对加工中心加工气门座圈与导管孔的技术探究
2019-12-6 来源: 一汽轿车股份有限公司发传中心 作者:朱惠春
摘要:指出汽车发动机缸盖上的气门座圈和导管孔的重要性及其机械加工精度的高要求,描述了为满足此高精度机械加工要求所进行的多方面工作,尤其是通过在多条缸盖加工中心生产线中的实际加工与探讨,找出了在工艺方案、工件定位方式以及刀具选用等方面,提高其加工精度的有效途径。
关键词:气门座圈 气门导管 密封面 线性补偿
1 、前言
气门座圈和气门导管孔的加工是整个气缸盖机械加工的关键技术工艺,它直接影响了发动机的工作性能与寿命。发动机工作时,气门不断开启和关闭,气门、气门导管与气门座圈长期处于 300 ℃-800 ℃的高温状态,硬质燃烧产物、积碳、高温腐蚀和零件变形,造成气门导管与气门座圈密封锥面的磨损和烧蚀,致使气门密封不严,燃烧室气密性受到破坏,排气温度上升,发动机功率下降。这就要求气门导管有良好的自润滑性、气门座圈密封锥面有很高的耐磨和密封性。如果气门导管孔位置度超差气门阀杆工作中心发生偏移,会导致有害的热传导和气门阀杆及导管孔的很快磨损,还会造成耗油量的增加。
鉴于此,对气门座圈和导管孔的加工精度提出了很高的要求,特别是对气门座圈工作密封面对导管孔的跳动规定了很严的公差。一般发动机规定其跳动≤0.05 mm,更严格要求其跳动≤0.03 mm。
气门座圈和气门导管孔的产品要求如图 1 所示。由图可见,气门座圈密封面对气门导管孔的跳动和圆度要求均较高,同时,它们也是机械加工的关键所在。为此,当前在在大批量生产中,要满足稳定的产品要求,普遍采用在加工中心的生产线上加工气门座圈与导管孔,并在优化加工工艺,定位基准的合理性,以及刀具的选用等方面都在进行着不断的探索与改进。
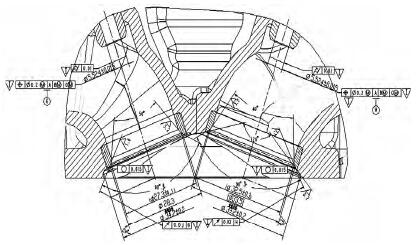
图1 气门导管和气门座圈产品图
2 、对气门座圈和气门导管孔加工工艺方案的探讨与改进
为了提高机械加工的精度与稳定性,当前对气门座圈密封面对气门导管孔的加工的机床均采用加工中心,而加工的基本工艺,目前也都是采用专用复合刀具分粗、精两次加工至最终尺寸,但实施的具体工艺还是值得探讨的,如粗、精加工如何进行,工件的定位方式,选用何种刀具等。
2.1 初始采用的工艺
初始采用的工艺及其加工方式是:粗加工只加工气门座圈 2 个截面及导管导引孔,导管导引孔留 0.04-0.08 mm 余量,精加工时以导管导引孔作为导向加工导管孔和密封面至最终尺寸,如图 2 及图3 所示。应用此种工艺主要应注意的是,在导管孔铰刀切削刃铰出导管后再加工密封面,这样可避免加工中的干涉,使加工相对平稳,有利于保证密封面相对导管孔的跳动要求。
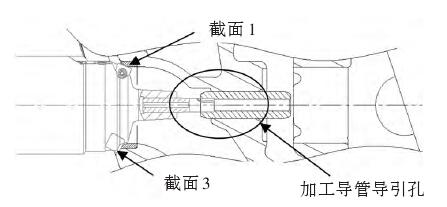
图2 导管导引孔加工示意图
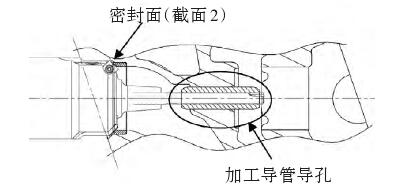
图3 导管孔加工示意图
早期加工中心的生产线采用的都是上述的工艺及其加工的方式。但长期运行下来,加工的稳定性并不太好,偶尔会有跳动超差现象,并出现靠近气道截面 3 的刀片寿命达不到要求,频繁折断等缺陷。针对此缺陷,优化了切削参数,更换刀体,降低刀具寿命。但此问题只是略有好转,而没有得到有效的解决。
通过对密封面的加工工艺进行分析,如图 4 所示,由于导引孔刀具去除 2 个截面余量后,直接加工密封面至最终尺寸,尚留有 0.24 mm 余量,而要加工粉末冶金材料的密封面时,一次加工就要去除这么大的余量,极有可能会对加工稳定性产生影响。鉴于此,通过与刀具技术人员进行探讨,并到相关厂家调研后,最终决定对原工艺进行改进。
