基于UG的机座注塑模设计与数控加工
2018-2-7 来源: 陕西工业职业技术学院材料工程学院 作者:董海东
摘要:针对机座的结构特点,在UG8.5的软件平台上,利用UG/MoldWizard模块,采用一模二腔方案,设计与产品参数相关的三维实体注塑模具。利用UG/CAM模块,分析了模具型腔的数控加工工艺,生成刀具加工轨迹并进行模拟仿真,最后生成数控程序。结果表明,实现了模具设计与制造的一体化,缩短了模具制造周期。
关键词:UG;MoldWizard;注塑模;数控加工
0 引言
当今,CAD/CAM/CAE技术在产品设计,尤其是模具设计当中的应用愈加广泛。其中,uG作为集成化的CAD/CAM/CAE系统软件,为工程技术人员提供了非常强大的应用工具,这些工具包括产品设计、工程分析、绘制工程图、模具设计以及数控编程加工等。
对于注塑模具中比较复杂的型芯或型腔,利用UG软件提供的uG/CAM模块,可完成平面铣、型腔铣、固定轴曲面轮廓铣等数控编程,从而实现了模具设计与制造的一体化,使模具
在设计的同时就可进行制造阶段相应的数控编程工作,缩短了模具制造周期‘1。
1 、塑件分析
如图1所示产品为机座,四周各有≯46 mm的连接孔,上部中央有高度为7 mm的突起部分,突起部分中部有18 mm的通孔。突起部分的右侧设置17 mmX 7 mm×3 mm的筋板以加强支撑,筋板右侧设置有妒18 1Tim的圆弧凹槽,其高度为8 mm。机座整体规格为98 mm×66 mm×15 mm,由于机座的外观要求很高,不能有熔接痕、浇口痕和顶出痕等缺陷,决定采用侧浇口即二板模结构,顶出机构采用推杆脱模。机座材料为ABS,密度为1.02 g/cm3,收缩率为0.3%~0.8%,ABS由丙烯腈、丁二烯、苯乙烯3种成分组成,具有良好的表面硬度、耐热(a)上部结构2模具结构设计要点性、耐化学稳定性、优良的成型加工性和着色性能[z]。应严格控制成型的主要工艺参数,选择震雄JNl68一E螺杆式注塑机,螺杆直径45 mm,螺杆转速0~180 r/min,注射压力147 MPa,锁模力1 680 kN,直通式喷嘴,喷嘴温度260~320℃,模具温度80℃,注射压力30~120 MPa,保压力15~25 MPa,注射时间5~10 s,保压时间5~10 S,冷却时间10~20 S,周期20~40 S。
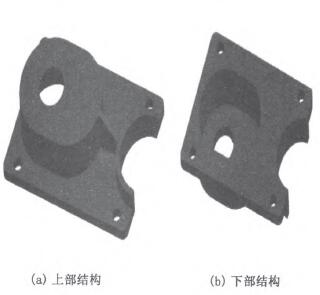
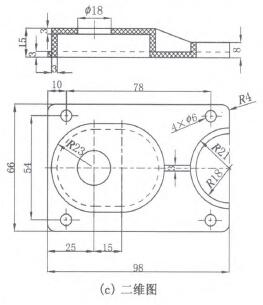
图1 机座
2、模具结构设计要点
2.1分型前准备
