汽车覆盖件用淬硬钢模具铣削加工的研究进展
2019-5-24 来源:哈尔滨理工大学机械动力工程学院 作者:刘献礼 姜彦翠 吴石 李茂月 岳彩旭等
摘要:作为汽车产销量第一大国,我国的汽车模具加工能力远远不能适应汽车更新换型的需要,中高档轿车关键覆盖件模具铣削加工质量还达不到设计要求。通过汽车大型覆盖件淬硬钢模具的铣削加工特征和难点的分析可知,铣削过程建模与仿真分析、加工工艺系统动力学特性和铣削稳定性分析、汽车覆盖件淬硬钢模具铣削加工用刀具研制、自由曲面数控编程技术及工艺规划是汽车模具高精度铣削加工的研究重点,总结归纳这几个方面的研究现状,同时探讨汽车覆盖件淬硬钢模具铣削加工仍有待于进一步解决的问题,为其后续研究方向提出一些建议。
关键词:汽车覆盖件模具;淬硬钢模具;数控铣削加工;动力学特性;刀具
0 前言
随着我国汽车工业的快速发展,各大汽车制造厂商为了争夺市场,适应购买者对汽车使用性能及造型个性化等方面的需求,不断进行新旧车型的更新换代,改型车和新型车的最主要的标志就是车身外形必须改换,汽车的覆盖件模具要重新设计制造。图 1 为汽车车身覆盖件拆解,一辆轿车汽车覆盖件数量高达数十件甚至百件以上,每件覆盖件均由其成配套模具冲压成形,这些配套模具的设计和制造时间严重制约汽车换改型的周期。可见,新旧车型的快速升级换代,对汽车覆盖件模具产生了巨大需求。
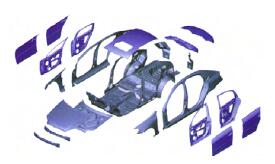
图 1 汽车覆盖件零件分解
为提高汽车大型覆盖件淬硬钢模具的生产效率,铣削加工技术在国内汽车模具制造企业中得到程度不同的应用。对比传统的磨削加工工艺,铣削加工可以获得理想表面质量,同时具有加工柔性好、无污染等特点。国内汽车覆盖件模具加工时,一般在模具切削加工工序之后还要花大量工时进行人工磨抛,其时间一般需要 3 周以上,模具最终尺寸精度和表面质量靠大量的钳工修磨研配来保证,因此,生产效率极低。而且目前中高档轿车的外覆盖件模具,国内汽车模具生产厂家还没有生产能力。因此,开展中高档汽车覆盖件模具的高效高精度铣削加工技术对提高模具制造水平和促进汽车产业的发展具有重要的支撑作用。
1 、汽车覆盖件模具特征和加工难点
汽车大型覆盖件模具是生产汽车车身的大型关键工艺装备,其主要特征如图 2 所示。
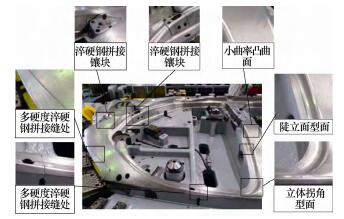
图 2 汽车覆盖件模具的加工特征
(1) 工件材料属于典型高硬度、高强度材料。模具材料多为7Cr Si Mn Mo V和Cr12Mo V
等模具钢,淬火后硬度达到 HRC45~65。
(2) 型面特征复杂。存在凹曲面、凸曲面、倾斜面、陡立面、拐角、沟槽等特征型面,且为保证凸凹模的合模精度对模具型面加工精度和表面加工质量要求高。
(3) 轮廓尺寸大。其尺寸范围 (0.5 ~ 2.5)m ×(1.5~3.5m,加工型面面积大,切削路径长,数控加工设备各运动轴行程范围大。
(4) 多硬度材料拼接结构。为满足大型冲压模具的加工精确度,提高加工效率,大型模具一般釆用多个分块模具拼接而成,或根据模具不同位置所受应力的特征,采用镶块式淬硬钢与模具本体拼接而成。在制作分块模具和淬硬钢镶块时首先单独进行粗加工和半精加工,然后再拼接成整体模具后进行精铣加工。多硬度拼接淬硬钢材料硬度相差高达ΔHRC5-ΔHRC20。
(5) 加工精度和表面加工质量要求高。为保证覆盖件的光顺性,要求凸凹模具有较高的合模精度,因此凸凹模具各自铣削加工时对加工精度和表面加工质量有很高的要求。若模具上有一处型面轮廓精度达不到要求或存在表面加工缺陷,会导致冲压件出现褶皱、凹陷等缺陷,则整套凸凹模具均不能再使用。
国内汽车模具生产企业的一般加工流程如图 3所示,模具最终表面加工质量和型面精度要靠钳工大量的打磨研合来保证,工件淬火后的加工精度直接影响后期抛光研磨的工作量。目前对于型面特征复杂而表面加工质量和型面位置精度要求不高的汽车内覆盖件模具的加工技术问题已经基本解决了,然而在加工精度要求高的汽车外覆盖件模具制造方面,仍普遍存在着生产效率较低、刀具使用寿命不足、已加工表面质量差等突出问题,导致模具整体合模精度低,覆盖件冲压成品光顺性较差。严重影响汽车模具成形精度、使用寿命和生产效率。
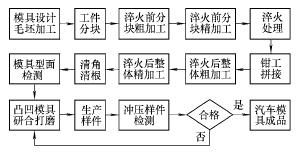
