深长孔提高镗孔精度的操作技巧
2018-5-9 来源:中国中车株洲电力机车有限公司 作者:杨和仲
【摘要】本文论述了SS4机车构架牵引座的重要性、加工的精度要求及加工的难度,据此,经过详细的工艺分析,找出了提高功效、适合的刀具、改进刀具角度及改进刀具刃磨的方法,解决了加工难,保证加工精度难的问题。
关键词:薄板;群钻;刀具
1. 概述
S S4机车构架牵引座是电力机车的主要部件,牵引系统质量的好与坏,可直接影响机车的牵引质量,机车构架牵引座是一关键部位,它的加工难度大、尺寸要求精度高,工件装夹刚性差;四个孔f60+0.048 +0m m孔的同轴误差要求为0.08m m。加工中总有孔钻飘位移误差较大的现象,表面粗糙度值过高达不到图样要求,尺寸精度难以控制。如图1~
图3所示。
2. 牵引座镗孔工艺分析
(1)构架属于Q235A大型板料焊接结构。16m m板料上钻孔,强度低、刚性差,板易产生变形。
(2)为达到图样技术要求,保证孔的同轴度要求,应一次将孔钻通,镗床主轴伸出过长,再加加长钻套,致使刀具刚性差,镗削时轴向跳动,钻头强度差,难保证钻头的定心精度。
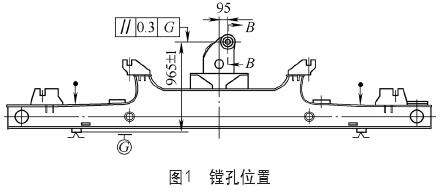
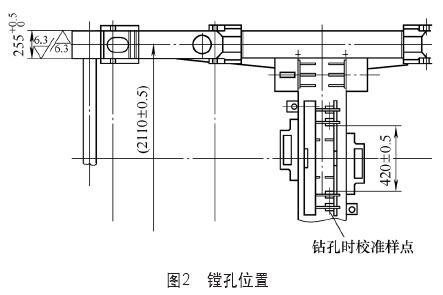
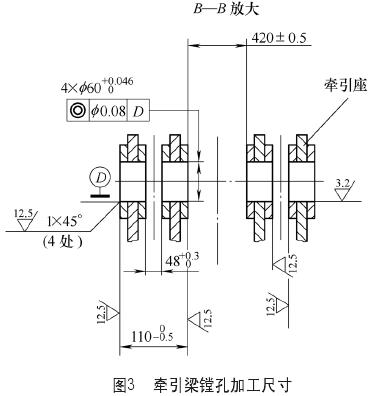
(3)镗孔时,由于主轴,加长套轴向伸出过长,刚性差。产生振动,钻削后孔表面有波纹。表面粗糙度值高。
3. 解决牵引座镗孔的方法
构架属于大型板料焊接结构,用标准麻花钻头进行钻削,定心不是很理想,容易出现飘移,经过对钻头切削力分析,在钻削过程中,所有切削刃都要承受轴向力FX,径向力Fy及切向力Fz。径向力Fy对钻孔质量影响很大,造成孔经的扩大和孔口偏斜,影响钻削力的因素是螺旋角、顶角、横刃斜角、后角等。螺旋角越大,则切削刃的前角愈大,并改善了排屑情况,轴向力FX与扭矩M都显著降低。但当螺旋角β>30°时,其影响减小。
标准麻花钻在切削部分几何形状上存在一些问题,沿主切削刃各点前角值差别悬殊(由-30°~ +30°),横刃上的前角竟达-54°~-60°,造成较大的轴向力和扭矩,使切削条件恶化。棱边近似为圆柱面的一部分,副后角为零度,摩擦严重,在主、副切削刃相交处,切削速度最大,散热条件最差,剧烈的摩擦,使切削刃磨损很快。两条主切削刃很长,切屑宽,各点切屑流出速度相差很大,切屑呈宽螺卷状,排屑不畅,切削液难于注入切削区。横刃较长,其前、后角与主切削刃后角不能分别控制。
经过改进,修磨效果不好。后将麻花钻改为群钻磨法,效果明显改善,原因是群钻综合应用了钻头的改良措施,经过试验证明,群钻可以解决加工过程中出现的问題,群钻切削部分的改进与效果如下:
①横刃及其附近的主切削刃上的各段前角都有不同程度的增大,圆弧刃(BC)平均增大10°;内刃(CD)平均增大25°,横刃增大4°~6°,大大改善了切削条件。
②圆弧刃不仅能起到良好的分屑作用,由于它在工作时切出一个凸形环圈,切削时能够很好定心,钻头不易偏摆,增加了钻削过程中钻头定心的稳定性。
③横刃缩短,前角增大,显著改善了心部的恶劣切削条件,可大大提高进给量,减小摩擦热。为保证横刃处一定的强度,应尽可能降低钻尖高度h,适当增大内刃顶角。
④由于群钻的切削刃锋利,切削变形小,加工钢件时,与标准麻花钻相比,其轴向力可降低35%~50%,扭矩可小10%~30%,使用寿命提高3~5倍,在保持同样使用寿命情况下,生产率可显著提高。此外,加工精度与表面质量也有所改善。
群钻是一种先进的麻花钻磨削方式,是早已得到了肯定的技术,由于其磨削难度较高,需操作者熟练掌握刃磨技术,如果解决了刃磨问题,必能获得更广泛应用。由于粗镗时余量的不均匀,致使精镗时产生振动,加工表面产生波纹对孔质量的影响极大,造成如下问题:①降低镗削表面的质量。②降低了刀具的使用寿命。③降低了生产效率。④降低了镗床的几何精度和运动精度。
由于镗孔的刀杆过长、刚性差,无法加装辅助支撑,故只能在刀具上想办法。对刀具切削力的分析。一般情况下,主切削力FY最大,FY、FX小一些。随着刀具几何参数、刃磨质量、磨损情况和切削用量的不同,FY、FX相对于FZ的比值在很大的范围内变化;FY=(0.15~0.7)FY;FX=(0.1~0.6)FZ。
镗刀采用较大的前角、后角和主偏角,以降低切削力和功率消耗,使切削轻快、减轻振动、减小摩擦、降低切削热;大的负值刃倾角,刀尖位于主切削刃的最低点,故刀尖部分强度较好,比较耐冲击和振动,避免崩刃现象的发生,控制了切削流动的方向。在切削用量上采用低速(30~50r/min),小进给(0.1~0.18mm/r),可以使刀尖产生微量积削瘤,增大前角,保护了刀尖,使切削更加轻快,保证工件得到较高的表面质量。
4. 结语
改进后的效果,提高了工作效率。钻孔基本无钻飘的现象发生,钻孔时间比原来的缩短1/3。由于改进了刀具角度,基本无振刀现象,表面粗糙度值有所下降,尺寸精度达到了要求。加工一个构架牵引座时间,由原来的270min缩短为200min。
投稿箱:
如果您有机床行业、企业相关新闻稿件发表,或进行资讯合作,欢迎联系本网编辑部, 邮箱:skjcsc@vip.sina.com
如果您有机床行业、企业相关新闻稿件发表,或进行资讯合作,欢迎联系本网编辑部, 邮箱:skjcsc@vip.sina.com