高效复合中心钻的设计与应用
2014-1-18 来源:陕西法士特齿轮有限公司 作者:唐永鹏
我公司加工生产的中间轴类零件端面有一种复合中心孔, 其作用是为后序加工用做定位基准和装配用的螺纹孔。原加工方法生产效率低, 烧刀问题严重, 精度难以保证, 机床工时费用高, 不能充分发挥机床效能等问题。近年来笔者针对加工材料为20CrMnTi ( 8620H) ,硬度为197 ~200HBW 轴类产品复杂的中心孔, 摸索设计出了高效的复合中心钻, 有效地解决了此类问题。
1. 原刀具存在的缺陷
此轴类工件如图1 所示。孔口60°倒角起着轴类产品各道工序加工定位基准的作用, 孔精度直接影响轴的后序加工质量,尤其对于弯曲及表面有缺陷的轴类毛坯件是至关重要的, 关系到该工件是否有合适的加工余量。并且在加工中孔口倒角、台阶孔、螺纹底孔必须保证同心度要求, 轴端面中心孔对轴在变速箱中安装都很重要。
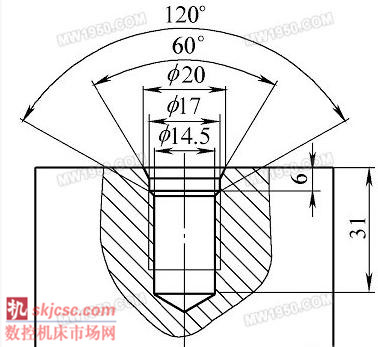
图1 制件截形示意图
原加工方法分两道工序完成, 一是先用图2 所示中心钻一次加工出孔口60°的倒角( 用于轴后序加工的定位基准) 和??17mm 台阶孔; 第二道工序用钻头加工??14. 5mm 螺纹底孔。分两道工序加工存在如下问题: 第一道工序, 刀具加工出现断屑困难, 切屑容易缠绕在中心钻60°的护锥处, 影响了切削液流入钻头部位, 切削区温度高, 很容易使钻头出现过热, 并很快磨损, 大大地降低了钻头的寿命。且切屑易刮伤已加工表面, 造成孔口倒角表面粗糙度值大, 直接影响定位基准精度要求。第二道工序, 是用麻花钻加工出??14. 5mm 的孔,容易出现孔钻偏现象, 难以满足孔同心度要求。
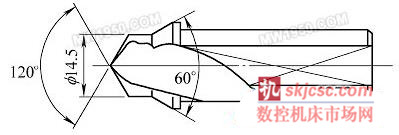
图2
两道工序存在时间长, 刀具损耗大, 机床工时费用高, 不能使机床发挥最大效能的缺陷。尤其是在市场形势一片大好, 产品供不应求的情况下是不可取的, 这就需要探索更科学更合理的加工刀具简化工序, 淘汰不科学的加工方法。
2. 高效复合中心钻的设计
高效复合中心钻加工分三部分, 如图3 所示, 前刃部是采用两刃式麻花钻头, 中间刃部是加工台阶孔刃部, 后刃部是加工孔口倒角刃部。
由于该中心钻有以下设计特点, 从而解决了以上述存在的缺陷。
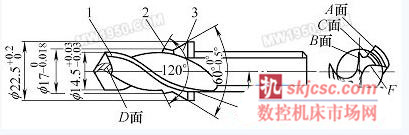
图3 高效复合中心钻
1. 麻花钻头2. 台阶孔刃3. 孔口倒角刃
( 1) 中心钻槽形采用两种25°~30°的螺旋槽形式,E 槽和F 槽有利于排出切屑均制成螺旋曲面。切削刃分别分布在两种容屑槽上, 提高了螺旋槽的锋利程度。14. 5mm 钻头前刀面B 面在F 螺旋槽上, 17mm 台阶孔切削刃C 面和60°的护锥切削刃A 面均在F 螺旋槽上。在初期试制时这两处的前刀面都在F 槽上( 见实物图4) , 便出现了两处切削部分排出的切屑发生干扰而杂乱的堆积在60°的护锥处, 烧坏切削刃, 大大降低了刀具的使用寿命。通过多次试制改进中心钻结构, 采用了E 槽和F 槽的形式后, 排屑流畅, 解决了烧刀问题。
