五轴一体式转台立式加工中心设计要点分析
2022-5-7 来源:宝鸡机床集团有限公司 作者:罗海军,贾银涛
摘要: 针对用户零件工况及机床最大轴向抗力计算,提出利用三维仿真模拟对五轴立式加工中心进行变形量分析,确定出了整机为五轴一体式转台结构,有效的提高了 Z 轴空间,使得整机具有良好的刚性。重点对机床夹具、一体式转台、光机部件进行了结构要点分析,结合对转台装配过程中技巧方法的论述,力求对同类机床的设计与制造提供借鉴与帮助。
关键词: 最大切削力; 三维仿真模拟; 变形量; 五轴一体式转台
0 引 言
五轴加工中心被认为是汽车、航空、精密仪器行业加工关键部件的最重要加工设备,作为应用范围最广的数控机床技术,五轴加工中心在加工方面有着其不可替代的优点,高端五轴加工技术是我国机床行业的短板,从整体来看国内五轴加工机床市场完全被国外市场垄断。要早日实现五轴加工机床从低端到高端再到高精尖产品的转变,必须以市场为导向,紧抓技术升级,促进五轴机床产业化整体升级,因此研发一款高性能的五轴加工中心十分必要。五轴加工中心一般分为摆头式和摇篮式( 双转工作台) ,摇篮式适用于轻型零件,主轴只做直线轴运动,结构简单可靠,主轴刚性及精度也会更好[1],结合用户合作单位的汽车类轻型零件加工,笔者对五轴立式加工中心设计过程中的技术要点进行分析,选定整体结构为 3+2 摇篮式结构,为其后续的改进、批量生产提供理论依据。
1、用户零件工况分析及整机结构的确定
1.1 用户零件加工内容及计算
用户工件如图 1 为本次专项牵头单位典型产品,机床设计完成后,需完成该零件的多工序加工,零件材料为 QT400-15 ,硬度为 HB = 130-180,钻 Ф13.15锁销孔及铣外侧面 Ф22 平台,以及割宽度 10 mm 的减振器槽。
刀具选用硬质合金切槽刀直径 d0 = 125 mm,主轴转 n = 600 r/min,进给量 fz = 0.035 mm /z,背吃刀量ap = 10 mm,侧吃刀量 ae = 25 mm,刀具齿数 z = 6,计算出主轴系统所需功率[2]。
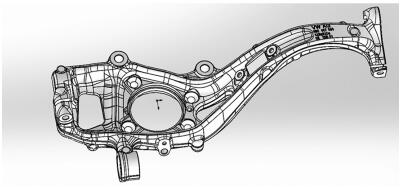
图 1 用户工件
1.2 五轴加工中心设计功率及最大切削力的确定
加工工件材料为 45 钢,刀具选用硬质合金立铣刀直径 d0 = 25 mm,主轴转 n = 1 600 r/min,进给量 fz= 0.12 mm /z,背吃刀量 ap = 8 mm,侧吃刀量 ae = 25mm,刀具齿数 z = 5,计算出主轴系统所需功率:
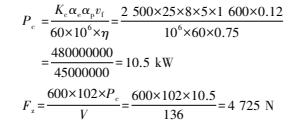
根据以上典型工况的计算,确定出本次机床的最大设计功率为 11 kW 和最大设计扭矩值为 75 N·M,主轴电机选用 FAUNC βiI 12 /12000。选取一款整体式主轴最高转速为 12 000 r/min,最大扭矩为105N,最大输出功率 15 kW,这些都满足于用户零件的加工要求。
1.3 整机的应力分析及整体结构确定
立铣刀在铣槽时,主轴系统所受轴向抗力是造成主轴箱变型的重要因素如图 1 所示,以上述大切削力铣槽工况中所计算出的切削力 Fz = 4 725 N 为算例,根据公式 F0≈( 0.5 ~ 0.55) Fz,可计算出铣削时的轴向抗力 F0≈2 500 N。