要进行注塑模具设计,首先导人机座零件模型,如图1所示,该模型是在UG/Model模块中创建。接着建立模具坐标系CSYS,通常模具CSYS的原点放置模架的中心,足y平面是分型面,Z方向是脱模方向。然后选择塑件的材料,定义收缩率,机座材料为ABS,收缩率大小为1.005。最后确定模具毛坯的大小为150 mm×115 mill×50 mm,并定义为一模一腔结构,如图2所示[3]。
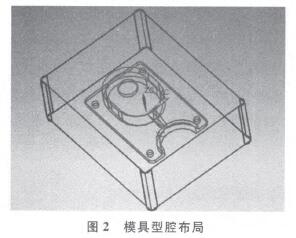
2.2 塑件的分型设计
分开模具能取出塑件和浇注系统凝料的面称为分型面,在创建分型面之前,需要修补片面、建立分型线。分型面创建完毕,就可以自动创建型芯和型腔。
2.2.1 修补片面
在分型之前,如果塑件存在通孔或碰穿面,需要进行修补,才能保证顺利分型。利用注塑模工具中的“边缘补片”功能,对4个≯6 ITlm孑L、1个妒18 mm孔等5个开放区域进行补片,如图3所示。
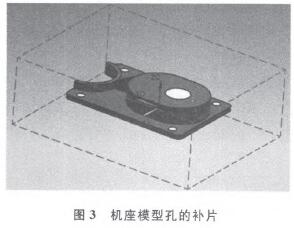
2.2.2建立分型线
分型线可采用自动或手工方式完成。对于本实例,采用自动搜索分型线,如图4所示。
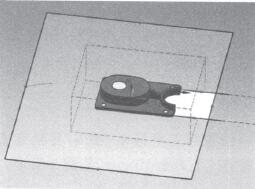
图4分型线
2.2.3创建分型面
分型面是用来修剪毛坯工件的片体,从而生成模具的型芯和型腔。MoldWizard提供的创建分型面的方式有拉深、扫描和有界平面等。由于图2所示的分型线不在同一平面上,需要定义过渡点或过渡对象将分型线划分成更小的分型段,然后把各分型段以不同的方向拉深成分型面,最后缝合成一个完整的分型面,如图5所示。
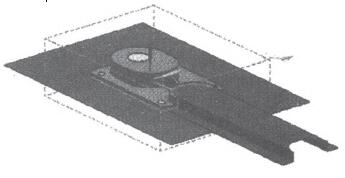
图5 分型面
2.2.4创建型芯和型腔
分型面创建完后,使用“抽取区域和分型线”功能,必须保证显示的总面数等于型芯面数与型腔面数之和。然后MoldWizard可自动创建型腔和型芯,分别如图6、图7所示。
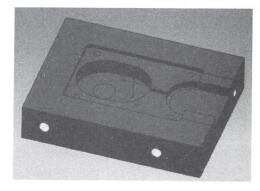
图6凹模
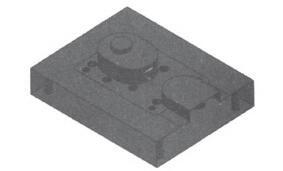
图7型芯
2.3后续处理
图7型芯型芯和型腔创建完毕后,需要根据模具毛坯的尺寸选择模架,模架必须把型芯和型腔嵌在内部,并留有足够的外沿部分。浇注系统的设计,包括选择定位圈和浇口套、设计分流道和浇口;然后进行推出机构和冷却系统的设计等。最终的机座注塑模二维装配图、三维结构如图8所示。
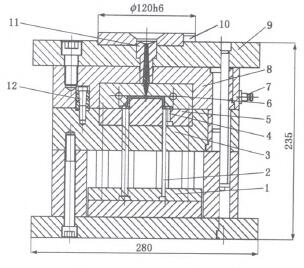
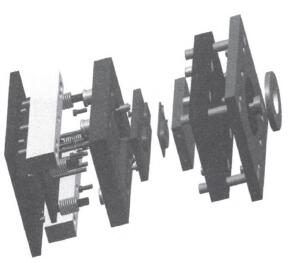
1.顶杆固定板2.顶料杆3.型芯固定板(B板) 4.小嵌件5.型芯6.型腔7.冷却水管接头
