航空钛合金零件深孔钻削工艺
2016-8-15 来源:沈阳黎明航空发动机(集团)有限责任公司技 作者:潘玉良 姜雪梅 姜莹
摘要: 针对钛合金深孔加工技术难题,采用枪钻加工某航空钛合金零件的深孔。在深入分析零件工艺特性的基础上设计了合理的工艺方案,改进了钻削走刀工艺路线,并通过工艺试验验证了钻削工艺参数。结果表明,在合理制定的工艺方案中,预钻孔深度稍大于2 倍孔直径的长度可使枪钻切削滞后于枪钻加速,有效提高刀具寿命和加工质量;通过优选钻削工艺参数可提升钛合金深孔结构的加工效率和精度。
关键词: 航空钛合金;深孔;枪钻;钻削
钛合金由于其比强度高、耐蚀性好、耐热性高等特点,在航空航天领域得到大量应用,但是钛合金的机加性能差成为制约钛合金应用的技术瓶颈[1 -6] 。钛合金切削加工特点包括:(1)刀具切屑单位接触面积上的切削力大,使刃尖部位应力集中,容易造成刀具磨损或破损;(2)黏刀现象严重,容易引起严重的黏结磨损;(3)由于刀具中的TiN 和TiC 等与被加工的钛合金之间易发生化学反应及熔覆现象,导致钛合金与刀具之间有很强的亲和力,以致造成刀具严重磨损[7 -9] ;(4)由于钛合金具有较强的冷作硬化特性,如果进给量过小,导致加工道次增加,加剧冷作硬化层对刀具的磨损。因此,钛合金加工过程中应使刀刃的粗糙度尽可能小,以保证排屑流畅并避免崩刃,并尽可能使用导热性能良好的、强度高的细晶粒钨钴类硬质合金刀具,为提高刀具耐用度,应采用较小的前角,后角应比切普通钢的后角大,刀尖采用圆弧过渡刃,刀刃上避免出现尖角[10] 。以往的钛合金小尺寸系列深孔加工通常采用接长麻花钻[11] ,不仅无法实现自动连续排屑,而且冷却润滑液难以供入。每钻削大约1 ~ 2 倍孔径的深度就必须退刀排屑,不仅加工精度低、表面粗糙度差,加工效率低、劳动强度大、质量难以保证,而且很容易引起“堵屑”或者折断钻头,造成更大的加工困难甚至报废工件。而枪钻则是一种优质高效的深孔钻削工具,具有排屑性能好、加工精度高、加工效率高以及钻头寿命长等优点[12 -13] 。因此本文采用枪钻加工某航空钛合金零件的深孔,在深入分析该零件加工工艺难点的基础上,合理设计深孔加工工艺方案,选取不同钻削参数进行钻削试验,分析得出钛合金深孔枪钻加工最佳工艺参数。
1、某钛合金零件深孔工艺性分析
某钛合金零件设计有18 个直径为6 mm、深度为122 mm、公差等级为H9 的孔结构,孔的长径比超过20。由于钛合金具有比强度高、热强性高、耐蚀性好、化学活性大、导热性能差和弹性模量小等特点,在进行深孔钻削加工时极易出现烧刀、堵屑、刀具磨损快、工件加工硬化以及深孔的弯曲和偏斜等问题[14] ,若采用常规钻头和外冷却机床加工,钻头刚性差容易偏摆导致切削失效,同时冷却液难以到达切削刃部位,切削时钻头寿命较短且极易断裂,所以在方案设计时选用枪钻和具有内冷功能的数控机床进行深孔加工是必要的工艺选择。
2、钻削试验与方案
2. 1 试验条件
(1)机床:试验用机床为具有高压内冷功能的数控机床,控制系统为西门子840D,冷却压力最高可以达到80bar,切削液为不含卤族元素的乳化液;
(2)刀具:试验用枪钻为伊斯卡刀具制造公司的合金刀具,切削刃部分采用硬质合金材料,其结构如图1 所示;
(3)刀柄:选用HSK A 100 ER32 × 100 和ER32 SEAL 15 -16 密封卡簧;
(4)试验件:材料为TC11,经过固溶和时效热处理,硬度达到HRC35 ~ 40,规格为Φ300 ×180 mm;
(5)装夹:采用硬三爪卡盘,装夹压力45 bar;
(6)粗糙度检测仪:检查孔加工表面质量。
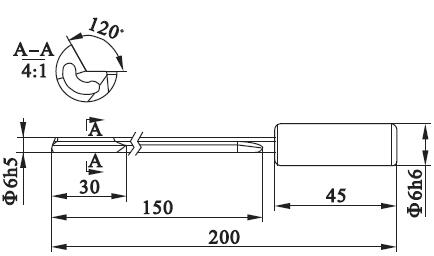
图1 枪钻结构示意图
2. 2 钻削工艺方案
工艺方案决定零件具体的加工过程,影响加工效率和加工精度。由于该零件所加工的孔为长径比大于20 的深孔,工艺方案的确定就更加重要。枪钻的使用与普通钻头不同,除了预钻孔要有严格的要求,切削参数还得进行精确控制,才能既保证质量,又尽可能缩短加工时间,同时提高刀具的使用寿命。所以要想全面掌握深孔钻削加工工艺,使枪钻加工深孔时能够达到满意的效果,必须熟练掌握枪钻加工系统(包括刀具、机床、夹具、附件、工件、控制单元、冷却液和操作程序)的性能,根据工件的结构及工件材料的硬度以及枪钻专机的工作情况和质量要求,选择适当的切削速度、进给量、刀具几何参数、硬质合金牌号和冷却液参数[15 -16] 。通过切削试验,摸索加工经验,不断积累和改进切削参数,才可以使工艺方案能够加工出合格的产品。本文设计具体钻削方案如下:
(1)打点:用中心钻在孔的端面上预钻中心点,使钻削的位置更加精确。由于打点刀具加工深度较小,切削热很小,排屑相对顺畅,采用普通合金中心钻外冷就能满足加工要求;
(2)预钻引导孔:用Φ5. 5mm 的钻头预钻2倍枪钻直径深度的孔作为枪钻加工时的引导孔,由于钻头直径较小且切削较深,采用内冷合金钻头提高冷却效率,以保证预钻孔的加工质量;
(3)修正引导孔:用端刃铣刀将引导孔进一步修正,保证引导孔的位置和尺寸符合要求,从而使枪钻在加工时产生自导向;
(4)深孔钻削:将枪钻沿引导孔按较低的切削速度导入预定加工位置,然后高速进行深孔钻削,完成深孔加工并保证设计要求。
2. 3 钻削参数确定
枪钻属于高速切削刀具,虽然每转进给量较低,但其转速高,每分钟进给量远大于麻花钻[7] 。根据加工经验和枪钻合金材料的能力,进给量采用适中的0. 03 mm / 转,试验低、中、高3 组转速参数,分别为2 000 转/ 分钟、2 500 转/ 分钟、3 000转/ 分钟,换算成每分钟进给量则分别为60 mm /分钟、75 mm / 分钟和90 mm / 分钟。
2. 4 枪钻切削程序设计
图2 是枪钻钻削循环图,枪钻先以快速进给方式运动到安全平面,再以枪钻导入进给量运动到枪钻工作起始平面(此时枪钻产生一定量的切削,但切削量很小),再以枪钻切削进给量进行深孔加工,到达底部后以快速进给或设定的进给运动到回退平面,从而完成一个孔的钻削。
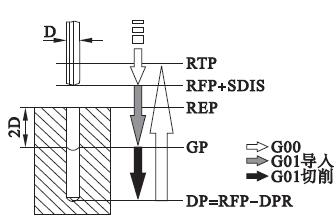
图2 枪钻钻削循环图(GP - 起始平面;RFP - 基准平面;RTP - 退回平面;SDIS - 安全距离;DPR - 相对基准平面的钻削深度)
由于在进行钻削试验时,需要反复调整钻削参数,若采用一般的G 代码程序,调整过程较为繁琐,容易发生误操作。由于该零件每个孔钻削循环相对固定,18 个孔沿圆周均布且十分规律,所以可以采用西门子循环编程指令和高级编程指令简化编程,用赋值语句将所有需要反复调整的切削参数进行参数化设置,从而方便程序的调整。枪钻试验加工用程序和说明如下:
N0001 R1 =500;;;枪钻导入转速
N0002 R2 =15;;;枪钻导入进给量
N0003 R3 =3000;;;枪钻切削转速
N0004 R4 =90;;;枪钻切削进给量
N0005 R5 =125/ 2;;;孔的分度圆半径
N0006 R6 =200;;;退回平面
N0007 R7 = -122;;;钻削深度
N0008 R8 = -12;;;枪钻工作起始平面
N0009 R9 =360/ 18;;;两孔间夹角
N0010 R10 =0;;;基准平面
N0011 R11 =10;;;安全平面
N0012 R12 =0;;;钻削起始角度
N0013 TLCH1(" tool" , -90,0);;;调刀命令
N0014 G54
N0015 G94 M3 =3 S3 = R1;;;设置导入转速
N0016 G0 X1 = R5
N0017 Z1 = R6
N0018 TLZTRANS(R5,R10);;;坐标系转换
N0019 G0 X1 = 0 Y1 = 0 Z1 = R11 C1 = R6M3 =8 M99;;;高压冷却液打开
N0020 Z18HOLES:N0021 G1 Z1 = R10 + 1F3000
N0022 Z1 = R10 +1 F = R3
N0023 G1 Z1 = R8 F = R2;;;枪钻以R2 进给速度导入预钻孔
N0024 S3 = R3;;;设置枪钻切削转速
N0025 G1 Z1 = R7 F = R4;;;枪钻加工深孔
N0026 S3 = R1
N0027 Z1 =5 F500;;;枪钻加工后退回
N0028 G1 Z1 = R11 F1000
N0029 R12 = R12 - R9
