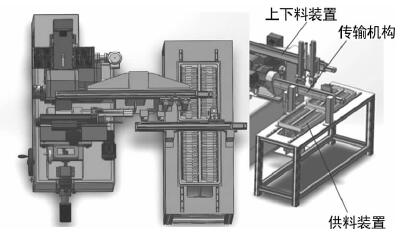
图 2 系统布局图
2.1 供料装置
供料装置由供料台、储料盘、过渡定位装置、供料机械手及导轨等结构组成,如图 3 所示,在机床合适位置放置中空结构的供料台,设 2 两个储料盘分装半成品与成品,盘内设计定位结构确定产品的排列方式与间距,储料盘通过导滑槽连接,约束运动路线,底部驱动电机控制运动状态,配合机械手执行抓取动作,机械手通过直线导轨在供料台上方水平运动,将半成品运送至过渡定位装置并回收成品。
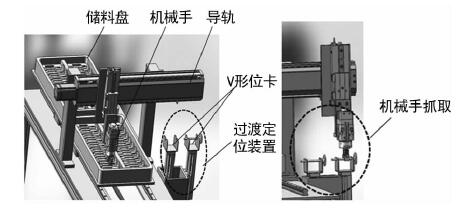
图 3 供料装置及抓取状态
过渡装置主要由两个活动气缸及和 V 形定位卡片组成,定位卡纵向位置可由气缸带动上下调整,用于放置半成品与成品,实现产品的准确供给与回收,如图 3 所示供料机械手正在进行抓取状态。
2.2 传输机构
传输机构由固定柱、直线导轨、滚珠丝杆、夹取轴、上下料机械手及驱动电机等辅助机构组成,如图4 所示,在供料装置与机床间设置固定柱,在适宜高度设置导轨与 X 伺服轴控制夹取轴和机械手横向运动,夹取机械手在伺服电机驱动下可沿夹取轴上下升降,取件时,两个夹取机械手下降到指定位置,机械手一将从过渡定位装置取来的半成品件放入磨床的砂轮间执行磨削加工,另一机械手取出自动出料装置中的成品件运回至过渡定位装置 V 形定位卡中等待回收,完成一个周期传输,如此反复,实现连续工作。
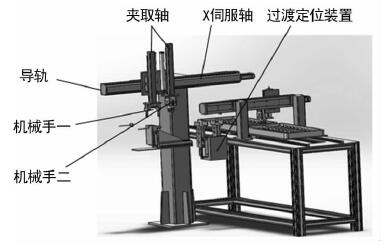
图 4 传输机构部件图
2.3 自动出料装置
自动出料装置主要用于将加工好的成品取出,该装置主要由具有定位卡槽块结构的夹具和气缸组成,如图 5 所示,出料装置可在活动气缸的带动下实现水平和上下运动,产品加工完成时,出料装置在水平气缸的带动下横向右移动至机床砂轮位置下方并确保定位卡槽位置与成品大端面对齐,上下气缸推动装置上移执行托举动作并取出砂轮间的成品件后退回至原待机位置,待上下料机械手来夹取并运回至过渡定位装置,实现产品的自动出料与传输。
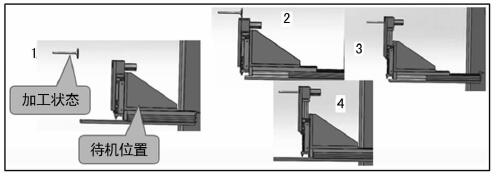
图 5 出料装置工作示意图
1.加工状态 2.出料装置前进取件 3.出料装置回退4.返回至待机位置
2.4 工作流程概述
整个自动化系统的改造以原机床设备及工作场地为基础,定点增设自动化供料装置与出料装置,配备相应动力装置、抓取机械手、传输机构,各部分装置在控制系统的操控下有序衔接并执行工序动作,完成从毛坯件送达到成品回收的一系列操作,工作过程基于 PLC 程序控制,工作流程如图 6 所示。
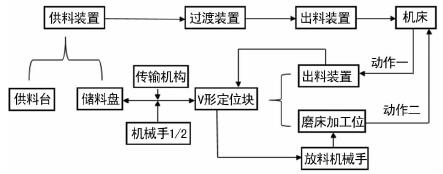
图 6 实施流程图
待加工毛坯件从供料装置的储料盘中出发,由机械手传输至过渡装置的 V 形定位卡中,由下一工序机械手抓取送至磨床加工位上方进入待机状态,待出料装置将上一周期成品件从机床取出复位后,将毛坯件放入磨削轮中实施加工,取出后的成品件再由机械手抓取经传输机构返运至过渡装置以及储料盘进行回收,如此反复,实现连续性生产。
3、系统特色与优势
(1) 生产效率明显提升。供料与取件均采用双机械手,可实现取放料的同时进行,缩短周期,系统各部分紧密配合可实现连续性生产,较大幅提高了生产效率。
(2) 系统实现全监控。各部分机构均安装了检测装置,全程监控系统的运行状态,便于过程控制与监管。
(3) 操控方便。系统运行基于 PLC 控制,触摸屏操作,方便直观、便于操作。
(4) 标准件占比高。系统机械手、传输装置、监控及控制器等均使用用标准件,标准件占比高达70%,方便系统安装及后期维护。
(5) 生产环境改动小。系统安装一般基于原生产条件,无需进行设备移动及场地更换,节约成本的同时,缩短改造周期。
(6) 具有柔性化特点。系统设计适用于各类尺寸轴类零件外圆磨削加工,可通过变换过渡装置定位卡和出料装置相关尺寸即可变换产品。
4、结语
智能制造的核心要素是生产过程自动化。在制造过程的各个环节广泛应用智能控制及自动化技术,是加快制造业发展方式转变,促进工业向中高端迈进、建设制造强国的重要举措,中小微企业占比大,进程慢,迫切需要进行数字化、自动化改造升级,上述设计方案是一种投资小、见效快的解决路径,有一定的参考与借鉴意义。
投稿箱:
如果您有机床行业、企业相关新闻稿件发表,或进行资讯合作,欢迎联系本网编辑部, 邮箱:skjcsc@vip.sina.com
如果您有机床行业、企业相关新闻稿件发表,或进行资讯合作,欢迎联系本网编辑部, 邮箱:skjcsc@vip.sina.com
更多相关信息