8.型腔固定板(A板) 9.定模座板10.定位环11.浇口套12.拉销
图8机座注塑模结构
3、模具的数控加工
数控编程的核心是计算刀位点,对于包含复杂曲面的产品,人工计算数控加工刀位点非常困难。而UG/CAM模块可自动编程,从而产生数控加工代码r4]。
下面以机座注塑模的型腔为例,来分析其数控加工编程过程。
3.1 型腔加工工艺分析
虽然UG/CAM模块可自动编程,但用户需要自行进行工艺的分析,工艺分析合理与否,影响模具的制造精度。具体包括:毛坯选择、工艺路线拟定、刀具选择和切削用量确定等。
型腔毛坯六面平整,尺寸为150 mm×115 mm×50 mm,材料为45钢。拟定了如表1所示的工艺方案。
3.2刀具轨迹生成过程
(1)创建加工坐标系MCS,并指定安全平面,距离毛坯上表面10 mm,如图9所示。
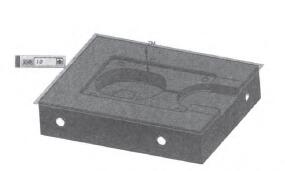
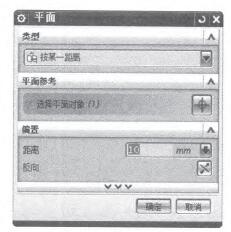
图9创建加工坐标系MCS
表l 加工工艺方案
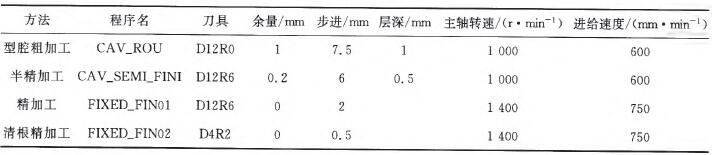
(2)指定部件几何体和毛坯几何体。
(3)创建刀具。
(4)根据拟定的工艺方案,分别创建加工操作;生成的型腔粗加工轨迹如图10所示。
(5)仿真加工,所有的刀具轨迹生成完后,进行数控模拟仿真。结果如图11所示。
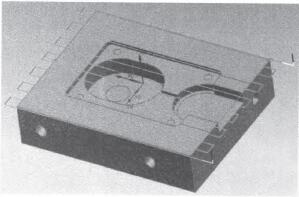
图10型腔粗加工轨迹
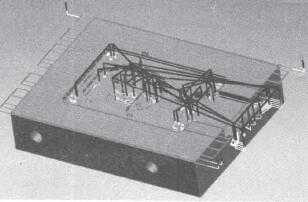
图11 型腔模拟仿真加工
3.3 后置处理
经过刀具轨迹计算产生的是刀位源文件(简称CLSF),而不是数控程序,因此需要把刀位源文件转换成特定机床能执行的数控程序,输人数控机床的数控系统,才能对零件进行数控加工,这个过程即是后置处理。图12为在采用三轴机床、FANUC操作系统下,利用UG/Post后处理生成的粗加工程序。
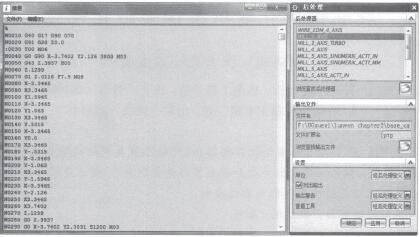
图12粗加工程序
4 、结论
以UG/Moldwizard和UG/CAM模块为平台,完成了机座注塑模具的设计和模具型腔的数控编程加工。CAD/CAM/CAE技术在模具设计和制造中的广泛应用,改变了传统的产品开发方式,大大提高了生产效果,缩短了生产周期。
投稿箱:
如果您有机床行业、企业相关新闻稿件发表,或进行资讯合作,欢迎联系本网编辑部, 邮箱:skjcsc@vip.sina.com
如果您有机床行业、企业相关新闻稿件发表,或进行资讯合作,欢迎联系本网编辑部, 邮箱:skjcsc@vip.sina.com