电火花机床主轴头的模态分析与减振设计
2018-10-18 来源:北京工业大学先进制造技术北京市重点实验室 作者: 王 民, 牛焕焕, 高相胜, 王敏达
摘要:针对某机床厂生产的 SH50电火花机床在实际工作中主轴头振动较大的问题,通过实验测试和有限元仿真相结合的方法,分析了主轴头的模态特性,并通过测试主轴头的工作振型(operating deflection shapes,简称 ODS),找出了主轴头实际工作中的薄弱环节。理论模态、实验模态和 ODS三种结果相互印证,增加了有限元模型的可信度,并以此模型为基础对主轴头进行了减振设计。模态实验中改进了传统模态实验依靠经验选取测点或均匀布点时,对经验高度依赖且实验效率较低的弊端,采用有效独立法和模态置信度(modal assurance criterion,简称 MAC)矩阵相结合的方法,实验前先进行测点优化,然后根据优化结果布置传感器和力锤位置,提高了模态实验的精度和效率。结果显示,在主轴头结构上增加一个背板,能够提高主轴头频率,远离工作频率的共振范围,起到减振的目的。
关键词 机床;模态分析;测点优化;ODS分析;减振设计
0、引言
随着模具加工的不断发展和难加工、高性能材料的不断出现,制造行业对机床综合性能的要求不断提高。电火花加工凭借其切削加工力小、加工精度较高、能够实现对超硬材料及复杂零件加工的特点,越来越受到国内 外 制造 领域 人士 的 广泛 关 注。电火花加工是一个动态过程,加工过程中的振动对工件的表面质量、加工效率、稳定性及工具电极的使用寿命等都有很大影响。因此有必要对电火花机床的动态特性进行研究,以期能够提高机床的综合性能,改善其加工精度和效率。机械结构 的动态 特性包括 模 态、阻 尼、动 刚 度等,通过对机床进行模态测试可以获得机床的动态参数。为了快速获得准确的模态参数,激励点和响应点的选取至关重要。目前大多数数控机床模态实验的激励点选择主要依靠工程经验,这不仅会延长模态实验的预实验时间,而且激励点的位置选择具有很大的随意性,若工程经验不足往往会漏掉某些重要模态。数控机床模态实验中响应测点布置方法主要采取均匀布点,均匀布点的缺点是需要大量的测试传感器,实验成本高。响应测点间的间距又需要很强的工程经验来确定,测点间距过大会影响结构的振型的判断;测点间距过密会增加模态实验时间和实验成本。Kammer提出可以用有效独立法来确定一组不依赖于经验的最佳响应自由度。根据每个候选响应点对模态向量矩阵的秩的贡献,逐步删除贡献最小的自 由 度,直 到 剩 下 想 要 数 量 的 自 由 度。陈 锋等基于 MAC矩阵,采用逐步累积法对空间桥梁载荷识别中的测点位置和数量进行了优化,提高了实验识别的精度和效率,降低了实验对工程经验的依赖。Stephan利用 Fisher信 息矩 阵,通 过 减 少自由度间的冗余,提出一种能确定飞机最佳响应自由度的方法。通过该方法选取的自由度,不仅对模态振型贡献较大,且分布较均匀,避免了测点集中分布的弊端。
为了准确获得SH50机床主轴头的模态特性和ODS振型,笔者首先利用有效独立法和 MAC 矩阵相结合 的 方 法,经 ANSYS 分 析 和 Matlab 迭 代 计算,进行模态实验前的测点优化,根据优化的测点数量和位置做模态实验和工作振型测试,得出结构的模态参数和工作 振 型;然后,通 过 模态实验 结 果 和ODS结果验证有限元模型;最后,根据 ODS分析得出的主轴头振动较大的原因,通过Isight优化平台对有限元模型进行结构优化,给出了机床主轴头减振设计的合理方案,并通过有限元仿真验证了减振设计的有效性.