图 3 汽车模具生产企业的一般加工流程
汽车大型覆盖件模具铣削加工中的难点。
(1) 汽车模具铣削条件恶劣,出现型面误差和表面加工缺陷。淬火后高硬度材料铣削时刀具切入困难,与工件之间出现滑擦现象;型面加工特征多变及多硬度拼接特征铣削载荷变化频繁,易引起刀具变形、振动、磨损、破损;材料拼接处由硬度差导致的加工轮廓不一致。这些现象导致型面误差和表面加工缺陷。
(2) 汽车模具铣削过程易产生颤振。汽车模具铣削过程动态铣削力大,且加工工艺系统动态性能了解不清,无法有效的控制颤振,导致加工表面恶化。一些企业为了避免切削颤振发生,通常以牺牲加工效率为代价,选择保守的切削参数,导致数控加工设备性能得不到充分发挥。
(3) 刀具性能不满足铣削要求。为保证模具型面的完整性及覆盖件成形质量,精加工时要求刀具遍历整个汽车模具加工表面,中间过程不能换刀,刀具使用寿命需要达到 4~12 h;不同硬度工件材料拼接过渡处铣削载荷突变,导致刀具的磨损破损程度加剧,故汽车模具铣削加工对刀具性能提出了更高要求。
(4) 汽车模具复杂型面数控编程及刀具路径规划不合理。对有效加工带宽及加工行距的确定不合理,增加模具抛光、打磨等工序的任务量;模具型面变曲率特征、拐角特征等易产生刀具局部干涉;无法有效地根据特定的加工曲面和加工条件进行刀具路径的规划,导致刀具失效过快,且加工效率低下。
综上所述,通过汽车覆盖件模具加工中的难点分析,高效高精度铣削加工汽车覆盖件模具需要在淬硬钢模具铣削过程建模与分析、加工工艺系统动力学特性与铣削稳定性分析、汽车覆盖件淬硬钢模具铣削加工用刀具研制、模具复杂曲面数控编程技术及工艺规划研究等方面进行系统深入的研究,如图 4 所示,本文针对这几方面的研究现状进行归纳和总结。
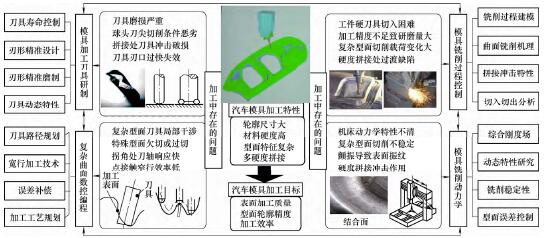
图 4 汽车覆盖件模具加工过程分析
2 、淬硬钢模具铣削过程建模与分析
国内外学者对淬硬钢铣削过程机理主要通过理论建模与仿真、基于有限元技术的建模与仿真以及试验方法分析等基本方法进行深入研究,如图 5所示。一般在研究过程中常常把两种及两种以上的基本方法相结合,完成淬硬钢铣削过程机理的分析、铣削结果的预测以及铣削条件的优化和铣削过程的控制。
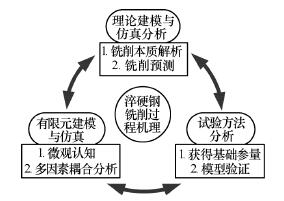
图 5 淬硬钢铣削过程建模与分析方法
2.1 淬硬钢模具铣削的理论建模
淬硬钢模具铣削理论建模与仿真分析的过程是在对淬硬钢模具铣削过程机理深入认知的基础之上,对铣削过程的物理本质解析,建立铣削过程物理量与铣削条件之间的物理关系。铣削过程理论建模一般要以试验分析为基础,理论公式中的参量通过试验来确定。
2.1.1 球头刀铣削力建模
汽车覆盖件淬硬钢模具铣削过程中产生较大铣削力,直接影响模具的切削加工性、刀具磨损、刀具变形、机床振动、加工精度及表面完整性等。目前,汽车模具的铣削加工多采用球头铣刀,而球头铣刀铣削力模型应用最普遍的是由 LEE 和ALTINTAS 建立的球头铣刀瞬时刚性力模型。其主要思想是将切削刃离散为切削刃微元,将微元铣削力表达成切削面积和切削刃接触长度的函数,如图 6 所示。
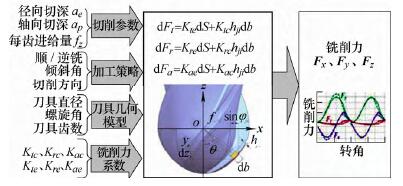
图 6 球头铣刀铣削力建模
汽车模具复杂曲面铣削加工中,刀具的铣削状态一般是不断变化的,变铣削状态主要包括刀具进给方向的变化和刀具-工件切触区域的变化。而刀具铣削状态变化在铣削力模型中主要通过未变形切屑厚度体现出来,进给方向变化通过对未变形切屑厚度计算模型的影响体现出来,刀具与工件切触区域的变化用以界定未变形切屑厚度计算模型的有效范围。球头刀铣削曲面的铣削力建模需要解决的关键问题有:球头刀刃线几何模型、刀具-工件接触区域确定、瞬时未变形切屑厚度计算、铣削力系数识别、铣削力在各坐标系间的转换、被加工表面类型。SUBRAHMANYAM 等建立球头铣刀铣削加工倾斜面工件时铣削力模型。KIM 等提出了一种基于Z-Map 模型的确定刀具-工件切触区域的方法,并由此建立铣削力模型。魏兆成等建立铣削力模型时考虑球头铣刀三维曲面加工进给方向任意变化。曹清园等研究了考虑工件型面曲率半径和刀具变形的球头铣刀铣削自由曲面铣削力建模。HAO等提出一种铣削复杂曲面的铣削力预测方法,考虑了刀具跳动的影响。GENG 等在建立球头铣刀铣削力模型时采用离散方法求得刀具-工件接触区域。JU等针对刀具工件接触区域的求解提出一种新方法。
