基于 Deform-3D 的共轨喷油器体深孔钻削温度场仿真
2018-5-2 来源:转载 作者:商解波, 武美萍,杭勇,王连顺
摘要: 因为枪钻加工中无法实时监测加工刀具的状态和加工工件的质量,所以用三维软件UG构建枪钻的立体模型,采用 Deform-3D 有限元分析软件对高压共轨喷油器体深孔钻削过程进行仿真计算,获取切削温度场的分布数据。通过钻削加工仿真实验,研究了不同钻削参数对切削温度的影响规律。仿真结果表明,随着钻入深度的增加,枪钻钻头的温度也迅速增大,并且最后逐渐稳定; 进给量、切削速度都与切削温度成正比。
关键词: 喷油器体; Deform-3D; 枪钻加工; 切削温度
机械系统中零部件的加工制造是高压共轨系统中最重要的部分,而高压共轨喷油器是机械系统中的关键零部件,由于其器体结构与工作环境较为复杂,需要在高温高压高频率下进行工作,所以采用成熟的加工工艺来确保喷油器工作质量的稳定可靠是有必要的。共轨喷油器的进油孔达不到加工要求的标准,将会因为进油孔偏移量较多、加工质量低等因素使得共轨喷油器进油慢、进出油不畅,这将严重降低高压共轨系统的使用寿命和工作稳定性。而器体进油孔的加工是整个高压共轨喷油器体加工过程中的难点和重点。由于喷油器体进油孔加工是处于加工环境封闭或半封闭的情况下的深孔加工,无法用眼睛观察加工过程中进油孔的表面加工质量和枪钻钻头的状态,并且目前尚未有合理的途径能实时监控深孔加工区域的加工状态和温度分布.
金属的钻削过程中伴随着切削热与切削温度的产生,钻削时做的功转变为热,极少的一部分通过周围介质逸出,绝大部分切削热会传入到切屑、刀具和工件中。切削热引起加工区域温度升高,使工件受热变形并且会加剧刀具磨损。尤其在工件加工质量要求较高时,切削热对工件表面质量和加工精度的影响不容忽视。而车削加工中利用提高切削速度来加快切削热的散出的方法是无法在深孔加工中适用的,这将会使得刀具急速磨损并且无法排屑。由于无法在半封闭的状态下将传感器安装在切削刃周围,所以钻削区域的切削温度很难直接测得。而国外的红外线传感技术只能测量钻削区域的平均切削温度,很难将钻削温度场分布情况深入研究下去。
随着计算机技术在各个领域的发展与应用,现在可以利用有限元相关软件对深孔钻削过程温度场进行模拟分析,节省了大量的人力物力。本文采用有限元仿真软件 Deform-3D 对喷油器体深孔加工过程进行仿真实验,以获取精确的切削温度场分布情况。通过仿真试验分析切削参数对切削温度场的影响规律。
1、深孔钻削温度场仿真
1.1 仿真模型的建立与简化
因为 Deform 的建模功能不强,所以本文利用三维软件 UG( Unigraphics NX)建立枪钻钻头模型,为了更易观察钻头部位的钻削力与切削温度,提高仿真的准确性,降低运算成本,本文建立枪钻的钻头的三维仿真模型,并简化了刀具的某些实体结构,省掉了一些工艺尺寸,如图1所示。
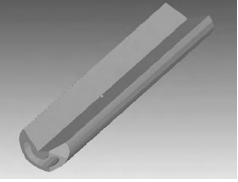
图1 简化的枪钻三维模型
所建立刀具的几何参数如表1 所示。因为只是简化了很细微的部分,所以不会对枪钻深孔加工的仿真结果产生巨大的影响。
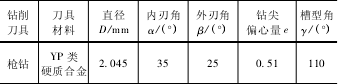
表1 枪钻的几何结构参数
本文的仿真工件为高压共轨柴油机喷油器,如图 2 所示,由于喷油器体结构复杂,不对工件模型进行相应简化的话,将会浪费巨大的硬件资源来对其进行建模仿真。所以本文将喷油器体简化为半径 10 mm,高度 20 mm 的圆柱体,如图 3 所示,并设定合理的边界条件使其模拟出喷油器体的加工状态。
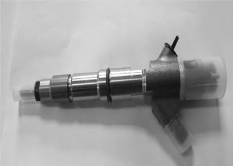