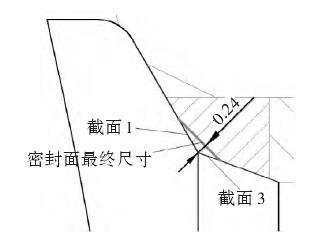
图4 初始密封面加工示意图
2.2 改进后的工艺
改进后的工艺及其加工方式是:粗加工气门座圈的3个截面和导管的导引孔,其中密封面留0.1 mm余量,导管导引孔留0.04-0.08 mm余量,精加工时铰导管孔及密封面至最终尺寸。另导管孔加工可根据材质及硬度要求,可做成阶梯尺寸,分两次加工至最终尺寸。改进后的密封面加工示意图如图5所示。
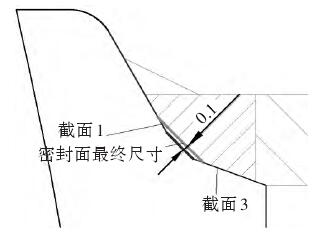
图5 改进后密封面加工示意图
采用此工艺及其加工的方式进行批量工艺验证后,密封面相对导管孔跳动加工稳定。此种方案已经在我厂多条生产线中得到了应用,其加工精度稳定,刀具寿命长,加工的成本也相应降低。通过实践验证,我们认为改进后的工艺及其加工的方式应该是目前总结出比较成熟稳定的工艺方案。
3 、对定位方式的探讨与改进
众所周知,工件的定位方式对其加工精度和加工效率影响是很大的。
3.1 初始采用的定位方式
初始采用的定位方式是:用燃烧室面(底面)及两销孔定位,因其加工气门锥面与定位面在一侧,为了避免加工时刀具与夹具发生干涉,此时的夹具采用背部掏空结构。底面销孔定位,背部掏空的夹具示意图如图 6 所示。
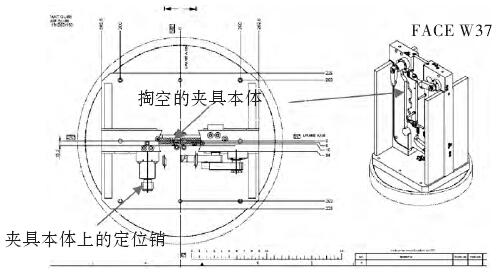
图6 背部掏空定位夹具形式
该夹具的本体较厚重,夹具夹紧采用气动方式,夹紧牢靠。虽然夹具的成本高,但是定位准确,节省夹紧时间,有利于生产节拍的保证。经过一段时间的运行,我们发现由于夹具定位销与气门座圈及导管孔压装后的缸盖变形,产生位置误差,使精加工的加工余量不均匀,导管孔铰刀容易铰偏,精加工后导管孔的位置度易出现超差现象。特别是设备长时间运行后,这种超常现象断续出现的频率也在逐步增大。为了解决此问题,我们在程序中增加修正线性补偿变量,并进行自动调整。在程序中增加修正线性补偿变量,并进行自动调整后,导管孔的位置度的超差现象得到了有效的控制。由此我们认为,如果产品在设计阶段即考虑压装变形造成位置误差偏置,并在图纸各个导管座圈位置坐标补偿变形量,将会更利于保证气门座圈和气门导管孔精加工的密封面跳动。经过一段生产运行,虽然导管孔的位置度的超差现象得到了有效的控制,但并没有达到理想的程度。针对此问题,我们在与国外机床厂家方案交流中,得知他们根据气门座圈和气门导管的压装要求,常常也应用顶面及销孔的定位方式,而且效果很好。鉴于此,我们对其定位方式又进行了改进。
3.2 改进后定位方式
如图 7 所示,改进后定位方式采用顶面及两销孔定位,用测头探测燃烧室面(底面)及两销孔作为加工基准,修正加工原点,一次装夹加工所有进排气门座圈及导管孔。
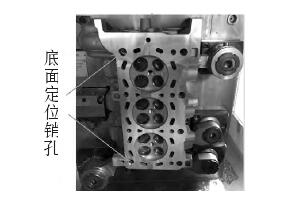
图7 顶面及两销孔定位夹具形式
经过生产线验证,此种定位方式加工夹具简单,刚性好,加工刀具刀杆悬伸减小,加工时更利于减小刀具本体的跳动,更利于保证气门导管对气门座圈的跳动要求,并且可忽略导管及座圈压装后产生变形对加工位置度的影响。通过两条生产线比较(分别采用改进前、后两种定位方式),在常温压装导管和座圈的条件下,采用探头探测的定位夹紧方式更易保证气门座圈密封面相对导管孔跳动。
4 、刀具的选用
4.1 复合刀具结构特点