2.1.2 球头刀铣削表面形貌建模
为保证汽车冲压钣金件的光顺性,要求汽车覆盖件模具具有较高的表面加工质量,而在以往的研究中学者们一向重视对于表面粗糙度和表面形貌的研究。从理论研究的角度,球头刀铣削表面形貌建模方法主要分为两类。一类是几何实体建模法,建立刀具和工件的 CAD 几何实体并离散,通过布尔操作运算获得工件表面形貌模型。IMANI 等使用B-Rep 建立工件实体建模和刀具运动学扫掠体模型,通过刀具扫掠体与工件求交建立球头刀三轴铣削的工件表面形貌模型。
YIP-HOI等基于实体模型研究了刀具工件接触特征,进而进行表面形貌的仿真。另一类是 Z-Map 法,将工件模型在 XOY 坐标内离散成大量分布均匀的 xy 网格节点,并求得每个网格节点对应 z 坐标的法向残余高度值,这些网格节点就组成工件的数字化模型,用以表述已加工表面。ANTONIADIS 等研究了球头铣刀加工复杂曲面时工件表面形貌的形成规律。BOUZAKIS 等基于工件网格划分采用一组平行参考面与刀刃求交,建立了四轴球头铣削表面形貌模型。OMAR等用 Z-Map 法构造了工件表面轮廓模型,该模型考虑了刀具跳动、刀具偏转、动力学特性和后刀面磨损等因素。文献考虑刀轴倾角建立了球头铣刀铣削模具钢的表面形貌仿真模型,分析认为刀轴倾角 15°时表面残留高度最小。ZHANG 等针对复杂曲面多轴铣削加工提出一种表面形貌模型仿真方法,分析了刀具磨损和刀具姿态对表面形貌的影响。还有 FANG 等提出一种基于离散点云的三维表面形貌仿真模型,由球头铣刀几何模型和运动方程,形成切削刃点云并进行数值计算处理,生成三维表面形貌用离散点云数据,如图 7 所示。
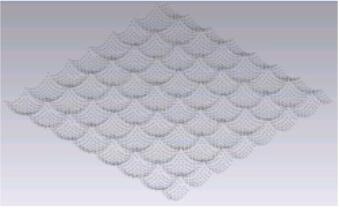
图 7 基于点云的表面形貌模拟
2.2 淬硬钢模具铣削过程的有限元模拟
淬硬钢模具铣削机理的有限元模拟研究中主要关注分析预测铣削力、铣削温度场、切屑形成与流出、刀具磨损、加工变形、表面残余应力和加工过程中微观结构变化等方面,图 8 为汽车模具有限元数值模拟实施方案。OZEL 等运用有限元法研究了未涂层硬质合金刀具高速铣削模具钢过程中的切削力、刀具应力和温度场分布。文献利用有限元仿真得知高速铣削淬硬模具钢时切削速度为300 m/min 形成锯齿切屑。文献基于优化理论对ABAQUS 进行二次开发,建立正交切削的参数化模型,避免传统有限元模拟切削过程中切削参数变化则边界条件就要重新设置而不易获得最佳切削参数的问题。
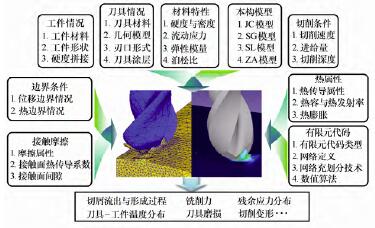
图 8 汽车模具铣削仿真过程
绝大多数的淬硬钢铣削过程有限元数值模拟仿真都是平面或斜面铣削加工,对于凸凹曲面及拐角等特征型面的研究较少,其主要难度体现在凸凹曲面及拐角等型面特征的铣削过程刀具运动轨迹非直线,刀刃与工件的接触区域不断变化,运动轨迹加载难度较大;凸凹曲面及拐角等型面特征的铣削过程的模拟仿真过程计算量大,不易收敛。图 9、图 10 分别为凸曲面铣削过程有限元数值模拟和为拐角铣削过程有限元数值模拟。
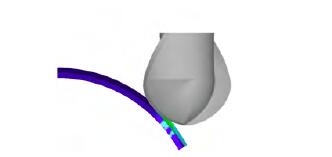
图 9 凸曲面铣削有限元仿真
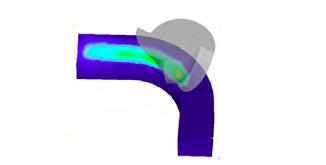
图 10 拐角铣削有限元仿真
对于汽车模具硬度拼接处铣削过程进行有限元数值模拟仿真,已有部分学者进行研究,文东辉等利用有限元软件模拟了多硬度拼接淬硬钢球头铣削加工过程,多硬度拼接淬硬钢工件模型如图11a 所示,分析了铣削力和铣削温度的分布,其分析结果如图 11b、11c 所示。
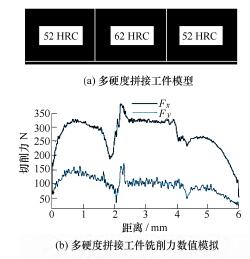
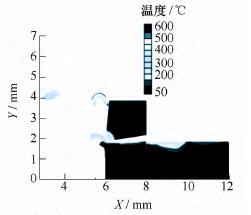
图 11 多硬度拼接淬硬钢铣削力和铣削温度
2.3 淬硬钢模具铣削机理的试验分析
