某曲轴平衡重凹槽加工技术攻关
2021-8-23 来源:- 作者:-
摘要:针对某大型曲轴生产研制以来,平衡重凹槽加工中的难点问题。根据实际情况对比分析与模拟仿真,采用车铣中心进行空间3D铣削及相位旋转与补偿的方法逐一加工,完成了6组共12个平衡重凹槽的攻关,为类似零件的研制提供了新的思路与工艺方法。
关键词:大型曲轴;配重槽;仿真;空间三维;铣削相位旋转与补偿
0 引 言
曲轴是发动机中的关键零件,起着传递动力的作用,工作时承受着复杂的交变应力,曲轴的质量直接影响发动机的动力性能和整机使用寿命。在其每一拐径上的平衡重凹槽装配平衡重,是为了平衡连杆大头、连杆轴颈和曲柄等产生的离心力及其力矩,以使发动机平稳运转,减少主轴颈负荷。平衡重一般有2种类型:第一种平衡重与曲轴连为一体,也就是与曲柄模锻为一体,设置在曲柄前端,一般用于小型曲轴中;第二种平衡重是单独设置一平衡块,用螺栓与曲柄前端面连接,常用于大型曲轴中。某平行重凹槽为空间递减3D结构,不易加工与测量,且尺寸精度与形位公差要求严格,在每拐径上分布的相位不同,加工数量多、风险高、难度大,直接影响某型柴油机装配与试验进度。1 零件结构与材料切削加工性每一零件在加工前都必须对其结构特点、技术要求、材料可切削性能等进行细致分析,找到加工的关键环节及难点所在。以根据实际情况选择机床、刀具及装夹方法,最终制定工艺路线。
1)零件结构如图1所示,其结构特点是:零件为大型轴类锻件,该曲轴的外形尺寸全长为5495 mm,总质量约为5700 kg,轴颈、拐颈外圆尺寸相同157.5 mm,每一拐颈相位相隔120°呈圆周均匀分布共2组6拐。在拐颈的两边都有一个拐臂,拐臂上的凹槽用于挂载平衡重。其工艺参
数要求:R40、R5、120°、30°、20°、159±0.2、83.5、45、Ra0.8、Ra3.2。
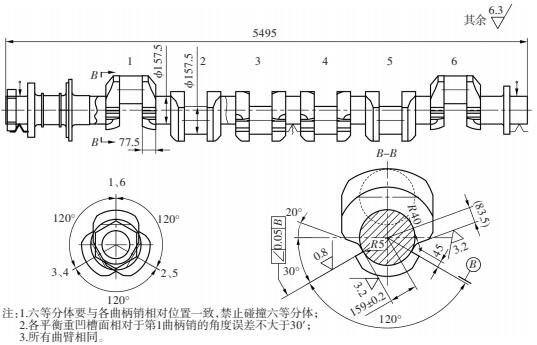
图 1 某曲轴平衡重加工示意图
2)零件材料为42GrMo,硬度41~45 HRC属于难加工材料。由于被加工零件硬度较高,刀具与零件在切削区摩擦因数增大,切削过程中产生的热量大、温度高,使硬化加剧。工件材料强度、硬度不断提高,切削力增大,致使加工刀具磨损较快,机床消耗功率过大[1]。
3)零件加工容差及检测方法。需要测量相对于基准B面的误差0.05°,表面粗糙度Ra0.8 μm,以及R40、R5、20°。基于加工后的检测要制作专用角度卡规以测量0.05°误差,R40、R5、20°可用样板测量,以照光间隙测量是否合格。
2 、加工工艺性分析
1)该凹槽不在同一加工平面内为空间尺寸,加工斜面、圆弧、底边、直角边,需连续变换相位,形位公差、线性尺寸(159±0.2、83.5)、表面质量要求高(Ra3.2 μm、Ra0.8 μm)。
2)42×R5圆弧面铣刀、D45×R0.8立铣刀加工时刀杆受到凹槽120×51×154.9尺寸限制,直径(28)小、长度(126)大,造成刚性差、强度低,切削时易产生振动 。
3)整个凹槽加工中,材料不易切削且去除率高,致刀具散热条件差,切削温度升高,使刀具的耐用度降低[2]。试切时需反复尝试改变刀路、修改切削参数、更换切削刀片,以降低切削温度,提高刀具耐磨性。
4)R40圆弧与底面和斜面相切时,42×R5圆弧面铣刀具路径需空间三轴连续多次圆弧移动,程序编制难度较大。
