改善传统钣金加工工艺的机器人折弯单元
2019-11-14 来源:- 作者:-
一、用户传统折弯工艺现状分析
无锡一家企业采用传统数控折弯机成形一个典型钣金件(见图1),其加工制造工艺存在以下问题:
(1)工件折弯工艺复杂,人工折弯时精度难以控制,造成折弯精度较低,产品一致性、稳定性差,不能保证后续的装配精度。(2)由于钣金零件重量大(工件重量65kg),一个工件加工时需要5个操作工来完成作业,用工成本高,工人劳动强度很大,而且不能连续作业。(3)由于折弯数多达9道,外观奇特,还需要人工翻面,所以在加工中操作困难,部件稳定性差,存在很大的危险性。(4)生产用时多,效率低,每个工件的加工用时需要15-17min。(5)生产布局及工艺流程不合理,工业视觉效果差。
二、用户钣金加工件基础技术要求及特点
该用户钣金加工件有以下技术要求及特点:
(1)工件材料:热轧板。(2)工件外形尺寸较大,原材料为不规则长方形,长度为1500mm,宽度800mm,厚度6mm。(3)工件重量达65kg。(4)工件外观造型奇特,形状复杂,在人工折弯成形加工过程中存在着很大困难。(5)折弯步序较多,有9道折弯步序,其中有三次翻面后的折弯步序。(6)折弯角度:90°及钝角折弯。(7)折弯精度:较高的稳定性和折弯角度一致性。
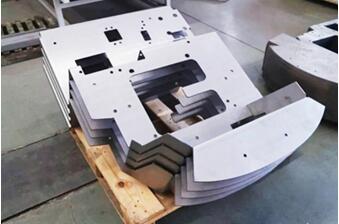
图1 该用户钣金加工件
三、机器人折弯单元的设备选型及用户钣金加工件工艺分析
1.设备选型
根据用户钣金加工件基本技术要求及特点,选型如下(见图2):
(1)选用机器人折弯单元1套,包括上下模1套。(2)选用德国原装KUKA 6轴机械手1套。(3)选用机械手伺服行走轨道1套。(4)配置磁性板料分离装置1套。(5)配置预对位定位工作台1套。(6)配置板料翻转机构2套。(7)配置磁力夹爪复合式抓手1套。(8)配置工件输送带1套。(9)安全防护1套。(10)折弯软件1套。
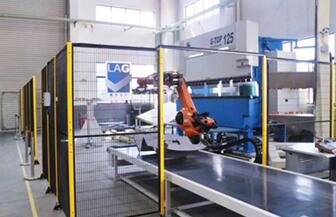
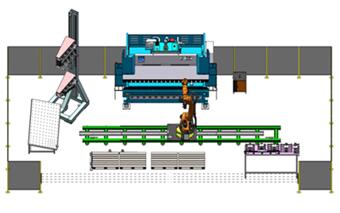
图2 设备选型
2.机器人吸盘及抓手设计选择
通过对工件折弯步序、型面、重量和工件开孔的模拟分析,设计了一套具备综合能力的抓手夹具,即磁力夹爪复合式抓手(见图3)。
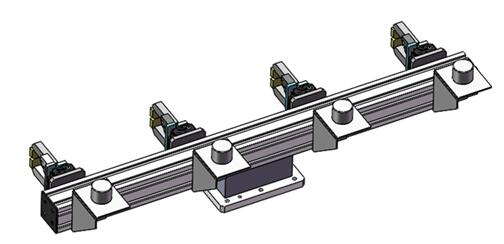
图3 磁力夹爪复合式抓手
3.折弯机模具选择
通过计算机模拟分析,根据不同型面和步序的折弯要求,折弯机模具选择:835mm×3支,按照不同步序的折弯,将模具对应分段为5组(见图4):左Ⅰ-200mm,左Ⅱ-350mm,中间-900mm,右Ⅱ-550mm,右Ⅰ-220mm。
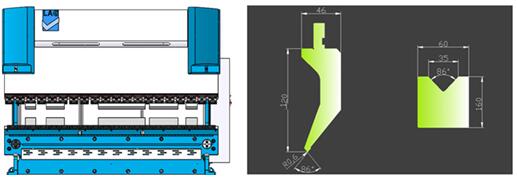
图4 折弯机模具选择(左Ⅰ,左Ⅱ,中间,右Ⅱ,右Ⅰ)
四、采用机器人折弯工艺后的主要效果
(1)成品合格率达99.9%。(2)设备可连续24h工作,保障生产的准时性。(3)排除危险,保障工件的加工稳定性。(4)只需1名工人按照作业报警器提示来操作,机器人在备好料时可按预设程序进行无人操作,无需人工干预,只有在码垛时在输送带末端接收一次工件即可,可以节省4.5名操作工,大大降低了用工成本。(5)效率显著提高,加工一个工件只需7.4min。折弯步序示意图见图5。(6)提升了制造工艺水平和视觉效果。