淬硬钢模具铣削机理的试验分析的过程主要是通过试验数据的统计分析或结合神经网络、遗传算法及模糊理论方法等人工智能算法获得刀具参数、切削参数、铣削条件等对铣削过程物理量的影响,进而建立优化工艺参数的模型。张义平等针对淬硬钢 Cr12Mo V 进行了高速铣削研究,结果分析了铣削方式、刀具螺旋角以及润滑方式对刀具磨损、表面粗糙度、铣削力的影响。庞俊忠等通过高速铣削试验,研究了 Ti Al N 涂层整体立铣刀铣削淬硬钢时在不同切削速度的切屑形态和铣削力变化规律进行复杂曲面模具钢铣削试验,结果表明 PCBN 镶片刀具在不同冷却条件下均表现出良好的热稳定性。基于切削区域球头铣刀刀尖磨损测量值建立了球头铣刀刀具磨损模型。
针对汽车覆盖件模具凸曲面精加工切入困难的问题,通过铣削试验方法确定最小切削厚度,在此基础上建立考虑刀具变形的汽车模具凸曲面精加工极限切削深度预测模型。王扬渝等通过对 Cr12Mo V 淬硬钢单硬度和多硬度拼接进行平面铣削试验,得出振动信号的频谱由基波及其谐波组成,在硬度拼接缝处,振动信号峰值出现阶跃。LIN 等针对模具不同曲率凹曲面进行铣削试验,通过神经网建立表面粗糙度的预测模型并通过模拟退火的优化算法选择最优铣削用量。文献在四因素正交试验的基础上分析了铣削参数对铣削力和表面粗糙度的影响规律,并建立铣削力和表面粗糙度的经验模型。文献模具钢倾斜表面铣削加工试验分析了不同刀具切削路径的表面粗糙度。陈晓晓通过试验方法分析了多轴高速铣削切削参数、刀具姿态对于工件表面几何特征、表面残余应力、表面硬度及表面层显微组织的影响规律。
以上研究大多数是针对淬硬钢模具铣削过程机理的研究,而针对汽车覆盖件模具的铣削加工特殊性和加工中的问题,如汽车模具精加工刀具失效形式多为崩刃,不同硬度拼接过渡区存在凸起缺陷,凹形拐角处刀具磨损情况严重,陡立面、凹形拐角和模具刃口等难加工处的加工缺陷等问题,仍有待于进一步解决。因此,还需要通过理论建模分析、有限元数值模拟和试验方法,进一步研究汽车模具复杂型面硬态铣削过程切削层参数变化机制、铣削力、铣削温度、切入切出情况、刀具磨损破损、轮廓精度及表面完整性等基础问题,揭示汽车模具复杂型面硬态铣削过程的特殊规律和现象;深入研究多硬度拼接过缝处的铣削加工特性,即铣削力阶跃值、铣削温度、轮廓精度及表面加工质量等随工件材料硬度差、刀具材料和刀具几何参数、切削参数及加工策略的变化规律。
3 、工艺系统动力学特性和铣削稳定性
汽车覆盖件淬硬钢模具铣削加工过程中动态铣削力大,易出现颤振,在陡立面、拐角等特殊型面铣削时颤振最为严重,这是导致模具表面品质恶化的主要原因之一,颤振既与机床-刀具加工工艺系统刚度特性有关,还与铣削加工过程的动态特性有着密切联系,其发生机理、变化规律、控制方法一直是学者们关注和研究重要课题。有效控制铣削颤振需明确机床-刀-刀具系统动力学特性,合理设定加工工艺参数。
3.1 加工工艺系统刚度场研究
汽车覆盖件模具轮廓尺寸大,其数控加工设备各运动轴行程范围较大,当机床处于不同加工位置工况时机床的结构特征发生变化,从而将引起加工工艺系统动态参数的变化,导致工艺系统的切削稳定性改变。近年来对于机床加工空间内的刚度场研究逐渐引起学者们的重视,按照理论方法大致可以分为两大体系。一种分析方法是基于模态综合分析法,将机床加工空间离散为几个加工位置工况,如图 12 所示,分别分析不同加工位置工况下的机床动动态特性,形成与加工位置相关的动刚度场。刘海涛等提出机床广义加工空间和广义刚度场的概念,如式(1)所示,并建立机床的有限元模型,分析了机床在加工空间内的动刚度随位置工况及激励频率的变化趋势。
LAW 等利用模态综合法建立机床结构降阶有限元模型,缩减模型自由度,分析主轴箱不同加工位置的刀尖点动态特性变化。孙永平等建立了立式镗铣机床静刚度预测实体模型,研究了机床刚度随工作空间变化规律。王磊等采用集中参数法建立轴间耦合下三轴联动机床系统的动力学模型,对系统固有频率和频响函数相对于位置参数的变化进行分析。LUO 等使用质量变化方法预测由不同位置机床结构变化而产生的固有频率变化的基本数学模型。
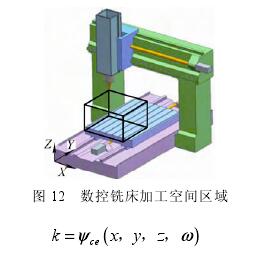
式中,x,y,z 是刀具点的空间相对位置,即各轴的相对位移量;ω 是激振力的激振频率;c 是激振力的方向;e 是拾振的方向。
另一种分析方法是基于多体动力学理论建立加工系统刚度场。该方法由闫蓉、彭芳瑜等提出,针对七轴五复合机床和五轴联动机床建立了综合闭链刚度场模型,通过引入三维力椭球进行了系统综合刚度性能的分析,如图 13 所示。基于该方法建立汽车模具加工系统综合刚度场建模,既考虑模具加工系统在加工过程中的综合刚度性能,同时考虑不同型面特征汽车模具的刚度性能,建立多轴联动机床-刀具-复杂曲面模具系统综合刚度场模型,以此优化刀具位姿和刀具切削路径。
