阶梯深孔加工技术的研究
2019-2-11 来源: 广西玉柴机器股份有限公司 作者:冯 基
摘 要:提出了基于组合机床上底孔引导的复合钻、复合铰阶梯深孔的加工技术,解决了加工阶梯深孔容易出现钻偏、铰不出、铰大、椭圆、刀具容易折断、崩刃等问题,提高了产品的加工质量,降低了生产成本。
关键词:底孔引导;阶梯深孔;复合钻;复合铰
组合机床上阶梯深孔传统的加工技术通常采用导向套定位,多工序钻、铰或单工序复合钻、铰。多工序钻、铰由于上下工序定位误差的影响,往往造成阶梯深孔不同轴、钻、铰偏等问题;单工序复合钻、铰由于刀具开始切削加工时导向距离加工面远,刀具悬伸长刚性差定位不好,因此容易出现钻偏、铰不出、铰大,刀具容易折断等问题。
为了解决阶梯深孔加工这些疑难问题,提出了以底孔引导复合钻、铰阶梯深孔全新的加工技术。
1、 底孔引导复合钻阶梯深孔的加工技术
1.1 传统多工序钻或单工序复合钻阶梯深孔加工技术存在问题
图 1 为气缸体阶梯深孔,由 准8 深 120 及 准10 深50 两同心孔组成,组合机床上传统的加工工艺有三种:
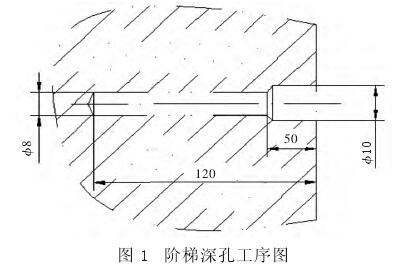
第一种工艺如图 2 所示,工序 1(或工步 1)先钻阶梯深孔的大孔 准10,即大钻头以模板上的钻套定位钻大孔到工艺要求深度 50;然后工序 2(或工步 2)钻小孔 准8,即小钻头以模板上的钻套定位钻小孔到工艺要求深度 120,如图 3 所示。
这种工艺的优点是减少小钻头的钻削深度,从而减少小钻头因为刚性差而折断的问题,目前这种工艺用得较普遍,但是其缺点也明显,因为钻小孔时钻套距离小孔远,钻套基本上起不到定位作用,小钻头便顺着大钻头钻削大孔时两切削刃留下的 118°锥面钻削,因此极容易钻偏,对于一些壁厚比较薄的深孔,经常出现钻穿壁现象。
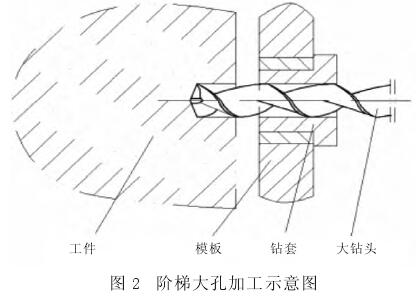
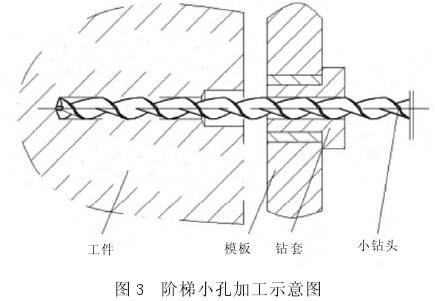
第二种工艺,如图 4 所示,工序 1(或工步 1)先钻阶梯深孔的小孔 准8,即小钻头以模板上的钻套定位钻小孔到工艺要求深度 120;工序 2(或工步 2)钻大孔 准10,即大钻头以模板上的钻套定位扩大孔到工艺要求深度 50,如图 5 所示。这种工艺的优点是开始钻削时大孔、小孔都是从工件表面开始,模板上的导向套都起到了定位作用,所以小孔、大孔的垂直、位置度都较好,减少钻偏现象发生,但其缺点是小钻头因为钻削比较深,且自身刚性差,因此比较容易折断。
