华中数控铣床对刀方法探讨
2021-7-2 来源: 达州职业技术学院机电工程系 作者:阳涛
摘要:数控铣床加工前必须对刀,不同的数控系统对刀的方法也有所不同。基于此,以华中数控 HNC210B 为例,阐述了数控铣床对刀的指令、方法和对刀过程。
关键词:对刀;工件坐标系;G54
数控铣床在加工之前必须进行对刀,否则数控系统无法识别编程人员设定的工件坐标系,也就无法进行正常加工。对于同一个零件的加工,不同的编程人员设定的工件坐标系原点可能不同,因此对刀时的步骤和设定方法也不同。本文以华中数控 HNC-210B 为例,说明数控铣床对刀的不同方法和步骤。
1、对刀的不同指令
对刀任务为设定如图 1 所示的工件上表面中心点作为工件坐标系原点(编程原点)。
1.1 使用坐标系设定指令 G92 对刀
1.1.1 格式
格式为:G92 X_Y_Z_。其中,X、Y、Z 为刀具刀位
点相对于工件坐标系原点的坐标。
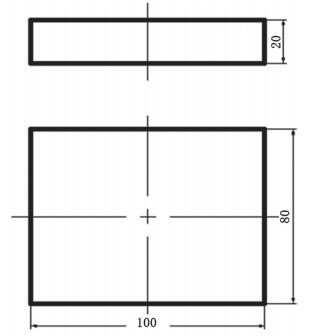
图 1 工件坐标系原点图
1.1.2 操作方法
使用手轮方式使刀具与工件左侧接触(看到有少量切屑即可,也可以使用寻边器),记下此时的机床实际 X 坐标;再使刀具与工件右侧接触,同样记下此时的机床实际 X 坐标;算出两个 X 坐标的平均值,即为工件上表面中心点的X 坐标。同理,使刀具接触工件的前侧和后侧,可以算出工件上表面中心点的 Y 坐标。再使刀具与工件上表面接触(也可以采用 Z 轴对刀器),记下此时的机床实际 Z 坐标,即为工件上表面中心点的 Z 坐标,最后移动刀具使其机床实际坐标到达前面算出的 X、Y、Z 坐标,也就是刀具位于了工件坐标系原点,因此刀具的刀位点相当于工件坐标系原点的坐标是(0,0,0),则程序中的指令为:G92 X0 Y0 Z0。
但是加工之前,刀具与工件之间不能接触,要有一定距离,比如刀具在工件坐标系原点正上方 100mm,则刀具移动的 Z 坐标要在原来的基础上加上 100mm,故刀具的刀位点相当于工件坐标系原点的坐标是(0,0,100),则程序中的指令为:G92 X0 Y0 Z100。要注意的是,在加工之前刀具不能再移动,否则建立的工件坐标系会被破坏,无法进行正常加工,这对于操作人员将十分不方便,并且还需要操作人员自己算出平均值,比较麻烦,因此一般情况下不会采用 G92 指令设定工件坐标系。操作步骤示意如图 2 所示。
1.2 使用工件坐标系选择指令 G54 ~ G59 对刀
1.2.1 格式
格式为:G54/G55/G56/G57/G58/G59。
1.2.2 操作方法
按操作面板上“设置”→“坐标系”对应功能键,进入如图 3 所示的坐标系界面,通过光标键及翻页键在G54 ~ G59 中选择,以选择 G54 为例。使用手轮方式使刀具与工件左侧接触,将光标移动到 G54 的 X 位置,如图 3所示,按下界面最后一行的“记录Ⅰ”,再使刀具与工件右侧接触,按下界面最后一行的“记录Ⅱ”,再按下界面最后一行的“分中”,则确定了 G54 的 X 坐标,将光标移动到 G54 的 Y 位置,同理可以确定 G54 的 Y 坐标。最后使刀具与工件上表面接触,按下界面最后一行的“当前位置”,注意在确定 Z 坐标前要将光标移动到 G54 的 Z 位置。程序中的指令中加入 G54,数控系统会自动调用 G54 存入的 X、Y、Z 值。由于 G54 ~ G59 对刀操作简单,不需要