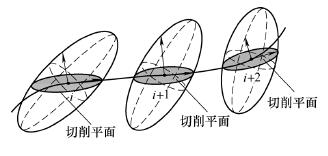
图 13 考虑切削平面的力椭球
3.2 铣削过程稳定性预测与分析
很多学者认为自激振动主要是由切屑厚度的再生效应引起的,同时与机床-刀具-工件系统的动力学特性相关。现有铣削系统颤振稳定性预测方法可分为两大类:频域解析法与时域数值法。频域解析法由 ALTINTAS 等提出,将动力学时滞微分方程组转入频域表达,采用零阶傅立叶级数展开近似求得时变方向力系数平均值,在扫描颤振频率范围时,由解析计算式直接确定临界轴向切削深度及其对应的主轴转速。之后 ALTINTAS 等利用该方法进行球头铣刀的铣削稳定性分析。随着频域传递函数法的发展,众多学者在切削稳定性研究中展开了诸多拓展,主要集中在结合具体加工条件和加工工艺系统的动力学特性的影响,且由传统的二维稳定性预测向三维稳定性预测发展。SCHMITZ 等建立颤振稳定域的解析模型,考虑刀具悬伸量对于铣削稳定域的影响,并得到三维稳定域极限图形。ERTÜRK 等考虑主轴系统的设计和操作参数建立铣削稳定性解析模型,并在无颤振稳定铣削基础上以材料去除率最大为目标选择最佳系统参数。GAGNOL 等建立一个高速主轴-轴承系统动力学模型,并阐述了由于高转速引起的弹性变形、旋转软化效果和陀螺效应对颤振稳定域的影响。HUNG等考虑主轴系统和机床立柱结构的相互作用下评价立式铣削加工系统的铣削稳定性。刘强等 对圆角铣削过程进行了稳定性建模与仿真,获得直线铣削铣削稳定域解析模型应用于圆角铣削的条件。
时域数值法,是指在时间域内对铣削稳定性进行分析的方法,主要分为半离散法和全离散法等方法。INSPERGER 等提出了半离散法,通过对每离散时间段考虑方向力系数的时变性,将铣削动力学时滞方程转化成一系列常微分方程,用于预测铣削稳定性。FAASSEN 等改进了刀刃的轨迹模型,将传统的刀刃圆形轨迹模型改进为铣削刃的次摆线轨迹模型,应用半离散法研究了变时滞特性对圆周铣削稳定性的影响,改进后的铣削刃轨迹模型可以更准确的描述切屑厚度的变化。龙新华等建立了基于次摆线轨迹的圆周铣削力模型,并利用半离散法分析了变时滞铣削过程稳定性。宋清华等利用半离散法分析了考虑每齿进给量、主轴-刀柄-刀具偏心及刀具-工件静态变形等因素对铣削稳定性极限的影响。丁烨等提出了全离散法,通过将时间全离散的单自由度及两自由度时域模型来预测切削力和振动,并利用 Floquet 理论来判断切削稳定性,其计算效率更高。基于全离散法预测分析了考虑轴向铣削力和陀螺效应的铣削稳定域,如图14 所示,结果表明,考虑轴向铣削力和陀螺效应时铣削稳定域向低频方向移动,其中陀螺效应仅在高转速部分对铣削稳定域有影响。在此基础上还分析了铣刀磨损量对不同硬度淬硬钢铣削稳定性的影响,刀具后刀面轻微磨损时稳定临界切深上升,随着工件表面硬度的提高,稳定临界切深逐步下降。
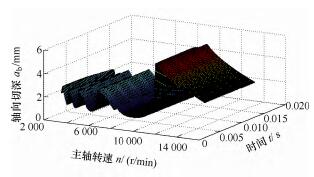
图 14 考虑轴向铣削力和陀螺效应的颤振稳定域
在研究汽车覆盖件模具不同型面特征对颤振稳定域的影响方面,主要从动力学建模考虑。建立动力学模型时应从影响铣削颤振的主要因素入手:
①刀具-工件接触区域;② 动态切削厚度;③ 切入、切出角的确定。图 15 表示凸曲面的各个铣削位置下不同刀具-工件接触区域。拼接过缝处由于不同工件材料存在硬度差导致铣时铣削力和振动发生阶跃变化,具有非线性特征,其动力学特性研究主要是铣削力的不确定性特征、铣削振动的非线性特征、表面形貌的非线性特征以及三者之间的映射关系。
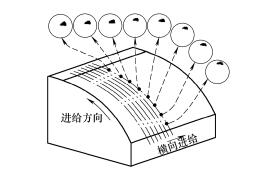
图 15 凸曲面不同铣削位置的刀具-工件接触区域
从目前的研究状况来看,对数控铣削加工过程的动力学分析多是集中在机床-刀具-工件系统的机床子系统、主轴-刀柄-刀具子系统、刀具-工件子系统等,利用不同的切削稳定性分析方法来预测和分析各个因素对铣削过程稳定性的影响规律。因此,汽车覆盖件模具稳定铣削加工的研究还需要进行机床-刀具-汽车模具完整加工工艺系统的动力学特性定量描述研究;分析模具复杂型面加工过程中的可控因素和过程物理量对于加工工艺系统动力学特性影响规律,进行复杂型面铣削加工过程多因素耦合影响下的铣削稳定性预测与模具型面误差分析,并提出复杂模具型面误差综合控制方法;揭示多硬度拼接模具铣削过程的非线性动力学特征,不同硬度拼接过缝处与型面误差之间的映射关系。