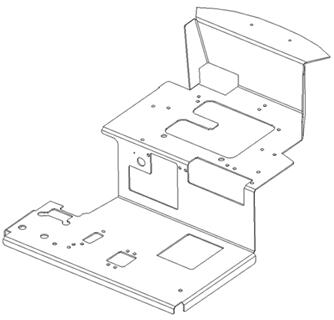
图5 折弯步序示意图
五、机器人折弯模拟演示
针对用户工件,工程师通过计算机模拟(见图6),可以分析9道折弯步序的工况情况,包括机床主参数开启高度、行程、喉口和工作台的尺寸选择以及上下模具形状和配对组合情况,这样对于设计和实际应用有着可行的理论基础。
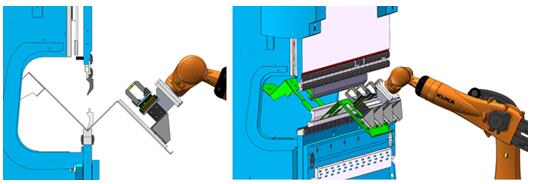
图6 机器人折弯模拟演示
六、机器人折弯单元系统特点
(1)多品种生产,产品切换无需首片测试,无需编程示教,在10min以内完成产品型号生产切换。(2)无需专业技工,只需学习能力强、善于钻研的操作工。(3)100%保证产品精度。(4)世界一流品牌部件集成,确保系统安全可靠。(5)布局合理,外观大气。
七、机器人折弯单元技术特点
1.设计研发
在机器人折弯单元设计研发中,一是要注重用户个性化需求和定制化的特点,以客户的需求为第一要务,在每个技术方案的制定中与客户进行详细的技术交流;二是对客户提供的工件加工图纸进行计算机模拟分析;三是对客户的典型工件进行现场打样试验;四是对客户的工件进行分类分析和数据处理。
在确认上述程序性工作完成后,再进行技术方案的制定,在技术方案和方案图得到客户认可后即可进行全面设计。
该机器人折弯单元采用先进的三维设计,在材料、结构、传感器、实时补偿、随动、激光角度测量、自动换模、自动换抓手、软件及控制、参数化编程、离线编程、生产管理软件和总线控制技术等方面全部采用和选用先进软硬件品牌。在折弯机机身设计方面,采用了目前世界上较先进的设计软件和设计方法,对机床进行结构力学分析,保证了机床设计的合理性、可靠性和稳定性。
2.优质材料应用
本文所述机器人折弯单元的折弯机机架承袭意大利钣金设备的用料特点,材料选用45#钢或Q345B(见图7),具有综合机械性能良好、刚性好、强度高、稳定性好的特点。
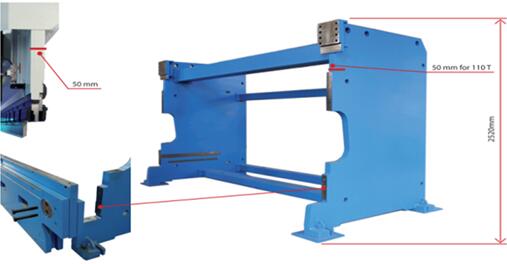
图7 机架应用优质材料
3.独特的机架结构
传统折弯机一般采用焊接式机架,包括左右立柱、下横梁(工作台)、油箱和支撑方梁采用整体焊接结构。而该机器人折弯单元中的折弯机机架没有采用焊接机架结构,而是采用独家的机架铆接技术(见图8),下横梁(工作台)与立柱之间采用高强度钢螺栓紧固连接,这种柔性连结充分保证了机身在高强度载荷情况下,能较大程度降低机架应力变形,保持机床精度的长久稳定性。
其结构特点:
(1)确保了机器无焊接应力变形。(2)提高了机器装配精度。(3)延长了机器使用寿命。(4)大幅提高了液压补偿精度。
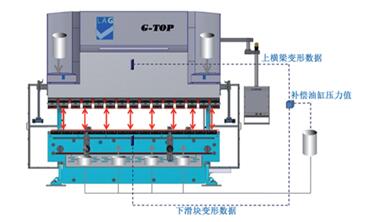
图8 独特的机架结构
4.传感器技术(精密电位计)应用
为了保证高精度的钣金折弯,在折弯机的上横梁(滑块)和下横梁(工作台)安装了传感器,在工作状态时将上、下横梁的变形量,实时准确地反馈到数控系统(PC),数控系统经过计算比对后,输出相应的补偿值驱动补偿油缸进行动态补偿,以获得满意的制件精度。