气门座圈和气门导管孔加工尺寸精度要求高,材料一般为铁基粉末冶金,加工特点是硬度高,加工难度大。如图8和图9所示,一般生产线选用SECO或MAPAL复合刀具,目前选用刀具结构特点是:a.采用整体刀柄,在同一刀体上安装加工座圈密封面的刀片及加工导管孔的铰刀;b.加工导管孔铰刀采用整体硬质合金刀杆上焊接 PCD 刀片或可换 PCD 刀片,整体刚性好,跳动小于 5μ,无需预调,寿命长,质量稳定;c.密封面加工时,采用 2 个刀片同时切削,保证切削过程平稳,保证加工圆度和粗糙度。刀片采用4刃CBN贴面,所有刀片高度可调,调整方便。
4.2 铰刀的选用
4.2.1 铰刀刀片的选用
加工导管孔的铰刀一般选用整体焊接刀片式铰刀和可换刀片式铰刀[1]。采用可换刀片式铰刀最初想法是由于刀片可换,调整方便,成本低。但实际加工中,出现很多问题。由于导管材料为粉末冶金,硬度高,刀片经常出现加工寿命达不到,甚至只加工 20-30 件就出现直径小,刀片松动等现象。经过改进,换成整体焊接刀片,加工尺寸稳定,其寿命
可提高10-20倍,并且最多可修磨5次,成本低。
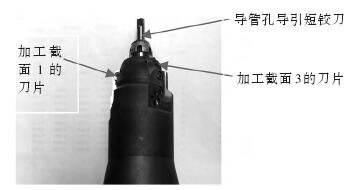
图8 复合短铰刀
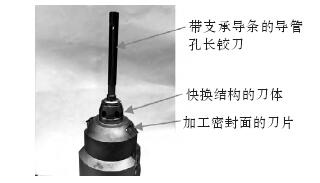
图9 复合长铰刀
4.2.2 铰刀头部刃口的选用
铰刀头部刃口一般选用单刃或多刃形式。为了提高加工效率,常常采用多刃铰刀[1]。 但实际加工中,多刃铰刀会造成密封面相对导管孔跳动经常超差。其原因是采用背部掏空夹具,压装后导管位置度变化了,而多刃铰刀的特点是更利于保证孔的尺寸精度。改进后采用单刃 PCD 带导条的铰刀,实践证明,单刃带导条支撑的铰刀更利于修正孔的位置,加工更稳定。但导管孔精铰刀加工时易出现精铰导管孔内壁有划痕现象,发现铰刀杆上加工几十件后粘有黑的粉末状屑,冷却孔里有碎屑。为了解决此问题,在加工程序上增加导管铰刀加工完成后进行 2s 的停留,断屑。但仍有切屑冷却液进入铰刀冷却孔里,堵塞冷却通道。我们在机床增加磁辊过滤,大大减少机床对切削的过滤效果,并在铰刀杆上打了两个内冷孔,利于冲屑,加工后导管孔内壁光滑,明显改善了导管孔的加工质量及加工尺寸精度。
4.3 刀柄的选用
对于气门座圈和气门导管孔这种复杂加工部位,特别是加工中心加工方式对刀具刀柄的要求也很高。气缸盖加工中心生产线 COMAU、MAG、GROB、Heller 等加工中心主轴刀柄形式是 HSK63A,采用刀柄与刀杆连接处加调整螺母来消除主轴的径向跳动,特别是 HSK 形式刀柄采用锥面、端面两面同时定位,锥体长度较短有利于实现换刀及高速化。
经过生产实践,加工中心生产线使用的刀柄不选用热胀刀具,因导管孔铰刀加工寿命几百件,在生产中需频繁更换,安装及拆卸此铰刀多次后会造成刀体本身与铰刀同轴度超差,最终造成导管孔与座圈密封面跳动超差,影响密封面加工质量,严重时甚至造成导管孔直径超差。刀体装铰刀处采用快换结构或拉钉结构,减少了多次装刀造成的刀柄本身变形,而且调节方便。
5 、结语
对多条气缸盖加工中心生产线加工气门座圈和导管孔实践中,从工艺方案验证、工件定位方式选择及刀具的选用等方面,我们总结出提高其加工精度的有效途径主要如下:a.减少密封面加工余量的加工工艺方案,可提高气门座圈和导管孔密封面圆度和跳动要求,使加工质量稳定,有效减少 20%不必要的废品。b.采用“顶面一面两销+探头探测”的定位方式,不仅避免压装变形,更利于提高 10%生产效率。c.专用合理的整体焊接单刃复合刀具,使加工精度更稳定,刀具成本降低 20%,降低换刀频次50%。
投稿箱:
如果您有机床行业、企业相关新闻稿件发表,或进行资讯合作,欢迎联系本网编辑部, 邮箱:skjcsc@vip.sina.com
如果您有机床行业、企业相关新闻稿件发表,或进行资讯合作,欢迎联系本网编辑部, 邮箱:skjcsc@vip.sina.com
更多相关信息