4 、汽车覆盖件模具铣削刀具研制
汽车覆盖件模具铣削加工过程中刀具磨损破损严重,因此刀具应具备高硬度、良好的耐磨耐热性、抗冲击和化学稳定性等性能。汽车模具铣削用刀具主要采用硬质合金、PCBN、陶瓷等材料,一般企业首选铣刀材料应是硬质合金,其特点是硬度高、导热性好且成本较低。为了提高刀具的耐磨性、耐高温性和化学稳定性,涂层硬质合金的使用越来越普遍。涂层的材料,从 Ti N、Al2O3、Ti C 发展为Ti CN、Ti Al N、Ti Si N、Cr Si N 等。陶瓷刀具耐磨耐热性好、化学稳定性优良,其抗黏结性比硬质合金好,主要失效形式是冲击破损和切削刃磨平。
PCBN的主要特点是硬度高、耐磨性和耐热性好,切削难加工材料时耐磨性约是陶瓷刀具的 25 倍,硬质合金的 50 倍。在汽车覆盖件淬硬钢模具铣削加工中,PCBN 的性能相对较好。选定刀具材料后,设计和优选出合理的刀具结构是实现高效高精度铣削的重要途径。将有限元铣削过程仿真分析方法结合刀具铣削加工模拟试验,对比分析刀具物理场分布,来设计和优选刀具结构、刀具刃口刃形及刀具几何参数,提高刀具切削的性能,汽车模具刀具研制具体实施方案如图 16 所示。
4.1 刀具结构设计
汽车模具制造厂家的常用刀具如表 1 所示,主要有球头铣刀和环形铣刀。球头铣刀由于具有数控编程和避免局部干涉简单的特点,在复杂曲面铣削中应用最多。对于球头铣刀的研究主要是针对切削刃和刀具角度的设计与优化。CHEN 等提出一种可提高进给率的新型球头铣刀,将 CBN 刀具的球头顶端切成 V 形,相对传统的球头铣刀可提高进给率 50%。MASAHIKO 等针对淬硬钢精加工开发了一种 CBN 球头铣刀,优化了前角和切削刃形。董敏等在回转刀具等螺距切削刃曲线的通用模型基础上,考虑了刃线的连续性的同时,提出了圆柱球头铣刀的连续切削刃曲线设计模型。针对淬硬钢精加工设计了具有新型切削刃的球头铣刀。
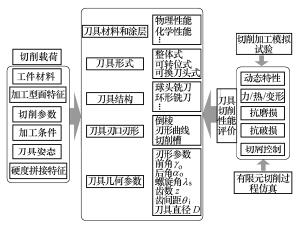
图 16 汽车模具刀具研制实施方案
表 1 适用于不同加工型面的汽车模具铣刀
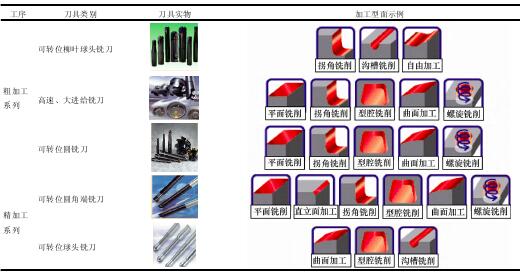
但球头铣刀切削刃上不同位置切削速度不等,刀尖点切削速度为零,切削状态恶劣,加剧刀具的磨损,影响表面加工质量,且行间距较小,加工效率较低。近年来学者们逐渐发现非球头铣刀在加工质量和加工效率上的优势,开始注重对非球头铣刀的设计研究,主要是环形铣刀的设计和研制。BEDI等通过切削试验比较了分别由环形铣刀、球头铣刀以及平底铣刀切削加工后的工件表面质量,环形铣刀铣削工件后表面质量良好,并且兼具球头铣刀和平底铣刀的优点。 针对汽车模具型面铣削加工设计一种改进环形铣刀,可实现大切深高效铣削,有效降低被加工工件表面残留高度,相对常规环形铣刀可降低表面残留高度 1.96 倍。文献设计出一种大进给环形铣刀,切削刃设计为双圆弧,建立了双圆弧切削刃的几何特征数学模型,通过有限元仿真和试验分析了其切削性能,并制定了刀具磨制工艺。
环形铣刀在铣削小曲率大曲面平坦型面时能发挥其优势,在铣削大曲率小曲面和陡立面等型面时易出现欠切和过切,因此环形铣刀铣削复杂曲面适用情况有限。非圆弧刃球型刀(双曲线回转刃形、椭圆回转刃形、抛物线回转刃形等)适用于仿形加工,如图 17 所示,可用于不同曲率的复杂曲面加工。非圆弧刃球型刀与相同直径的球头铣刀相比,参与切削的切削刃长度更长,切削过程中变形振动减小,可以实现平稳切削,提高了刀具寿命,加工成本降低。与环形铣刀相比,非圆弧刃球型刀的切削刃曲率光滑渐变,可以实现平稳切削。对于非圆弧刃球型刀的研制需要在刃形结构设计,优化刃形参数,建立几何结构模型,准确磨制切削刃,评价切削性能,制定工艺规范,数控加工刀具路径规划技术等方面进一步进行研究。
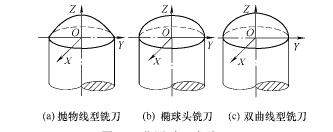
图 17 非圆弧刃球型刀
4.2 铣削 刀具磨制
复杂刀具的制造主要涉及切削刃、螺旋槽、后刀面等制造特征(图 18)的加工模型建立和砂轮类型选择、磨削约束等制备工艺方法。