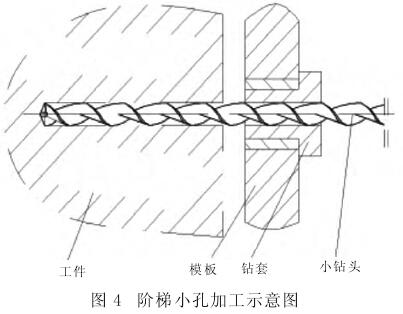
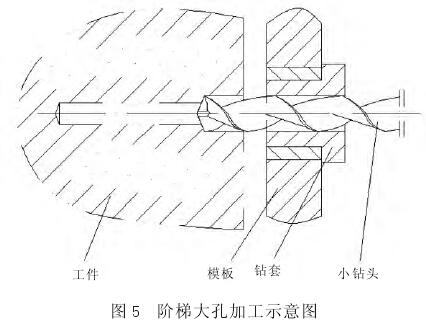
第三种工艺如图 6 所示,采用阶梯钻进行加工,即阶梯钻的后段以模板上钻套定位复合钻阶梯深孔准8 深 120、准10 深 50. 这种工艺的优点是,减少了一道加工工序,降低了生产成本,但其缺点是,在加工过程中,由于阶梯钻前段比较长,而加工时只是对以阶梯钻后段进行定位,造成切削加工时阶梯钻前段悬伸较长,摆动大,定位精度差,刚性不足,因此加工容易出现钻偏,也容易造成阶梯钻前段折断,严重影响产品的加工质量。
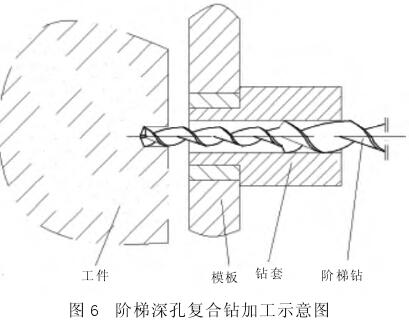
1.2 底孔引导复合钻阶梯深孔的加工技术
为了克服组合机床上传统阶梯深孔加工技术的缺陷,提出了一种底孔引导复合钻阶梯深孔全新的加工技术,即首先利用阶梯钻的前段及后段分别与前钻套及后钻套定位加工出一基础引孔,然后移开前钻套以基础引孔及后钻套定位继续钻孔至工艺要求深度。
(1)钻一基础引孔。如图 7 所示,前钻套安装在活动小模板上,通过油缸带动活动小模板沿着导轨向下运动,当活动小模板移动到位,安装在固定模板上的定位销插入活动小模板的销孔,保证前钻套与安装在固定模板上的后钻套同轴,然后主轴箱带动阶梯钻前段、后段分别进入前钻套及后钻套内定位,加工 准8 深孔的一小段深 20 作为基础引孔。
由于加工时阶梯钻前段、后段分别与前钻套及后钻套定位,且前钻套与后钻套同轴,而且前导钻套距离工件的加工面近,因此定位精高,从而保证了 准8 深孔的基础引孔加工的位置精度,同时由于刚开始加工时阶梯钻后段进入后钻套的长度为 20,因此可有效地防止阶梯钻的摆动,从而使阶梯钻的刚性得到显著加强,有效地解决阶梯钻前段因摆动大刚性差容易折断的难题。
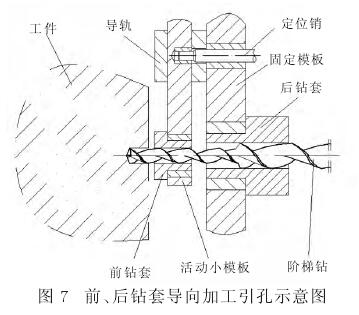
(2)复合钻阶梯深孔到工艺要求深度。如图 8 所示,由于阶梯钻后段的直径 准10 比前段的直径 准8大,因此首先阶梯钻要在主轴箱的带动下快速退回直至阶梯钻前段完全退出前钻套,然后前钻套在油缸带动活动小模板下撤回至完全让开阶梯钻后段能通过不干涉的位置,然后主轴箱带动阶梯钻快速进给到终点位置前 5 的安全位置,利用阶梯钻前段与基础引孔以及阶梯钻后段与后钻套进行定位,然后复合钻阶梯深孔 准8 深 120、准10 深 50 到工艺要求深度。