操作人员计算平均值,并且加工之前刀具可以任意移动,因此通常情况下都采用 G54 ~ G59 方式对刀。
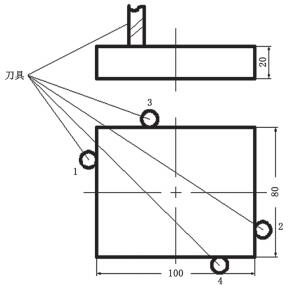
图 2 刀具操作步骤示意图
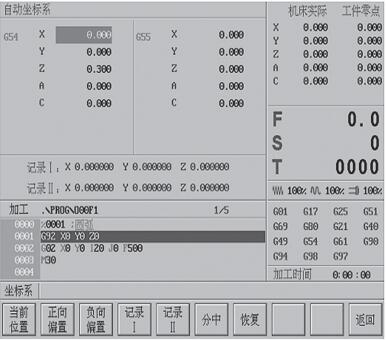
图 3 坐标系界面
2、同一工件不同工件坐标系的对刀
上述对刀任务选择的是工件上表面中心作为工件坐标系原点,而不同的编程人员选择的工件坐标系原点可能不同,还可以选择上表面的 4 个角点作为工件坐标系原点。
2.1 以工件上表面的左上角作为工件坐标系原点
如图 4,使刀具接触工件的左侧和前侧,由于刀具中心与工件坐标系原点相差一个刀具半径值,因此需要偏置。由图可知,工件坐标系原点处于左侧刀具的右边(+X 方向),故 G54 的 X 坐标应该加上刀具半径值,工件坐标系原点处于前侧刀具的后边(-Y 方向),故 G54 的 Y 坐标应该减去刀具半径值。加上或减去刀具半径值可以通过图 3 中最后一行的“正向偏置”“负向偏置”来进行。如要加上半径值,按“正向偏置”,输入半径值后回车即可;如要减去半径值,按“负向偏置”,输入半径值后回车即可。
2.2 以工件上表面的右上角作为工件坐标系原点
同理,如图 5,G54 的 X 坐标应减去刀具半径值,G54的 Y 坐标应减去刀具半径值。
2.3 以工件上表面的右下角作为工件坐标系原点
同理,如图 6,G54 的 X 坐标应减去刀具半径值,G54的 Y 坐标应加上刀具半径值。
2.4 以工件上表面的左下角作为工件坐标系原点
同理,如图 7,G54 的 X 坐标应加上刀具半径值,G54的 Y 坐标应加上刀具半径值。
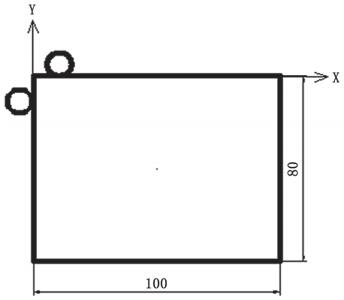
图 4 刀具中心与工件坐标系原点偏置 1
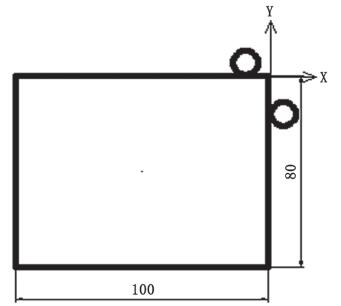
图 5 刀具中心与工件坐标系原点偏置 2
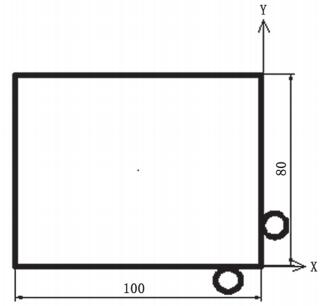
图 6 刀具中心与工件坐标系原点偏置 3
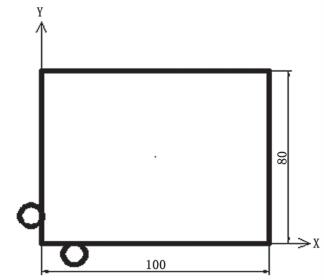
图 7 刀具中心与工件坐标系原点偏置 4
3、多把刀具的 Z 向对刀
数控铣床加工中,经常会使用多把不同的刀具加工同一个零件,理论上每一把刀具都需要对刀。对于加工同一个零件,每一把刀装夹到主轴上时,刀具的轴心线都是同轴的,因此只需要对标准刀进行 X 向和 Y 向对刀,其他刀
具不需要对 X 向和 Y 向,使用和标准刀相同的对刀值即可。每一把刀装夹到主轴上的长度不同,因此每一把刀的 Z 向必须对刀。如果把每一把刀所对的 Z 值都记下来,然后在使用每一把刀之前将 G54 的 Z 值进行修改,则非常麻烦,并且耽误时间,效率低。为了提高效率,可以采用刀具长度补偿的方法进行 Z 向对刀。