1、主轴头模态分析
1.1 理论模态分析
1.1.1 主轴头有限元建模
图1所示为SH50机床的主轴头部分,主要由滑座、转接板、AR轴、直线模组、旋转头和电机组成。首先,对主轴头进行理论模态分析,对主轴头三维模型进行结构简化,删除对结构动态性能影响不大的小孔、钣金壳、圆角、倒角等小特征,以免影响网格划分 的 质 量。然 后,将 简 化 后 的 模 型 导 入 AN-SYS Workbench软件进行模态分析。外购件和标准件采用卖家提供的材料属性,其余零件采用灰铸铁材料。网格划分方式为自由网格划分,所有结合面均采用默认的 Bonded连接方式。
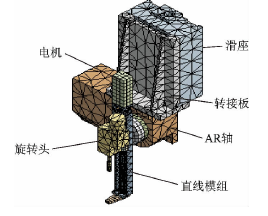
图1 SH50机床主轴头网格划分模型
1.1.2 主轴头理论模态分析
本次研究主要关心机床的低阶模态,所以设置要求解的模态数目为5,设置主轴头装配体的支撑方式为滑座底面上与滑块配合的16个孔边线为固定约束。求解可得到主轴头前五阶固有频率和模态振型,具体结果如表1所示。
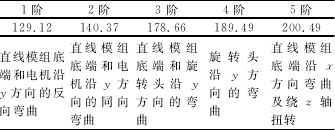
表1 主轴头理论模态
1.2 实验模态分析
1.2.1 传感器测点优化
为了改进传统模态实验精度受测点选取影响导致的精度和效率较低的弊端,本次模态实验前进行测点位置的优化 选取,以 提 高 实验的 精 度和效率。本次测点优化采用的方法是 Kammer提出的有效独立法,它是根据每个候选响应点对目标模态矩阵的秩的贡献,来确定一组不依赖于经验的最佳响应自由度。通过有效独立法虽然可以确定一组不依赖于经验的最佳响应自由度,但对于这组最佳自由度的数 目 却 无 法 确 定,因 此 又 引 入 MAC 矩阵的概念
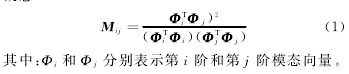
MAC矩阵非对角元元素代表了对应两阶模态向量的交角状况。若两个向量正交,那么 MAC 值应该接近于0,若两个向量完全相关,则 MAC 值应该接近于1。要想最大程度地保留振型特征,MAC矩阵非对角元元 素越 小越好。通 过对 模态 矩阵 求MAC矩阵,找出 MAC非对角元元素最大值最小时所对应的自由度数,即为测点优化的自由度数。通过 MATLAB程序输出给定数量的自由度编号,对应到 ANSYS模型中的节点位置和方向,即可达到测点优化的结果。
以滑座为例,首先通过有限元分析获得前5阶的模态振型矩阵,然后根据有效独立法和 MAC 矩阵相结合的方法在 Matlab中进行迭代计算,可得到如图2所示的变化曲线。由图2可知,当自由度为3时,滑座 MAC矩阵非对角元最大值达到极小值,即最少在滑座上布置3个传感器测得的模态参数的效果最佳。显然,这3个测点的优化结果虽然能够识别出固有频率,但无法准确识别前5阶模态振型,因此有必要再适当增加一些测点,以达到振型识别的要求。使用香农定理进行增设测点的方法为:测得结构关心模态的最高频率,估计该最高频率的半波长;在半波长的每个节点上布置一个传感器;再在半波长上等均布两个传感器.