5.补偿技术(独家技术)
G-FLEX墙板比例型变补偿系统为一项专利补偿技术,无论板材厚度、长度或折弯位置等折弯条件发生何种变化,都能保证每次折弯角度在全长内完全一致,消除光栅尺的测量误差,保证机器精度。
G-CS自动挠补系统通过闭环控制,在板厚一定的折弯情况下简化了复杂的试折弯工作过程。即使折弯工件的长度不同,或者在折弯机的不同位置,都能确保折弯出来的工件具有完全一致的角度及直线度,且无需人工干预。可实现较高折弯精度和稳定性,完成实时动态补偿。
6.折弯随动技术
机器人折弯单元在折弯过程中,应对不同大小和板厚的工件,可根据折弯机滑块的运行速度进行自动跟随,自动调整。该技术由意大利LAG葛世专用机器人折弯应用软件包LK-RBC-Rev4.0来实现(见图9)。
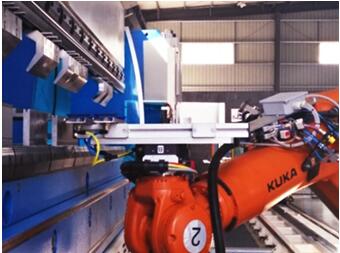
图9 折弯随动技术
7.激光角度测量技术
AMS角度测量系统通过闭环的激光角度在线测量系统,在机器人自动折弯过程中,其自动应用程序及内置激光角度测量装置的自动角度测量系统与G-CS系统配合工作,保证弯曲角精度(见图10)。其主要特点为:
(1)通过激光在线检测工件回弹后的折弯角度。(2)受力检测系统自动计算折弯回弹量。(3)工件根据下模宽度的不同可自动调整进深。(4)通过闭环的激光角度在线测量系统,保证折弯成品率达到99.5%以上。
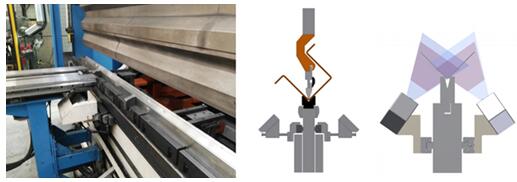
图10 激光角度测量技术
8.机器人自动换抓手、换模技术
机器人自动换抓手、换模是折弯机最先进的智能自动化操作技术之一,该技术由自动换模软件、机器人和模具库组成(见图11)。当选配自动换模系统时,精密折弯中心就能全自动随机折弯小批次的不同产品。利用自动更换模具的功能,折弯机中的模具不再成为限制因素,可全程无人处理部件。机器人自动机械装置的抓手更换模具的速度非常快,随时可折弯下批部件。
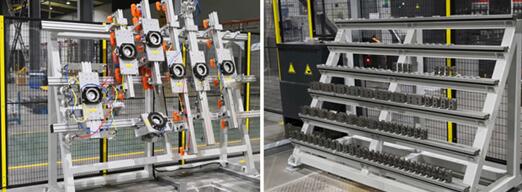
图11 机器人自动换抓手、换模技术
9.软件及控制
在机器人折弯单元中应用了参数化编程、离线编程和生产管理软件(见图12),同时二次开发了折弯随动、自动换模、自动换抓手、柔性码垛、实时补偿、板边寻边、柔性翻转技术和总线控制技术,极大地满足了各类客户钣金折弯的技术和软件需求。
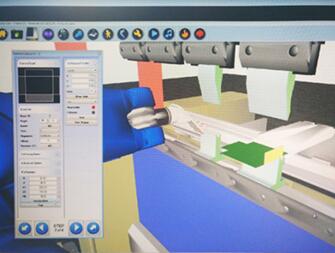
图12 软件及控制
八、结束语
通过上述机器人折弯单元改善钣金加工工艺的浅析,我们发现该技术能够显著改善传统折弯技术和工艺,可提高两倍的生产效率,实现安全无人化操作,能够减少原来90%的用工,有助于解决用户存在的钣金加工瓶颈问题,充分体现了钣金工业智能制造的优势。
(来源:《世界制造技术与装备市场(WMEM)》2019年第5期 作者:马会元 王军军 嘉意机床(上海)有限公司)
投稿箱:
如果您有机床行业、企业相关新闻稿件发表,或进行资讯合作,欢迎联系本网编辑部, 邮箱:skjcsc@vip.sina.com
如果您有机床行业、企业相关新闻稿件发表,或进行资讯合作,欢迎联系本网编辑部, 邮箱:skjcsc@vip.sina.com
更多相关信息