( 2) 中心钻头部设计成麻花钻头的形式, 为了保持钻头强度和刚度, 钻头两主切削刃不通过钻头中心,而是互相平行并错开而形成横刃。不但提高了加工效率和减少工序, 而且也大大地提高了中心钻的锋利程度,减少了加工过程中钻头与工件之间的摩擦力, 延长了刀具的使用寿命。

图4
( 3) 在钻头的后刀面处磨出二次后角面, 非常有利于断屑( 见图3 所示D 面) .特殊的槽形可提高刀具的刚性, 可以改善切削状况, 也有利于排出切屑。为了保护主切削刃, 在切削刃上磨出倒棱, 增加另一个倒棱保护钻头转角和副切削刃。用特殊的结构和切削刃几何角度的钻头加工, 有利于排出碎状切屑。如果不断屑就会出现排屑不利, 从钻头F 容屑槽里出来长的切屑与中心钻护锥刃产生的切屑容易发生干扰, 杂乱缠绕在中心钻的护锥处, 易烧坏护锥处的刃口, 降低刀具的使用寿命, 大大降低加工精度。
( 4) 轴端面中心孔一次加工出来, 简化了工序,保证了中心孔的同心度要求, 提高机床利用率, 很大程度上降低了加工成本和刀具费用, 提高了生产效率。
3. 高效中心钻的合理使用
中心钻在使用过程中要根据所加工的工件材料、硬度等实际情况, 合理选择钻头的几何参数和钻削用量。
要控制在加工过程中刃口出现过热现象, 切削速度不可过高, 要提高润滑和充分冷却效果。加工一定数量的工件后, 要及时刃磨, 确保钻头锋利, 不能使钻头过度磨损, 以防烧坏切削刃而严重地影响钻头的寿命和加工孔的表面粗糙度。
合理刃磨钻头对中心钻的寿命有很大的影响, 这种新型中心钻其前端钻头相对其他部分刃口磨损较快。刃磨时注意: ①提高刀具刃磨质量, 保证各刀面有低的表面粗糙度值, 一般要求Ra = 0. 4μm, 这样可以减小切屑与前刀面和工件与刀具间的摩擦, 保证生产效率和提高刀具寿命的有效措施。②刃磨刃口还必须将后刀面磨出一个大后角( 8°~12°) , 否则就会出现钻头中心钻各后刀面与工件严重摩擦和抗刀, 不利于切削。③钻头主要刃磨两个主后刀面, 刃磨时除了保证顶角和后角的大小合适, 还应保证两条主切削刃对称, 以防止孔径扩大和孔轴线不直, 容易出现孔钻偏。④修磨横刃一般保证在0. 50 ~1mm, 以减小轴向抗力和挤刮现象, 提高钻头的定心作用和切削的稳定性。⑤该中心钻在使用中主要是断屑, 根据实践所得刃磨钻头保证横刃长0. 50 ~1mm时, 在钻头后刀面磨出6°~8°的二次后角D 面( 见图3) .两个后角面相交便出现一条棱边, 断屑效果十分理想, 便于断屑后的碎切屑在切削液的冲击下很容易从螺旋槽里排出来, 避免了切屑杂乱卷绕在刀具上, 以防止切屑堵塞而影响正常加工。
4. 结语
上述高效率复合中心钻结构设计及其合理使用的方法, 都是结合实践不断试制、不断探索、不断积累经验所得。有效地保证中心孔精度要求, 提高了产品的质量和加工效率。不但提高了机床的利用率, 而且提高了刀具寿命, 降低了刀具的损耗和刀具成本。
投稿箱:
如果您有机床行业、企业相关新闻稿件发表,或进行资讯合作,欢迎联系本网编辑部, 邮箱:skjcsc@vip.sina.com
如果您有机床行业、企业相关新闻稿件发表,或进行资讯合作,欢迎联系本网编辑部, 邮箱:skjcsc@vip.sina.com
更多相关信息