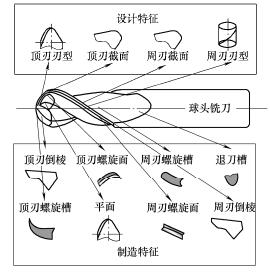
图 18 刀具的设计与制造特征
CHEN 等建立了球头端部回转刀具的等导程切削刃曲线模型,提出了等导程球头类回转刀具的设计与制造模型,定义了二轴联动加工中砂轮的进给速度。CHEN 等建立了锥球头铣刀的等螺旋角切削刃曲线模型,在此基础上提出了通过使用 CBN球面砂轮加工这种刀具前刀面的 CNC 磨削方法。此后他又建立了球头铣刀的正交螺旋形切削刃的基础上,提出了刀具前、后刀面的新磨削方法。PHAM 等建立了球头铣刀的等螺旋角模型,在此基础上详细地提出了五轴数控加工球头铣刀的相关模型,为球头铣刀的设计与制造的仿真软件的开发提供了切实有效的方法。曲坤等提出了适用于二轴联动加工的凹圆弧球头螺旋铣刀新型刃口曲线方程,并推导出了制备中的轴向与径向进给速度模型。韩成顺等提出了基于非数控加工方案的回转刀具等螺旋角切削刃曲线通用模型,讨论了非数控加工刀具时砂轮相对于铣刀的轴向和径向相对运动,并给出了球头圆弧铣刀和带角圆圆锥铣刀的刃口曲线及相对运动方程的求解实例。CHEN 等提出了带角圆的中凹铣刀等螺旋角切削刃曲线模型,并基于刃线模型建立了圆弧端铣刀的二轴联动磨削制造模型。REN 等提出了等导程铣刀的切削刃及螺旋槽设计模型,推导了二轴联动加工中的砂轮截面轮廓和砂轮进给速度,并以锥环形铣刀为例验证了数学模型的有效性。文献在对螺旋角的不同定义下,建立锥环形铣刀刀具回转面上的等螺旋角切削刃曲线模型,同时讨论了这种刀具的加工问题。
目前还未有汽车覆盖件淬硬钢模具铣削加工用的专用刀具,一般制造企业在汽车模具精加工多采用可转位球头铣刀,这种刀具除了是点接触窄行加工效率低,还易出现崩刃破损,导致刀具使用寿命小、加工效率低。因此,面向多硬度拼接汽车大型覆盖件淬硬钢模具开发高效高精度加工新型专用刀具,是提高汽车模具加工效率和表面质量的一种新途径。合理选择刀具材料并结合优质涂层材料和涂层技术,选用整体式磨制刀具结构和镶片式刀具结构,优选刀具刃线形式,精准设计刀具刃口刃形和前刀面槽型等几何参数,开发用于精加工的环形刀具和非圆弧刃球型刀具,并开发相关磨制工序及工艺优化技术。
5 、 模具曲面数控编程技术及工艺规划
汽车覆盖件模具型面和型腔精加工在保证加工质量的前提下,提高加工效率。为保证复杂曲面和型腔的铣削过程稳定、高效,通常通过提高刀具路径的光顺性和保证铣削载荷恒定来实现。
5.1 模具复杂曲面自由曲面刀具路径规划
汽车车身曲线曲面造型是由自由曲线和自由曲面来描述,因此,汽车覆盖件及其内饰件用模具多数为轮廓尺寸大、型面特征复杂的空间自由曲面。自由曲面的数控加工过程中刀具轨迹规划是关键任务,直接影响零件表面加工精度和加工效率。目前针对汽车覆盖件模具的加工设备大多为 3 轴数控加工中心或者 3+2 轴数控加工中心,粗加工和半精加工使用的刀具多为环形铣刀和球头铣刀,精加工使用的刀具多为球头铣刀。在三轴球头铣刀铣削复杂曲面的研究中,应用等残留高度法进行复杂曲面 3 轴球头铣刀加工的刀具路径规划,得出走刀步长和行距的解析式,使得 CL 数据显著减少。GLAESER 等针对复杂曲面的 3 轴铣削加工进行了研究,提出加工表面
在此基础上结合了干涉检测和优选刀具,提出了一种系统化的刀具轨迹生成方法。针对模具型腔尖角提出了双圆弧轨迹过渡,尽可能增大走刀行距。
汽车大型覆盖件模具型面中存在着大量的大面积平坦面,如发动机盖模具、天窗模具等,球头铣刀加工这些型面时切削效率低且切削速度不恒定,而将环形铣刀宽行加工技术应用于汽车模具加工中,可提高切削效率和表面加工质量。图 19 为环形铣刀宽行加工自由曲面示意图。汽车模具制造企业中已意识到环形铣刀宽行加工的诸多优势,但实际铣削过程应用存在着切削余量掌握不好,已出现过切和欠切,这些问题需要由宽行数控加工切触理论和刀具轨迹规划的研究来解决。目前宽行加工技术的研究主要集中在五轴数控加工,RAO 等提出了主曲率法,通过调整刀轴倾斜角获得最大切削宽带。通过分析刀具包络面与被加工曲面的匹配关系,实现复杂曲面的宽行加工,但该方法并不能准确计算三轴数控加工中加工带宽。文献采用二阶泰勒逼近方法分析了被加工曲面与刀具直接局部匹配情况,并以加工带宽最大化为目标实现局部刀位优化,但该方法在三轴加工中较难实现。朱利民建立了被加工曲面与刀具包络面在刀触点领域内的三阶切触关系,由单个刀位重建刀具包络面,建立了局部三阶近似曲面的数学模型。