5)某曲轴全长5495 mm,要求相位误差不大于30′。每加工一组先要对机床进行检测,主轴径距凹槽直角面直线距离159 mm。记录误差值做出反方向差值补偿。
3、 工艺方案
1)方案1。某曲轴粗、精铣凹槽在落地FPT镗铣床加工,其加工原理是:把零件定位在V形架上并夹紧,利用六等分体手动保证相位角度,铣头旋转后逐一加工。此方案的缺点是加工误差大、效率低。手动旋转相位时,松开压紧的曲轴后慢慢转动,待端面固定的六等分体大致水平时,利用百分表找平曲臂平面在0.03 mm内,压紧曲轴加工凹槽竖直部分与R40圆角。然后旋转铣头加工20°斜面与R40相切,同时保证83.5 mm尺寸。一组加工完后,再次手动旋转六等分体及铣头120°,铣削另一组平衡重凹槽。以此类推全部加工完成。在每组铣削中需手动找正曲轴曲臂平面,费时费力,且存在铣头旋转与找正叠加误差。此方案加工效率低、尺寸误差大,质量与研制节点难以保证。
2)方案2。车间现有的HTM1251000车铣复合加工中心(如图2)是沈阳机床厂生产的,目前是国内最大的车铣复合加工中心。该机床采用西门子840D数控系统,配有左右两个旋轴B﹑C和X﹑Y﹑Z三个直角坐标,左旋转头为主头用于车﹑铣加工,通过左右转头使相位自动旋转,以有效保证120°相位角,同时在加工中利用相位的变换,缩短刀具与刀柄的长度,减少刀具费用并提高刀具刚度,有效地对侧臂与斜面进行精加工,同时对于不同拐径上的凹槽尺寸一致性好,加工精度高、质量稳定、效率高。
结合工艺要求经对比分析,充分利用车间现有技术、设备、刀具,确定为在HTM1251000车铣复合加工中心上加工。先粗铣去除大部分余量,二次开粗进行半精加工,最后利用相位角的变换进行光整加工。粗、半精、精加工分步进行,使得整个生产过程精确、高效、可靠。
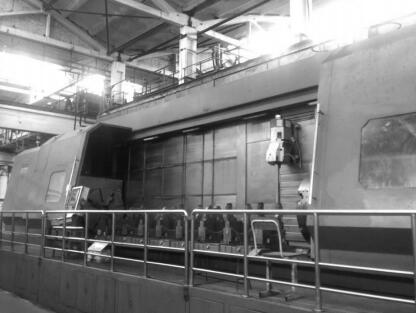
图2 HTM1251000车铣复合中心示意图
3.1 刀具选用
平衡重凹槽空间材料去除率大、形位公差小、表面质量要求高,相误差不大于30′。这就要求在刀具选择上,既要高质量又要高效率。通过对零件图样尺寸精度、材料等综合分析,选用数控机夹刀具进行切削[3]。粗、精铣选用42×R5铣刀,精铣120°侧面选用25平底立铣刀,精铣20°斜面选用50平底立铣刀。某曲轴粗、精铣单个曲臂平衡重凹槽面刀具选用表如表1所示。
表1 某曲轴粗、精铣单个曲臂平衡重凹槽面刀具选用表
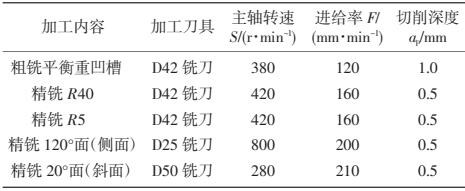
3.2 数控程序编制
数控程序的编制包括:三维模型的建立、粗精加工刀具切削参数的设定、模拟仿真、程序的导出。本程序通过以下步骤来加工整个平衡重凹槽。
1)根据图样要求建立三维模型。编写程序时所涉及的刀具位置轨迹,需在三维软件中做出曲轴平衡重凹槽数字模型。打开NX软件,进入XOY平面建立草图,绘制B-B剖视图截面,拉伸出实体即可。
2)粗铣平衡重凹槽。用 42×R5铣刀进行3D空间凹槽开粗,单边预留1 mm余量。由于材料不易加工,且要从实心处去除材料,材料去除率高。在开粗时要选用刀杆较短的刀柄,以防止切削中的振动,在切削过程中加注乳化液,从而降低切削区的温度,以减少工件变形、保持刀具的硬度和尺寸,同时利于切屑的排出,保证切削顺畅不被卡住。切削深度为1 mm,主轴转速为380
r/min,切削速度为120 mm/min,逼近速度为1000 mm/min,进刀速度为100mm/min、移刀速度为1000 mm/min[4]。