由于前面已经加工了 准8 深孔长 20 的基础引孔,因此在后续加工时,阶梯钻前段仍然有长 15 进入基础引孔定位,因此后续的加工是在基础引孔的导向基础上继续加工,保证了后续的加工精度;在后续开始加工时,阶梯钻后段有 35 进入后钻套定位,因此可有效地防止阶梯钻的摆动,从而使阶梯钻的刚性得到显著加强,有效地解决阶梯钻前段因摆动大刚性差容易折断问题。
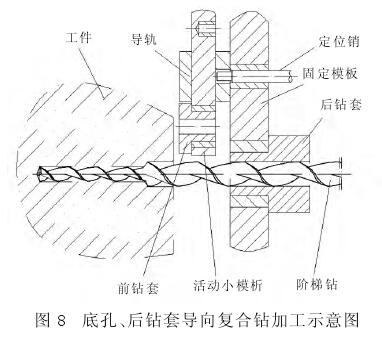
综合上述,加工基础引孔的目的是在移开前钻套后,在基础引孔及后钻套的定位下继续加工,直至加工到阶梯深孔工艺要求的 准8 深 120、准10 深 50。综上所述,底孔引导复合钻阶梯深孔的加工技术可有效解决传统技术在加工阶梯深孔时出现容易钻偏、阶梯钻前段容易折断的难题,提高了产品加工质量,降低了刀具成本,提高了生产效率。
2 、底孔引导复合铰阶梯深孔的加工技术
2.1 传统复合铰阶梯深孔的加工技术存在问题
图 9 为气缸盖排气面有 3 个 准11 × 准12 阶梯深孔(其中 准11 是深孔,通常称之为深水孔),待精铰前如图 10 所示先复合钻到 准10 × 准11.5 阶梯孔,组合机床上传统的加工工艺有两种:
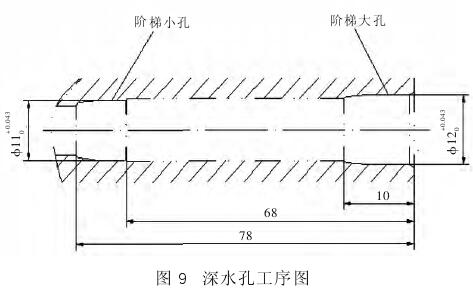
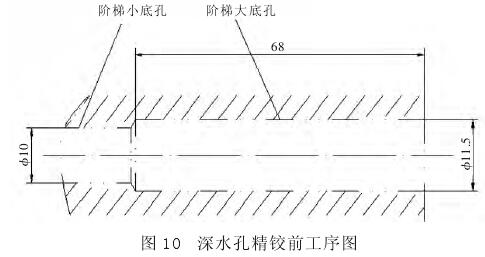
第一种工艺如图 11 所示,采用导向套定位复合铰 准11 × 准12 阶梯深孔到工艺尺寸,但由于 准9 阶梯小底孔位于待精铰阶梯深孔的底部,距离端口比较深,因此针对于精铰加工的位置度往往较差,而且精铰工序与精铰前道工序存在定位误差,并且复合刀 准11 切削部分距离导向套较远,悬伸较长,摆动大,定位精度差,刚性不足,因此该工艺经常有阶梯深孔 准11 段铰不出现象。
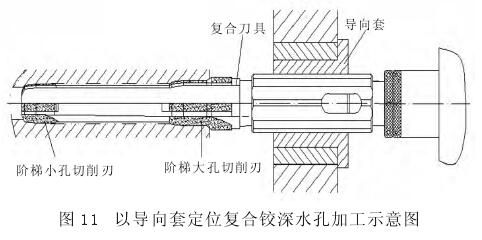
第二种工艺如图 12 所示,为了保证阶梯小孔准11 能精铰出,将导向套去除,加工时 准11 底孔切削刃和 准12 底孔切削刃同时顺着阶梯小底孔和阶梯大底孔进行切削,但是由于复合刀具悬伸长,摆动大,刚性不足,在伸入待精铰阶梯深孔切削时,准11 底孔切削刃和 准12 底孔切削刃缺少导向和支撑,从而造成精铰阶梯小孔时振刀、椭圆、孔大,且刀具切削刃容易崩等问题。