如图 2 所示机床采用的是传统的 3+2 模式,工作台和五轴转台是通过过渡板连接,转台和机床为分体式结构,这时立柱顶面距底面为 2 900 mm,受到 2500 N 的轴向抗力时,通过 Solidwords Simulation 分析其变型量最大为 0.015 7 mm。
主轴系统在受同样的轴向抗力时,通过优化五轴转台结构,使得工作台和五轴转台设计为一体式结构,这时机床结构更紧凑,稳定性更好,立柱顶面距底面降低为 2 700 mm,如图 3 所示其变型量最大为 0.010 5 mm,变型量有了明显的下降,整体刚性有了显
著提高。
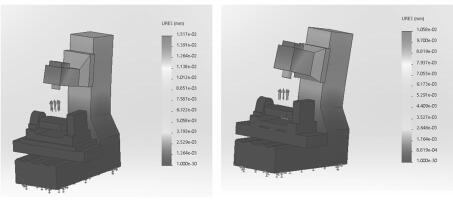
图 2 传统工作台与转台分体式 图 3 五轴一体式转台立
五轴加工中心变型量 加工中心变型量
2、机床核心部件结构设计分析
2.1 机床夹具设计
如图 4 夹具结构所示夹具本体 1 通过 T 型槽块2 与五轴一体式转台固定,用户工件 3 通过一面两销进行定位,夹紧油缸 4 负责对工件提供夹紧力,辅助支撑油缸 5 对工件提供侧向支撑力防止工件变形。液压油通过夹具本体里预留的油路,为所有液压缸提供动力,液压油管 6 接入五轴转台盘面里的油路分配器,油路分配器又与外置液压站相连接,液压站最高压力 20 MPa,具有保压和卸压报警功能,配五路电磁其中四路为单路电磁阀仅为夹具提供辅助支承及转台锁紧动力,剩余一路电磁阀为一进一出回路系统,驱动夹具上液压夹紧缸夹紧和松开。
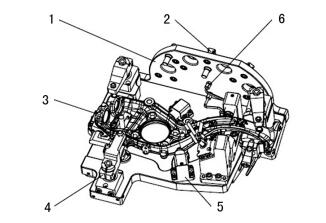
图4 夹具结构图
1.夹具本体 2.T 型槽块 3.用户工件 4.夹紧油缸5.辅助支撑油缸 6.液压油管
2.2 五轴一体式转台结构及装配要点分析
如图 5 数控摇篮一体式回转工作台为该机床的核心部件,可实现 A 轴±110°摆动,C 轴 360°回转,转台盘面 1 为直径 400 mm 带 T 型槽圆形工作台,夹具油路与盘面中心分配器连接,为压紧工件提供动力,结构美观、可靠。通过将机床工作台 3 和摇篮转台 2 设计为一体,提高了 Z 轴空间的利用率,降低了立柱的高度,使得机床具有良好的刚性,工作台底部为两组六滑块滚柱线轨结构,为工作台提供了恒久的支撑力。导轨防护 4 为工作台线性导轨及滑块提供良好的保护,避免切削液污染导轨。
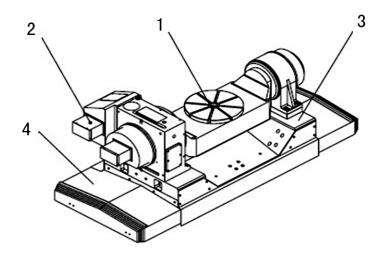
图5 一体式转台结构图
1.转台盘面 2.摇篮式转台 3.机床工作台 4.导轨护罩
在实际装配过程中必须保证一体式转台 6 个滑块安装面的等高度在 0.02 mm 以内,为了消除底面的加工误差,必要时需对底面进行刮研,由于一体式转台外形不规则并且较重,不容易进行翻转,通过计算确定出转台重心位置,如图 6 所示把刮研支架固定在转台顶部,利用转动工装对其进行翻转,使滑块安装面朝上,方便进行修配。通过对底面进行刮研,保证一体式转台底面与线轨的六个滑块保持良好接触,最后利用三组压块对滑块侧母线进行定位。
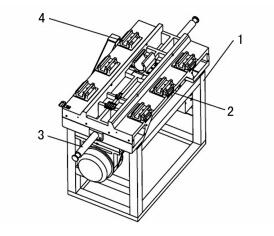
图 6 一体转台刮研示意图
1.刮研支架 2.压块 3.转动工装 4.滑块