3)精铣R40。粗加工后大体的形状已加工完成,对于根部大圆角R40,用42×R5精铣刀具进行光整加工,采用拟合逐步逼近的方法。为保证表面质量,通过提高转速、降低进给量、减小步距来进行精加工,且在加工中选择步距应用在部件上,以保证加工刀路在零件上的均匀。
4)精铣R5。用42×R5精铣刀精铣R5,由于刀具圆角半径与平衡重凹槽根部相同,故顺铣一刀完成精铣加工。在加工中注意与R40圆角过渡接刀光滑。
5)精铣 120°侧面、20°斜面。精加工操作,同时旋转B、C轴,使120°侧面与主轴平行,用25立铣刀精铣出侧面并与底部R5相切。满足图样Ra0.8 μm表面粗糙度和角度误差0.05°。同理,相位角转过20°,用50立铣刀精铣出斜面与R40圆弧另一侧相切。保证尺寸83.5 mm、表面粗糙度Ra3.2 μm。
6)加工前的数字化验证。曲轴属大型关键件,加工要求高、研制风险大。为确保正确无误,要进行3D模拟仿真加工与试件实操加工[3]。为此我们制定了《曲轴平衡重凹槽三维模型与仿真模拟加工方案》,用来提前进行数字化模拟验证,来进一步确定方案的可行性与程序的正确性,以保证万无一失。加工模拟仿真如图3所示。
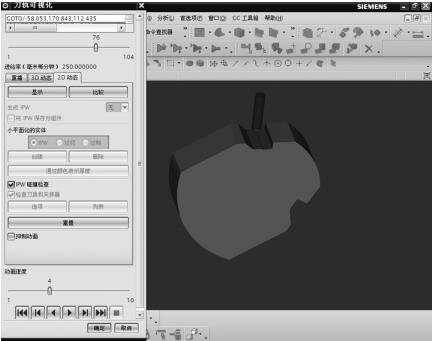
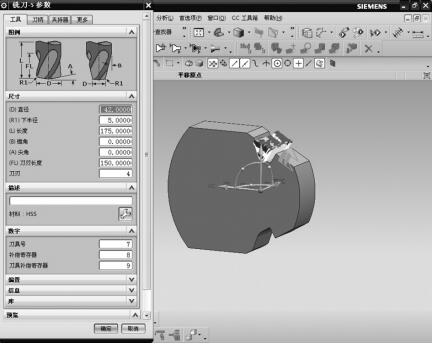
图3 加工模拟仿真图
7) 制作后处理导出数控程序。由于数控机床种类繁多,控制系统多样,每一机床的NC代码厂家自定义的指令各有不同,因此刀轨数据输出,必须经过定制的后处理生成机床可识别的指令。编写程序时所涉及的刀轨数据,需在三维软件中做出曲轴数字模型、建立曲轴中心仿真系统模块、配置刀具、选择加工策略,生成刀路、后置处理,输出程序。最终编辑为机床用数控程序。同时结合刀具、机床、零件计算理论切削参数。程序输出示意图如图4
所示。
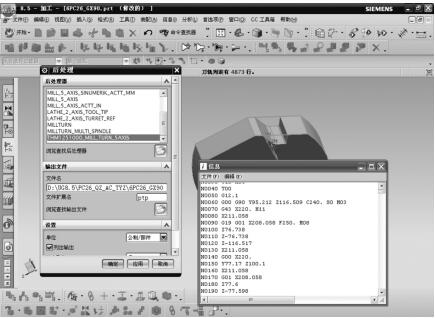
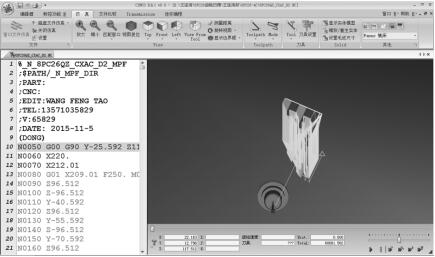
图4 程序输出示意图
4 、加工后的平衡重凹槽与专检结果
由于加工前准备充分,成品某曲轴平衡重在首次加工过程中,切削抗力小、刀具运行平稳、机床载荷均匀、相位旋转准确,加工十分顺利。凹槽加工尺寸与表面质量好。测量结果满足工艺要求,仅用了1个班次就完成了首个平衡重凹槽的加工。加工后的平衡重凹槽如图5所示。
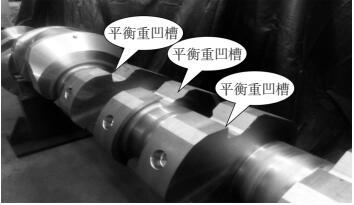
图5 加工后的平衡重凹槽图
5、结 语
通过对平衡重加工工艺的试验和技术攻关。采用数字化验证及对比加工方法进行研究后,保证了最佳方法在实际生产中的有效应用,为后续生产大型、特型零件的首件调试提供了新的工艺方法,且数字化验证较原有试加工验证更具先进性和科学性,能有效排除加工质量风险、优化加工程序、提高生产效率,并确保一次加工合格,缩短产品研制周期。
作者:王逢涛1,童勇智1,金许涛1,陈浩安1,田永维2
来源:1.陕西柴油机重工有限责任公司, 2.驻咸阳地区军事代表
投稿箱:
如果您有机床行业、企业相关新闻稿件发表,或进行资讯合作,欢迎联系本网编辑部, 邮箱:skjcsc@vip.sina.com
如果您有机床行业、企业相关新闻稿件发表,或进行资讯合作,欢迎联系本网编辑部, 邮箱:skjcsc@vip.sina.com
更多相关信息