N0030 G1 C1 = R12 F3000
N0031 IF R12 > -360 GOTOB Z18HOLES
N0032 G1 Z1 = R6 F3000 M3 =9
N0033 TLZTRANS(0,0)N0034 M3 =5
N0035 GOHOME
N0036 M30
3、试验结果分析与改进
经过6 次深孔钻削试验,共钻了108 个孔,消耗2 把枪钻,其中切削试验1、2、3 顺次进行,用的是同一把枪钻,切削试验4、5、6 顺次进行,用的是另一把枪钻,试验所用加工参数和试验结果见表1。对表1 数据进行分析,钻削过程主要是枪钻导入和枪钻钻削,随着导入速度S1、导入进给F1、切削转速S2 和切削进给F2 的提高,加工时间呈减少趋势,切削试验2 所用参数最小,加工时间最长,而切削试验5 所用参数最大,加工时间最短。随着进给量和切削转速的增加,切削力也相应增大;同一把枪钻加工过程中,孔的加工数量增加,刀具磨损逐渐加大,切削时刀具的偏摆和切削力也逐渐增大,所以孔中心的直线度越来越差;而刀具磨损后,孔壁的粗糙度值也增大。每把枪钻在加工完最后一组孔后,切削刃明显磨钝,其表面出现较明显的毛茬儿和局部微小崩刃,说明刀具马上就会进入急剧磨损阶段,也说明切削参数的提高对刀具寿命的影响较大。
在前5 个试验中,程序运行到“N0024”段,刀具转速迅速由S1 提升至S2 的同时,刀刃部分开始全部接触到零件待加工材料,所以瞬间对刀具产生冲击,发出1 秒钟左右尖锐的切削声音,而在钻速逐渐增大到一定范围时,在试验5 中产生了崩刃现象。经过分析,如果能将枪钻加速的时间点和全部接触零件的时间点错开,使后者稍稍延迟,待完成加速后再进行切削,就会避免刀具同时受切削力和加速扭力的双重作用,从而减小零件对刀具的作用力,降低崩刃的风险,提高刀具的寿命。所以,试验6 将枪钻导入运动的转速适当降低的同时,还将预钻孔和扩孔的深度在2 倍孔径的基础上,增加一个Δ 值(约0. 3 mm),使枪钻切削被适当延迟(改进的钻削过程见图3)。虽然此时仍使用第2 把刀具,但在加速瞬间没有产生尖锐的切削声音,加工后刀具上的崩刃部分未发现增大趋势。加工后粗糙度变化趋势明显,但孔的直线度变化较小,说明刀具磨钝后对孔的直线度影响较小,对表面粗糙度影响较大,而刀具产生崩刃是导致刀具寿命降低的主要原因。
表1 钻削试验数据统计结果
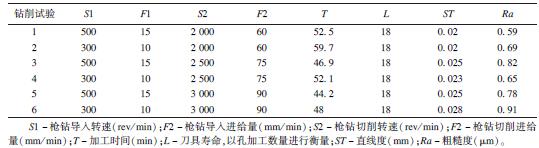
结合以上试验数据和分析结果,应用改进后的钻削循环,综合考虑质量、效率和刀具成本,进行了参数改进和二次验证(验证结果见表2),仅用一把枪钻加工了90 个孔,刀具寿命有一定的提高,表面粗糙度和直线度均满足要求,切削过程比较顺畅和平稳,枪钻加工产生的切屑(见图4)95% 以上小于3 mm,使用80 bar 压力的内冷切削液能迅速排出切屑并冷却刀具和零件,可以满足零件的优质、高效、低消耗加工需求。同时,枪钻在第5 组加工中极速磨损,在正式零件加工时,要将换刀点设置在第4 组孔加工后。
表2 钻削验证数据统计结果
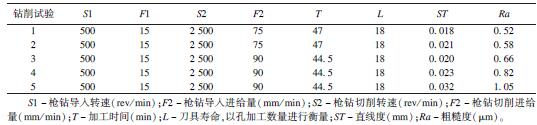
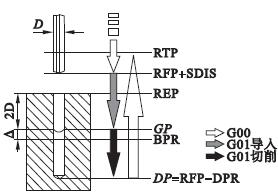
图3 改进后的钻削循环图
(BPR - 相对基准平面的引导孔钻削深度)
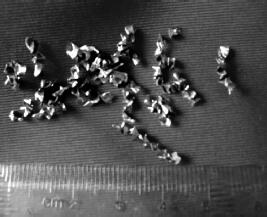
图4 枪钻钻削产生的切屑
4、结论
(1)钛合金零件深孔加工可采用打点、预钻孔、扩孔、深孔钻削的加工方案;
(2)预钻孔深度要稍大于两倍孔直径的长度,使枪钻切削滞后于枪钻加速,可有效提高刀具寿命和加工质量,采用高压内冷方式能充分提高枪钻的加工能力;
(3)本文所选定的试验参数可为实际零件加工参数的确定提供必要依据,有效保证钛合金深孔结构的加工效率和精度。
投稿箱:
如果您有机床行业、企业相关新闻稿件发表,或进行资讯合作,欢迎联系本网编辑部, 邮箱:skjcsc@vip.sina.com
如果您有机床行业、企业相关新闻稿件发表,或进行资讯合作,欢迎联系本网编辑部, 邮箱:skjcsc@vip.sina.com
更多相关信息