石横特钢超长辊套的高效加工实践
2020-5-28 来源: 石横特钢集团有限公司 作者:吴德宝
摘要:加工长辊套内孔时,一般采用镗床悬伸镗削法或车床长刀杆车削法,因镗刀杆或车刀杆伸出较长,刚性差,导致加工精度差、效率低。通过采用镗床支撑法和车床镗削法进行加工试验对比,确定采用车床镗削法加工长辊套内孔,操作简单,精度高,加工效率提高2倍以上。
关键词:超长辊套;车床;镗床
石横特钢在为客户加工一种镶嵌式超长辊套时,采用离心铸件,铸件在粗加工后多次进行热处理工艺,保证了辊套材质及硬度均匀性要求。其工艺路线为:离心铸造→粗加工→热处理→精加工辊套内孔→辊轴热装→精加工辊轴及辊套。辊套通常采用镗床镗削内孔或在车床架中心架车削内孔的加工方式,加工效率低,一直影响着交货工期要求。通过原因分析,制定了提高加工效率的有效措施。
1 、超长辊套加工效率低的原因分析
1.1 刀具系统刚性差
在镗床上镗削内孔或车床上车削内孔时,但因镗床主轴或车床刀杆伸出较长,刀杆为悬臂支撑,加工过程中刀杆受切削力作用产生弹性变形,加工内孔呈现锥孔,内孔两端直径尺寸偏差约 0.07 mm 左右,无法达到图纸设计要求。因辊套内孔两端直径尺寸偏差大,无法实现互换装配,只能先加工辊套内孔再配做辊轴,加工效率较低,配做锥度辊轴时费时费力,一直制约生产进度和加工精度的提高。
1.2 加工方法不当
由于镗刀刀杆或车刀刀杆直径受被加工孔的限制,刀杆截面尺寸相对较小,刀杆伸出较长,刚性差,加工内孔时容易产生变形和振动。为了保证镗孔质量,精镗时采用试切法,并选用比粗镗内孔更小的切削深度和进给量,并多次走刀,以消除内孔的锥度偏差。因采用较低的切削用量,导致加工效率低下。
2 、提高加工效率的措施
2.1 镗床支撑镗削法
镗床支撑镗削法就是利用镗床尾座支柱与主轴箱同时支撑镗杆镗削工件的方法。其操作步骤如下:根据镗床空间结构,制作加长主轴刀杆,刀杆中间装有镗削小刀杆。加工时,主轴加长刀杆一端插入主轴内孔,穿过辊套内孔后,另一端支撑在尾座立柱套筒中,通过调整镗削小刀杆径向伸长和工作台移动,完成内孔的镗削。
因每次加工前都必须找正镗杆前后支撑的同轴度,装夹找正复杂,用时较长。同时,镗杆外圆与立柱套筒存在回转间隙,当切削力大于刀杆自重时,刀具无论处于任何切削位置,切削力推动镗杆紧靠在与切削位置相反的套筒内表面,随着镗杆的转动,镗杆表面以一固定部位沿导套的整个内圆表面滑动。因此,导套的圆度误差将引起被加工孔的圆度误差。精镗时,切削力很小,通常小于刀杆自重,切削力不能抬起镗杆。随着镗杆的旋转,镗杆轴颈以不同部位沿导套内孔的下方摆动,直接造成了被加工孔的圆度误差。配合间隙越大,在切削力的作用下,镗杆的摆动范围越大,所引起的误差也就越大。
此外,在采用前后双导向支撑时,调整镗杆与导套配合间隙更加困难,装夹复杂,也不易采用。因此,采用镗床支撑镗削法虽然提高了镗杆的刚性和加工效率,但装夹及找正时间较长,对操作人员的技术水平要求较高,控制镗削精度比较困难,影响了加工效率的进一步提高。
2.2 车床镗削法
通过对辊套结构分析,借鉴车镗床上镗削内孔的工作原理,将普通车床改造成车镗床(见图1),实现了辊套的镗削加工。其工作原理为:辊套装夹在车床中托板上,穿过工件内孔,在车床主轴与尾座顶尖间安装车镗主刀杆,主刀杆轴上带有径向小车刀,通过刀杆主轴的转动及中托板的纵向移动,实现自动镗削内孔的工作。经过多次试验及对比,采用车床镗孔法加工辊套效率更高,操作方便,质量稳定。
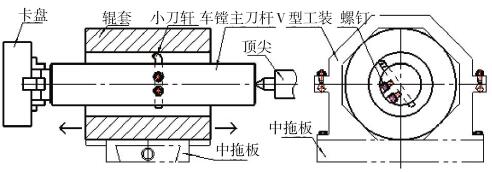
图1 车床镗削示意图
3 、辊套加工操作实践
普通车床改造成车镗床步骤:1)根据辊套内孔直径大小不同,制作专用车镗刀杆主轴,刀杆上加工出径向小刀杆安装刀孔;2)拆去普通车床小托板,在其中托板上安装 V 型工件夹持工装;3)将车床中托板 V 型工装中心调整到与车床主轴同心位置,并用定位块将中托板固定。为保证加工过程中中托板纵向走刀,预防误操作,拆去中托板手柄,将中拖板横向进给手柄锁住。
其操作方法为:1)根据辊套外径及内孔直径大小,调整V形工装,确保内孔中心线与机床主轴中心线大致重合,然后锁紧辊套外圆;2)采用一夹一顶的方法装夹专用车镗刀杆主轴,并根据工件材质及加工余量选用合适车刀;3)加工内孔时,通过调整车刀径向伸出长度,控制吃刀深度;按下纵向进给手柄,便可实现自动加工辊套内孔。
由此可知,以上改造是在不破坏车床本体的情况下,将传统车床刀杆的悬臂支撑改为一夹一顶的刚性支撑;车削内孔改为镗削内孔,提高了刀杆刚性和加工效率。
通过以上改造,辊套加工时间由 6 h 减少到 2 h以内,加工效率提高两倍以上;内孔加工精度偏差≤0.03 mm,表面粗糙度由 Ra 6.3 μm 提高到 Ra 3.2μm,完全实现了辊套内孔的互换性加工。加工操作时,将普通小车刀改为可调式机夹刀杆刀片,能明显节约磨刀时间及调整内孔尺寸时间;同时,更换不同的中拖板上夹持工装,可满足多种长通孔件的批量加工。
投稿箱:
如果您有机床行业、企业相关新闻稿件发表,或进行资讯合作,欢迎联系本网编辑部, 邮箱:skjcsc@vip.sina.com
如果您有机床行业、企业相关新闻稿件发表,或进行资讯合作,欢迎联系本网编辑部, 邮箱:skjcsc@vip.sina.com
更多相关信息