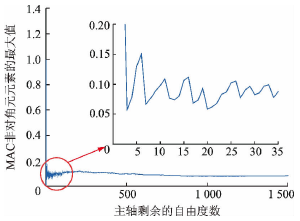
图2 滑座 MAC 矩 阵 最 大 非 对 角 元 元 素 的 最 大 值 与 滑座自由度数的变化曲线
机床主轴头滑座的长边为350 mm,通过有限元分析获得第5阶固有频率下滑座的一条长边的节点位移,再将其进行曲线拟合得到滑座变形最大的x 方向上的位移波形如图 3,从波形估计滑座的波长λ≈700mm。
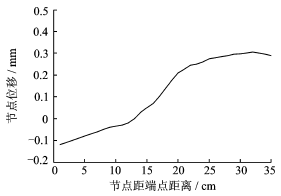
图3 滑座第5阶频率下的长边波形
使用香农定理进行增设测点后的测点优化结果见图4所示。图中编号为有限元分析中对应的节点编号。图中有标号的节点为优化得到的节点,无标号的节点为通过香农定理增加的节点。通过对比图4和滑座前5阶振型,发现通过这种方法选择的测点大都分布在零件变形较大的部位,因此这样选择的测点对模态振型的贡献最大,且满足振型识别的要求。同理,对主轴头其他关键结构也可以通过这种方法进行测点优化。
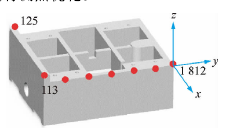
图4 滑座测点优化结果
1.2.2 主轴头模态测试
本次模态实验使用的是丹麦 B&K 公司的模态测试分析系统,采用单点拾振多点激励测试方法,即将加速度传感器固定于主轴头下端,用带有力传感器的力锤在选定的位置敲击试件,给试件一个激振力。力信号和响应信号经数据采集前端被送入计算机中 的 PULSE 分 析 仪 中,经 数 据 处 理 软 件 ME′scopeVES分析计算,得 出 试 件 频 响 函 数 及 模 态 参数。图5为在模态测试软件中建立的主轴头测试模型,红色箭头表示加速度传感器测试位置及方向,黑色箭头表示力锤激振位置及方向。
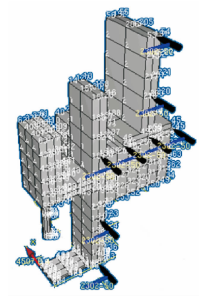
图5 主轴头模态测试模型
根据 Maxwell互异性原理,在 P 点输入所引起的在Q 点的响应,等于在Q 点相同输入的P 点的响应。因此,激励点可从优化得到的响应测点中选取,对响应测点的优化亦即对激励点的优化。通过对比实验模态和有限元模态,发现实验结果中没有与有限元第3、第4阶振型相对应的模态。仔细观察有限元振型可知,第3,4阶振型是在第2阶模态的基础上,增加了旋转头部分的振动,可以认为是旋转头的局部模态。因此取129.12,140.37和200.49Hz为主轴头前3阶理论模态。实验测得的模态参数与理论值的比较结果如表2所示。
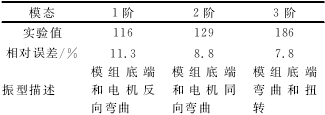
表2 模态测试结果
由表2对比结果可以发现,有限元得到的结果与模态测试得到的结果误差都在15%以下,满足工程误差的要求。实验结果验证了有限元模型的有效性,因此可以用有限元模型对结构进行仿真优化。
2、主轴头 ODS分析与减振设计
2.1 主轴头 ODS分析
2.1.1 ODS分析理论
传统的模态分析试验通常是在受控条件下进行的,然而极少有结构会在这样的条件下工作。要想了解结构 在 工 作 状 态 下 的 实 际 变 形,还 需 要 引 入ODS的概念。ODS 为 工 作 状 态 下 的 变 形,表 明 结构在某一特定工作状态下的振动状态。因此,ODS也通常被称为工作振型。ODS 不仅可以表现结构振动敏感部位的相对变形,而且可直观地识别出故障发生位置及结构的薄弱环节。
2.1.2 ODS测试结果
本次 ODS测试用机床模拟实际工况,让电极进行上下往复运动,工作频率为50Hz。如果 ODS展现的是 ODS FRF数据块中的共振峰值或者峰值点附近的振动动画,则该 ODS振型基本等同于模态振型。将 ODS分析得到的实验结果与模态实验分析得到的结果进行对比分析,以验证实验结果的可信性,然后以 ODS测出的薄弱环节对结构进行减振设计。对比结果见表3,可见两者误差基本在工程允许范围内,两种结果相互印证。
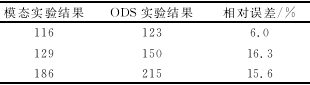
表3 模态实验与 ODS实验结果对比