3.1 每一把刀都进行长度补偿的 Z 向对刀(绝对坐标)
将 G54 的 Z 值输入零,按“刀补”中的“刀补表”键,进入如图 8 所示的界面,然后将每一把刀所对的 Z 值输入到长度补偿里。
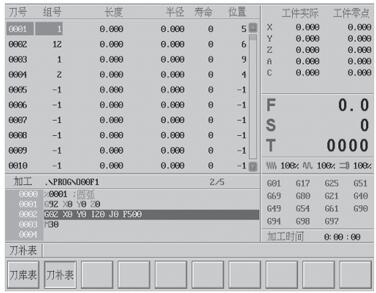
图 8 补刀表界面
3.2 设置标准刀进行长度补偿的 Z 向对刀(相对坐标)
将 G54 的 Z 值输入一号刀(标准刀)对应的 Z 值,按“刀补”中的“刀补表”键,进入如图 8 所示的界面,一号刀的长度补偿值输入零,其他刀的长度补偿值输入其与一号刀的长度差值。长度差值确定方法:一号刀与工件上表面接触,按“设置”中的“相对清零”键,进入如图 9 所示的界面,按“Z 轴清零”,再换成其他刀具,同样使刀具与工件上表面接触,屏幕上显示的 Z 轴相对实际坐标即为长度差值。
4、刀具折断后的对刀
数控铣削加工中会出现刀具折断的情况,特别是精加工时采用直径很小的刀具时,如果切削参数设置不合理,很容易断刀。断刀后,对刀的表面已经被切掉,因此可以利用 Z 轴对刀器对新刀具进行 Z 向对刀(X 向和 Y 向不需要对刀),如图 10 所示。
4.1 绝对坐标方式
将 Z 轴对刀器平放在工件上或平口钳上,先用标准刀与 Z 轴对刀器上表面接触(Z 轴对刀器指针指到零),记下此时的 Z 坐 标( 如 -388.5mm); 再换成新刀具,同样使其与 Z 轴对刀器上表面接触,记下此时的 Z 坐标(如 -408.5mm),则两者的差值为 -20mm。再计算标准刀与断刀的长度补偿差值,如为 -22.5mm,两个差值求差为 2.5mm,说明新刀比断刀长了 2.5mm,则新刀的长度补偿值应为断刀长度补偿值(如 -308.6mm)的基础上加上2.5mm。此方法比较繁琐,也容易出错,故一般不用。
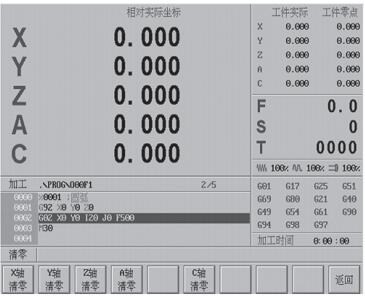
图 9 清零界面
4.2 相对坐标方式
将 Z 轴对刀器平放在工件上或平口钳上,先用标准刀与 Z 轴对刀器上表面接触(Z 轴对刀器指针指到零),按“设置”中的“相对清零”键,按“Z 轴清零”,再换成新刀具,同样使其与 Z 轴对刀器上表面接触,屏幕上显示的 Z 轴相对实际坐标就是长度差值,将其输入到对应的长度补偿值里即可。这种方法不用计算,操作非常简单。
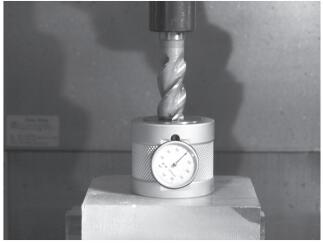
图 10 刀具折断后的对刀图
5、结语
对于不同的操作人员和不同的数控系统,数控铣床的对刀方法不尽相同。在实际操作过程中通过不断摸索,选择操作最简单、最不容易出错的方法对刀,可以起到事半功倍的效果。
投稿箱:
如果您有机床行业、企业相关新闻稿件发表,或进行资讯合作,欢迎联系本网编辑部, 邮箱:skjcsc@vip.sina.com
如果您有机床行业、企业相关新闻稿件发表,或进行资讯合作,欢迎联系本网编辑部, 邮箱:skjcsc@vip.sina.com