图2 高压共轨柴油机喷油器
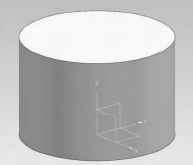
图3 简化的喷油器体有限元分析模型
1.2 钻削条件及仿真参数的确立
在本文中,使用枪钻来作为深孔钻削中的加工刀具,规格是Φ2.045 ×110mm,被加工件喷油器体的材料是20CrMo,工件材料物理参数如表2所示。被加工孔是喷油器体的进回油孔,孔径为 Φ2. 05 mm,加工精度上极限为+0.03mm,下极限为-0.02 mm,深度为 58 mm。
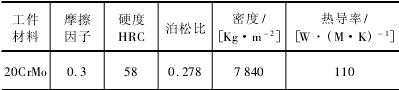
表2 工件材料物理参数
本文主要有切削速度,进给量,钻削深度三个钻削参数,由于喷油器体进油孔尺寸已定,所以切削深度定为58mm,转速n=1100~1400 r/min,进给量 f=0.06 ~0.15 mm/r。对切削速度和进给量分别选取4组加工数据,一共设计 16组仿真实验,仿真数据如表3所示。
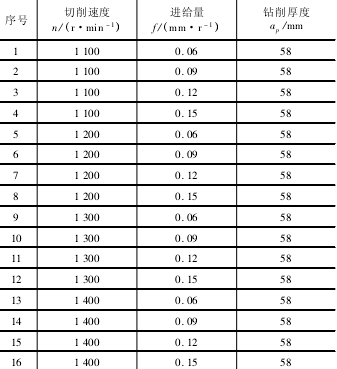
表3 仿真实验数据正交表
1.3 仿真前处理及边界条件设置
预处理作为仿真前必不可少的准备工作,主要分为确立仿真参数,划分刀具及工件网格和设定边界条件三个步骤。
(1) 仿真参数
单位系统选择 SI( le Système international d'unités) 单位制,类型选择 Machining-Transient,加工形式选择钻孔,切削速度 1100 ~ 1400 r/min,进给量 0.06 ~ 0.15 mm/r,环境温度设为 20℃ ,摩擦因子 0.6,热传导系数 110 W/( M·K) 。
(2) 刀具及工件网格划分
选择从档案读取刀具形状,导入格式为“STL”的刀具模型,并在 Deform-3D 中建立工件模型,因为使用相对网格化分方式要指定固定单元的数目,无论物体形状多么复杂,单元的数量是恒定的,所以使用相对尺寸划分刀具初始网格数为 20 000 个; 而使用绝对网格划分方式要指定最小单元尺寸,随着物体的复杂,单元数也随之增加,所以使用绝对网格尺寸划分工件,取进给量的 1/3即,0.03mm。
本文的加工仿真中,枪钻钻头与工件的接触部分是切削温度的主要分布区域,为了使仿真结果更加精确,需要对钻头刀刃部分以及工件主要加工区域的网格进行重划分,为了最大限度地减少几何失真,保证预设切削参数的准确性,设置应变权重因子为 0.65,因变率权重因子为 0.35。刀具和工件网格划分效果图如图4 和图 5所示。
(3) 边界条件的设定
选择刀具为刚性类型,工件为塑性类型,设置模拟步数数量为3000,每隔 25 步一保存,同时设置钻削深度为 10 mm作为停止条件,当总步数达到 3000 步或者钻削深度达到10mm,仿真就会结束。
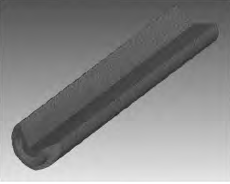
图4 刀具的网格划分
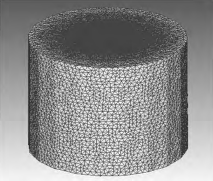
图5 工件的网格划分
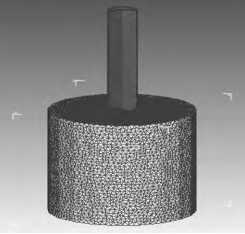
图6 枪钻加工仿真模型
为了防止工件在仿真过程中移动,设置工件的外圆周面 X,Y,Z 三个方向上的速度为零,即限制工件表面所有的自 由度,将环境温度设置为20℃ ,刀具和工件所有表面与外界做热交换,刀具进给方向为-Z 轴,并绕Z轴做旋转运动。选用Usui's 模型作为刀具磨损模型,其中 a、b 是模型中的实验校正因子,根据以往经验,系数 a 设为 0.0000001,b 为855,最后检验参数设置,生成DB 文件并进行仿真,枪钻加工仿真模型如图6所示.