作为测量与反馈元件的圆光栅,是数控转台保证回转精度的重要元器件,它的装配精度直接影响转台的定位精度和重复定位精度[3],本次圆光栅安装充分保证了安装后的同轴和垂直度要求,圆光栅动、定部分的间隙严格控制在 0.2 mm,A /C 轴加装了高精度圆光 栅 后,按照五轴联动立式加工中心检验标准[4],实际测得两回转轴定位精度≤0.016,重复定位精度≤0.008,优于国家标准,顺利的通过专项验收。
3、五轴立式加工中心光机部件结构解析
如图 7 机床整体为 C 形结构,采用链条式配重 1平衡方式,立柱 2 采用人字型结构,配合大跨距淬硬导轨,贴塑、刮研工艺,使摩擦阻力小,精度保持性长久。
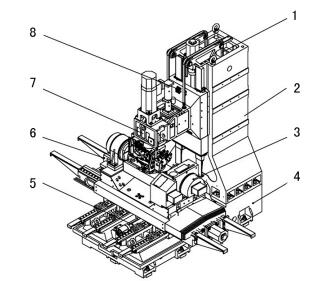
图7 五轴立式加工中心光机结构
1.链条式配重 2.立柱 3.五轴一体式转台 4.底座 5.C3 级丝杠 6.滑台 7.主轴箱 8.定量式分油器
五轴一体式转台 3 具备 A、C 轴复合功能,适合加工汽车行业复杂曲面零件。X、Y、Z 轴均采用高精度 C3 级丝杠 5 与大扭矩交流伺服电机直接传动,实现高动态特性,适宜于工件高速切削; 底座 4 上四条重载高精度线轨与滑台连接,保证整机的位置精度能达到了精密机床的标准。滑台 6 采用导轨内嵌式结构,降低了工作面到地面的高度,有利于人工操作上下料并且整机刚性更好,有效的提高了 Z 轴的加工空间和范围。主轴箱 7 采用油冷却方式,热稳定性好、精度保持性高。机床选用 12 000 r/min 高速主电机与主轴连接,主轴运转平稳,可靠。导轨、滚珠丝杠副均采用集中自动稀油润滑,各个节点配有定量式分油器 8,定时定量向各润滑部位注油,保证各滚、滑动面均匀润滑,有效的减小摩擦阻力,提高了运动精度,保证了滚珠丝杠副和导轨的使用寿命。
4、样机可靠性验证与设计应用
8 台 VM1270L 五轴立式加工中心如图 8 样机试制完成后,对其进行了负荷试验,在机床恒功率区范围内选取主轴转速 n = 1 600 r/min ,采用直径 d0 = 25mm 四齿硬质合金钢端铣刀进行铣削试验,通过改变进给速度或切削深度,使机床达到设计最大功率 11kW,此次试验过程中样机工作正常、可靠。
根据五轴联动立式加工中心技术条件和精度检验标准对样机进行了大量切削和精度检测试验,各项位置精度、几何精度及加工精度都优于国家标准。机床已在用户处加工转向节等汽车类典型零部件,使用效果良好,并且已经顺利通过国家专项验收。
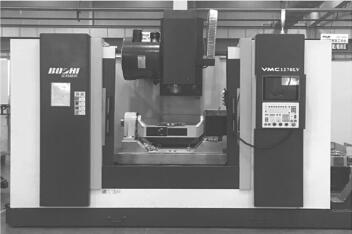
图 8 样机实物
5 、结语
汽车行业转向节、涡轮增压等技术的迅速发展和广泛应用,会带动大量适用复杂零件加工的五轴联动机床的需求,同时也为国内机床制造企业提供了机遇。本文通过介绍一款具备 A、C 轴复合功能,可实现一次装夹完成复杂曲面零件加工的五轴立式加工中心,经过对该产品重要部件及五轴一体式转台的技术要求点分析,结合样机试制完成后的大量实验数据,得出该产品是一款精度高,效率高,可显著提高机械行业的生产效率、自动化水平的设备,力求对同类机床的设计与制造提供借鉴与帮助。
投稿箱:
如果您有机床行业、企业相关新闻稿件发表,或进行资讯合作,欢迎联系本网编辑部, 邮箱:skjcsc@vip.sina.com
如果您有机床行业、企业相关新闻稿件发表,或进行资讯合作,欢迎联系本网编辑部, 邮箱:skjcsc@vip.sina.com
更多相关信息