2.1.3 ODS结果分析
将 ODS实验测得的加速度信号经两次积分,得到主轴头工作状态 下位移变 形曲线。在 位移 曲线中,可找到工作状态下主轴头振动幅度较大所对应的频率。 取 位 移 较 大 的 两 点 对 应 的 频 率 122 和149Hz进行分析。通过观察122和149 Hz处的工作振型,发现它们分别与主轴头1阶、2阶模态振型相似,且与主轴头1阶、2阶固有频率相差不远,因此这两处振动剧烈的原因是工作频率激起主轴头1阶、2阶模态所致。要想对主轴头结构进行减振设计,需要提高主轴头固有频率,使其1 阶、2
阶固有频率更加远离工作频率。
2.2 主轴头减振设计
2.2.1 减振设计
经过模态分析和 ODS测试,确定了主轴头工作状态下的薄弱环节。因为直线模组属细长零件,刚性较差,因此减振的关键是提高直线模组的刚度,并尽可能提高主轴头固有频率。又因为直线模组是采购件,不宜对其结构进行改动。为提高直线模组刚度,决定在其后面增加一个背板,以增加主轴头整体刚度,提高其固有频率。考虑直线模组安装定位和结构之间的连接和干涉等因素,在不影响加工方便装配、结构之间无干涉的条件下,初步设计背板为“凵”型结构。已知直线模组轨道长宽高为400mm×60mm×33mm,左右两侧的安装定位面距底面10mm。模组与背板之间采用底面和一侧面做定位基准面,因此背板可以确定的参数长为400mm、两侧翼缘高度为10mm、两侧翼缘内侧间距为60mm。为便于安装,两侧翼缘内侧间距60mm 应设计出一微小间隙。背板还需要优化的参数为翼缘厚度和背板厚度。因为机械结构的动刚度与结构有很大关系,固有频率越高,说明单位质量的结构刚度越高。在Isight优化 平 台 中 集 成lidWorks和ANSYS 文件,采用 NLPQL(序 列 二 次 规 划 法)法,以 背 板 1阶,2阶固有频率和背板质量为优化目标,对背板厚度和翼缘厚度进行优化。为使结构不致过重,根据工程经验,取板厚均 在 3~8 mm 之 间进行 迭代 优化。最终,在满足背板1阶、2阶固有频率较大和质量较小的条件下,折中选取背板厚度为5.2mm,翼缘厚度为7.8 mm,优化后的背板结构和主轴头装配图见图6所示。背板和模组之间通过底面上均布的8个螺栓孔连接,并通过其中4个孔与后面的转接盘连接。
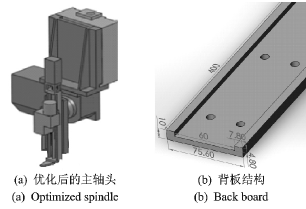
图6 减振设计结构
2.2.2 减振设计效果验证
为了验证增加背板后的减振效果,对优化后的主轴头进行了理论模态分析,结果显示,主轴头的各阶固有频率都得以提升。其中1阶固有频率理论值由原来的129.12Hz提高到162.34Hz,2阶固有频率理论值由原来的140.37 Hz提高到183.79 Hz,3阶固有 频率 理 论值 由 原 来 的 200.49 Hz提 高 到283.23Hz,都更加远离了工作频率,避开了工作频率的共振范围。主轴头各阶振型的最大变形也得以大幅度减小,达到了减振设计的优化效果。优化后的前3阶振型如图7所示。
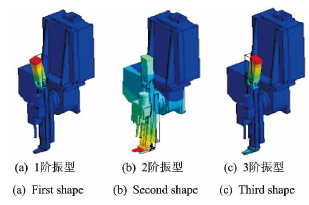
图7 优化后结构前3阶振型
3、结束语
笔者建立了SH50电火花机床主轴头的三维模型和有限 元 模 型,并 对 主 轴 头 进 行 了 有 限 元 模 态分析。使用有 效 独 立 法 和 MAC 矩 阵 相 结 合 的 方法,对主轴头进行了模态实验前的测点优化,根据优化的测点对主轴头进行了模态实验,其结果和理论结果 相 互 印 证。 在 工 作 状 态 下 对 主 轴 头 进 行 了ODS测试,找出了主轴头工作状态下的薄弱环节,并用有限元模型对主轴头进行了减振设计,验证了设计的有效性。
投稿箱:
如果您有机床行业、企业相关新闻稿件发表,或进行资讯合作,欢迎联系本网编辑部, 邮箱:skjcsc@vip.sina.com
如果您有机床行业、企业相关新闻稿件发表,或进行资讯合作,欢迎联系本网编辑部, 邮箱:skjcsc@vip.sina.com
更多相关信息