吴宝海等基于广域空间误差分析提出一种刀轴方位优化方法,从宏观的角度分析切削刃曲面到干涉区域离散点集的干涉误差,构建了刀具的有效切削轮廓,完成了有效加工带宽的计算。樊文刚等提出旋转切触刀位算法,通过刀具的后跟角和侧偏角来确定最优刀位,并对汽车顶盖模具凸曲面多点切触加工时不同走刀方向下的刀位误差分布进行了分析。目前宽行加工技术的研究多是 5 轴数控加工,而对于 3 轴数控机床或者 3+2 轴数控机床,相关研究较少。针对环形刀铣削汽车模具中的小曲率面进行三轴数控加工刀具几何切触关系分析,对比了环形铣刀与球头铣刀在曲面刀触点处的切削速,并提出由刀具切入工件部分在刀触点切平面内的投影,建立 3 轴铣削条件下有效切削带宽与曲
面曲率、刀具、进给方向、切削深度等因素之间的数学模型。
5.2 基于切削载荷的加工工艺规划
这方面的研究主要集中在对自由曲面的球头铣刀三维铣削刀具路径的优化,基本方法是通过控制主轴转速和进给速率来保持切削速度和切削载荷维持在稳定的范畴之内。基于这一原则进行数控加工编程可以减少铣削加工时间,同时延长刀具的使用寿命。在粗加工和半精加工过程中该方法可以避免过大的刀具偏移量导致的加工曲面轮廓偏离理论设计曲面。
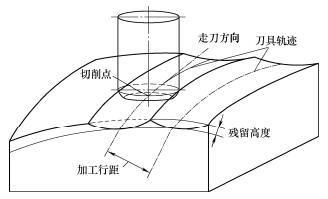
图 19 环形铣刀加工自由曲面示意图
恒定切削载荷为目标的加工工艺规划研究主要从两个方面展开。
(1) 基于体积模型的优化研究,假设铣削力与材料的平均瞬时材料去除率成比例关系。多数研究者通过改进材料去除率的算法实现进给量的优化研究。目前多数的商用 CAM 软件的加工参数优化模块多采用这种方法。
(2) 基于铣削力预测模型的进给优化研究,该方法具有更高的精度和可靠性,通过将加工过程中的铣削力限定在某一固定值/某一范围内,将固定的进给量值重新优化为一系列进给量,以满足高效加工的要求。文献提出了基于 Z-Buffer 模型预测 3轴数控加工复杂曲面的铣削力并作为约束条件,优化了进给速度。文献根据考虑刀具偏心和刀具变形的铣削力预测进行了进给速率的离线规划。把球头铣刀作为研究对象,提出了获取铣削加工中瞬时铣削力的预测方法,按照优化目标进行了进给速度优化并自动修改 NC 代码反映优化结果。建立了球头刀铣削力模型,并以切削力恒定为优化目标,进行了进给速度优化。
对汽车模具特殊型面和多硬度拼接等特征的铣削精加工刀具路径生成算法深入研究,开发的环形刀、非圆弧刃球型刀具等新型刀具铣削不同特性曲面的路径规划算法;进一步研究局部干涉检验与刀具轨迹修正的算法;在综合考虑机床动力学特性、铣削特征、刀具切削性能及物理因素的基础上制定综合加工工艺。
6 、结论
由于汽车覆盖件模具工件材料和结构的特殊性,还需要对以下几个方面进一步研究。
(1) 通过理论建模分析、数值模拟和试验研究,进一步研究自由曲面硬态铣削过程切削层参数变化机制、铣削力、铣削温度、切入切出情况、轮廓精度、表面完整性及刀具使用寿命等基础问题,揭示自由曲面硬态铣削过程的特殊规律和现象;深入研究多硬度拼接过缝处的加工特性,即铣削力阶跃值、铣削温度、刀具磨损破损等随工件材料硬度差、刀具材料和几何参数、切削参数及加工策略的变化规律。
(2) 进行机床-刀具-汽车模具加工工艺系统的动力学特性定量描述研究;分析加工过程中的可控因素和过程物理量对于加工工艺系统动力学特性影响规律,进行加工工艺系统的铣削稳定性预测与分析;揭示汽车模具的不同硬度、硬度拼接过缝处与型面误差之间的映射关系。
(3) 面向多硬度拼接汽车大型覆盖件淬硬钢模具开发高效高精度加工新型专用刀具,是提高汽车模具加工效率和表面质量的一种新途径。合理选择刀具材料并结合涂层技术,优选刃线形式,精准设计刀具刃口刃形和前刀面槽型等参数,并开发相关磨制工序及工艺优化技术。
(4) 对汽车模具特殊型面和多硬度拼接等特征的铣削精加工刀具路径生成算法深入研究,开发的环形刀、非圆弧刃球型刀具等新型刀具的路径规划算法;在综合考虑机床动力学特性、削特征、刀具切削性能及物理因素的基础上制定综合加工工艺。
投稿箱:
如果您有机床行业、企业相关新闻稿件发表,或进行资讯合作,欢迎联系本网编辑部, 邮箱:skjcsc@vip.sina.com
如果您有机床行业、企业相关新闻稿件发表,或进行资讯合作,欢迎联系本网编辑部, 邮箱:skjcsc@vip.sina.com