2 、仿真结果处理及分析
回到 Deform-3D 主窗口选择 DB 文件,点击runnning 进行仿真计算,图7为Deform-3D 仿真过程。
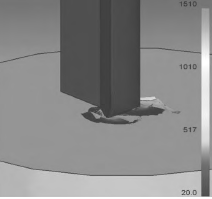
图7 仿真过程
仿真结束后,切削温度分布情况可以通过 De-form-3D 的后处理器模块查看,不同的参数条件对应着 不同的仿真结果。一般刀具切削过程中切屑会带走 80% 的切削热,但是深孔钻削只会带走 40%,其他切削热基本传到工件本身和枪钻上。因为切屑在第一变形区开始形成时,切屑在没有冷却的情况下带着巨大的切削热以很大的速度继续与刀具前刀面产生相对运动,使切屑温度继续升高,所以最高温度出现在切屑与刀具的接触面上,刀具的最高温在钻头的刀刃上。
2.1 正交实验仿真结果处理及分析
本次喷油器体深孔加工仿真实验选取切削速度、进给量和切削深度 3 个工艺参数作为试验因素,每个因素的变化选取 3 个水平值。通过正交试验,可以有效地减少实验次数,降低实验成本,从而确定最适加工条件,提高喷油器体深孔加工加工效率和改善加工质量.
本实验切削温度随进给量和切削速度变化曲线如图8所示,随着切削速度和进给量的逐渐增大,喷油器体枪钻加工过程中的最高温度也逐渐升高。由此可知,枪钻加工过程中进给量和切削速度都与切削温度成正相关关系。根据仿真结果可以看出,当n=1200 r/min,f = 0.12 mm/r 时,切削温度上升幅度最小,所以这是最适量的加工条件。
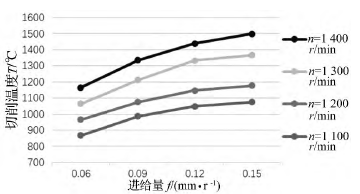
图 8 切削温度变化曲线图
2.2 单一变量因素仿真实验结果处理及分析
2.2.1 切削速度对切削温度的影响
保持进给量 0. 09 mm/r,钻削深度 58 mm 不变,选取切削速度分别为 1100 r/min、1200 r/min、1300 r/min 进行钻削仿真。在后处理器里提取钻头最高切削温度数据,得到每个切削速度对应的钻头最高切削温度变化曲线如图 9 所示。
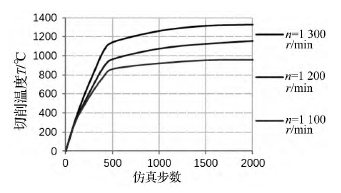
图9 切削速度对切削温度变化曲线图
由曲线图可知,当进给量一定时,深孔加工过程中的最高温度随着切削速度的增大而增大,最后趋于平稳。所以切削速度与切削温度成正比。
2.2.2 进给量对切削温度的影响
保持切削速度 1 200 r/min,钻削深度 58 mm 不变,选取进给量分别为 0.06mm / r、0. 09 mm / r、0.13 mm / r进行钻削仿真。在后处理器里提取钻头最高切削温度数据,得到每个进给量对应的钻头最高切削温度变化曲线如图 10 所示。由曲线图可知,当切削速度一定时,深孔加工过程中的最高温度随着进给量的增大而增大,最后趋于平稳。所以进给量与切削温度成正比。
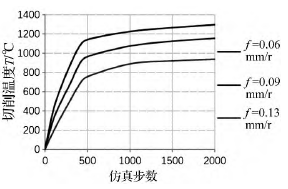
图10 进给量对切削温度变化曲线图
3 、结论
通过构建高压共轨喷油器体深孔钻削三维仿真模型,确立仿真参数及边界条件,并通过单一变量因素仿真试验,本文利用有限元仿真软件 Deform-3D 对喷油器体深孔加工过程进行动态模拟。仿真结果表明,随着钻入深度的增加,枪钻钻头的温度也迅速增大,并且最后逐渐稳定; 深孔加工中最高温度出现在切屑与刀具的接触面上; 进给量、切削速度都与切削温度呈正相关关系。本文研究结果为今后深孔加工切削参数优化,延长刀具寿命提供一定的理论指导。
来源:江南大学 机械工程学院,中国第一汽车股份有限公司 无锡油泵油嘴研究所
投稿箱:
如果您有机床行业、企业相关新闻稿件发表,或进行资讯合作,欢迎联系本网编辑部, 邮箱:skjcsc@vip.sina.com
如果您有机床行业、企业相关新闻稿件发表,或进行资讯合作,欢迎联系本网编辑部, 邮箱:skjcsc@vip.sina.com