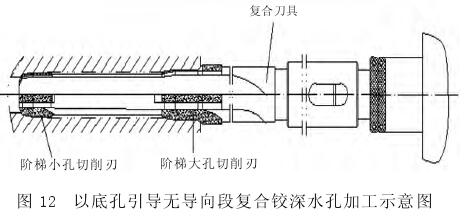
2.2 底孔引导复合铰阶梯深孔的加工技术
为了克服上述现有技术中缺陷,如图 13 所示提供了一种结构简单合理,通过在复合刀具上设置导向部来避免阶梯小孔加工时的振刀、椭圆及孔大,且刀具崩刃的阶梯深孔的复合精铰加工刀具。具体的技术方案为,在小孔切削刃的后端和大底孔切削刃前端分别设置有导向段,导向段包括 4 四条沿刀具本体圆周均布直径比阶梯大底孔的直径小 0.05 ~ 0.08 宽 2的圆柱刃带,其中小孔切削刃导向段的圆柱刃带长度为 20,大底孔切削刃的圆柱刃带长度为 8.
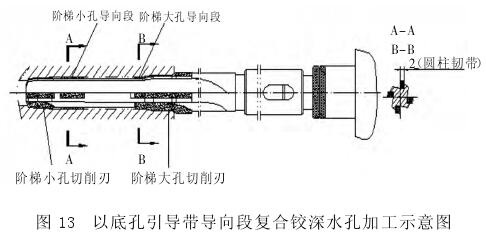
具体的工作原理为,加工过程中,小孔切削刃先进入阶梯大底孔,接着小孔切削刃后面的导向段在其前端倒角的引导下进入阶梯大底孔,由于其不开设后角且直径比阶梯大底孔的直径小 0.05 ~ 0.08,所以其在阶梯大底孔内不参加切削,只起到定位、导向及提高刀具刚性的作用接着开始精铰阶梯小孔,大底孔切削刃前端的导向段在其前端的倒角的引导下进入阶梯大底孔,由于其不开设后角且直径比阶梯大底孔的直径小 0.05 ~ 0.08,所以其在阶梯大底孔内不参加切削,只起到定位、导向、加强刀具刚性的作用,接着开始精铰阶梯大孔。
该 准11 × 准12 阶梯深孔的复合精铰加工刀具通过在复合刀上分别设置阶梯小孔导向段和阶梯大孔导向段,以精铰前的阶梯大底孔作为复合刀导向的基础,对阶梯小孔和阶梯大孔进行精铰,有效地解决了在复合精铰中出现的阶梯小孔容易振刀、椭圆、孔大、刀具切削刃容易崩等问题,提高了产品的加工质量,降低了生产成本。
3、 结束语
本文提出了组合机床上底孔引导的复合钻、复合铰的阶梯深孔的加工技术,彻底解决了阶梯深孔加工位置度、孔径等难保证的难题,提高了产品加工质量,降低了生产成本,提升了产品的市场竞争力,产生了巨大的直接、间接的经济效益和社会效益,在机加工行业有着广泛的推广价值。
投稿箱:
如果您有机床行业、企业相关新闻稿件发表,或进行资讯合作,欢迎联系本网编辑部, 邮箱:skjcsc@vip.sina.com
如果您有机床行业、企业相关新闻稿件发表,或进行资讯合作,欢迎联系本网编辑部, 邮箱:skjcsc@vip.sina.com
更多相关信息